The raw potato counts for over 50% of the overall Carbon Footprint of Lamb Weston / Meijer's potato products. In 2016, chemical fertilizers count for 54% of the carbon footprint of the potato.
Sustainability Report: Potato Processor Lamb Weston / Meijer continues to innovate
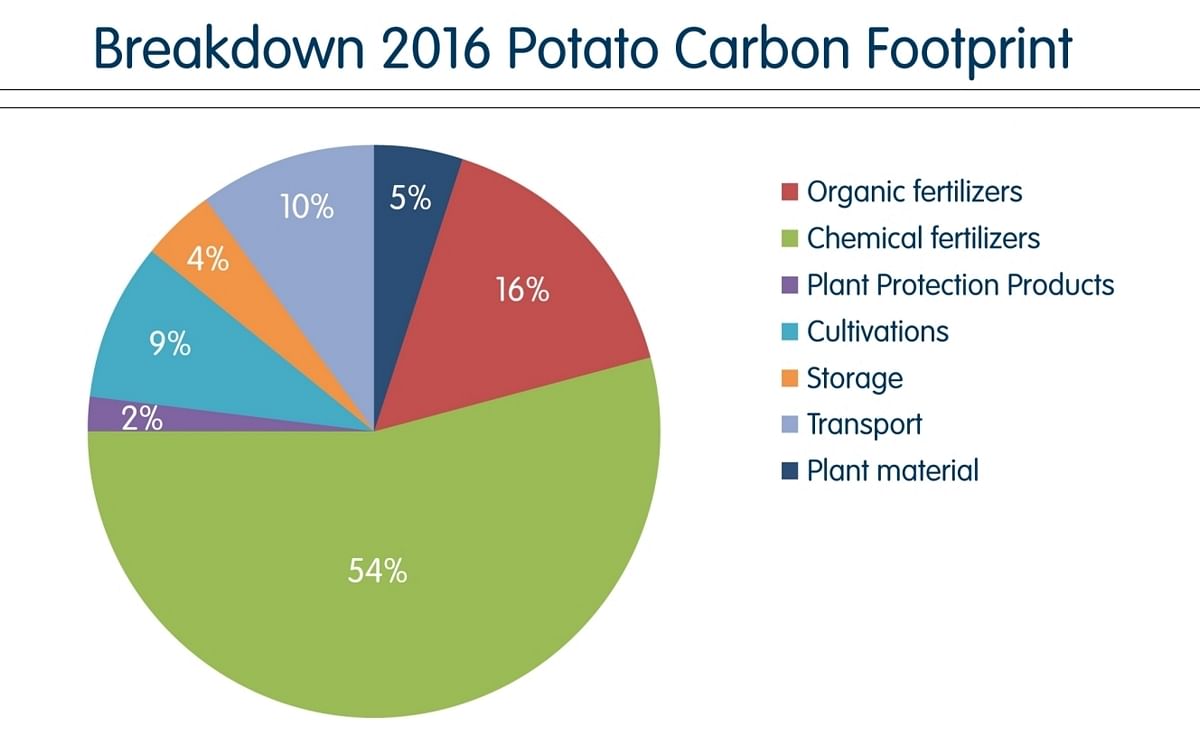
Lamb Weston's European joint venture, Lamb Weston / Meijer has published its sustainability report for 2015-2016.
This sustainability report shows that Potato Processor Lamb Weston / Meijer is well on its way to achieving the sustainability objectives it has formulated for 2020.
Over the last two years the company has made a number of significant investments to support those ambitions.
Compared to the reference year 2008, energy consumption per tonne of product has reduced by more than 21% and potato utilisation has improved by 4.5%.
Increasing transport by water and rail has reduced road transport by more than 6 million kilometres per year.
Furthermore, Lamb Weston / Meijer pre-fries more than 82% of its products in a healthier frying oil. On an annual basis this equals a reduction of 9.6 million kilos of saturated fat through its products.
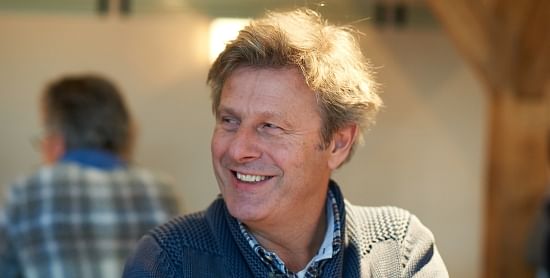
Bas Alblas, CEO Lamb Weston / Meijer
Bas Alblas, CEO Lamb Weston / Meijer:
“There’s a limit to what you can ask Mother Nature to give you. Yet, if you treat her well she will respond in kind. It’s a symbiotic relationship in which both parties need to benefit.”
“This standpoint is fundamental to our sustainability programme and strategy. We believe in give and take. In the micro and the macro. In the company and society.”
Online sustainability report 2015-2016
The full report complies with the GRI (Global Reporting Initiative) guidelines at G4 Core level. The Chapters on three of the Sustainable Six themes - Water, Energy & Emissions and Potato & Waste - have been reported at G4 Comprehensive level.The full English report and a summary in eight languages are available online.
Access Lamb Weston / Meijer Sustainability Report 2015-2016
Access Sustainability Report 2015-2016 Summary
Lamb Weston / Meijer plans to publish its next sustainability report in 2019.
The Sustainable Six
The Lamb Weston / Meijer sustainability strategy focuses on six areas, the Sustainable Six. PotatoPro will highlight the 2020 targets in each of these six areas and highlight some of the progress:
Water
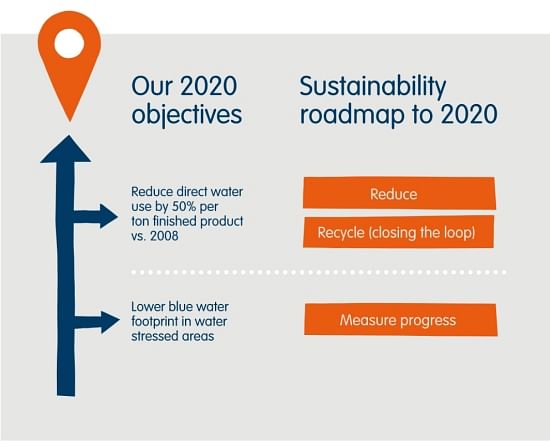
Conserving water, wherever, whenever, however
In two of its plants (Bergen op Zoom and Hollabrun) LWM has installed a Pulsed Electric Field System (PEF).
This technology replaces the traditional 'preheating' of potatoes, meaning they can be cut more efficiently into French fries, with less starch lost during cutting and less waste generated.
In the Bergen op Zoom plant, the implementation of PEF resulted in an eight percent reduction in fresh water use (70 million litres per year). In addition, energy use was reduced by five percent per year and frozen product recovery was improved
Innowater
Lamb Weston continues to scale up its experimental Innowater purification system. The Innowater system is an advanced wastewater treatment system which purifies our process wastewater to meet legal potable water standards, for reuse into our production processes.
Drip Irrigation
LWM estimates that 90% of all water used for french fries is used in agriculture - to grow potatoes and to grow oil seed crops. LWM has made a business case for the application of drip irrigation for the cultivation of potatoes in arid areas, such as in the United Kingdom
Still committed to initial targets
LWM operations saw an INCREASE in (direct) water use in the last three years and a meager 0.3% savings in water use per MT finished product compared to reference year 2008. Recent increases are attributed to crop quality, changes in the overall product mix as well as extensive construction and testing.
Despite these setbacks, LWM still intends to reach its initial targets for 2020, including a now rather ambitious looking reduction of 50% in direct water use per MT finished product.
More on conserving water, wherever, whenever, however...
Energy and Emissions
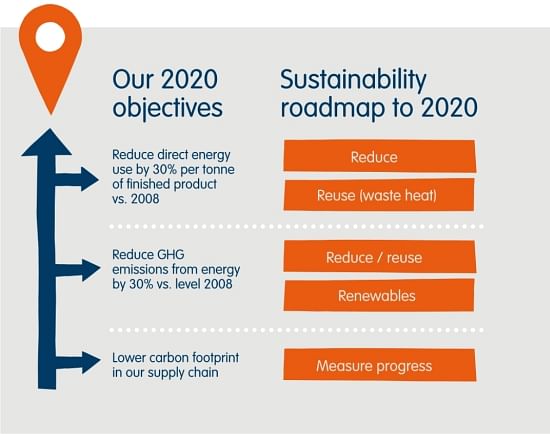
Cutting CO2-emissions with 15% from field to fork
In 2015 Lamb Weston Meijer invested in Bergen op Zoom in a Premium Product Line in response to increased demand for such products. The latest energy efficient technologies were implemented in this line to optimize processes and to drive energy efficiency.
Key examples are the optical sorting system, the eco-peeler, Pulsed Electric Field (PEF) preheating, an ultra-efficient freeze tunnel using less electricity, the latest, most efficient packaging lines and an improved wastewater treatment plant (more biogas). In 2016, the Kruiningen factory was converted from a CHP (combined heat and power) gas-turbine power plant to a High Efficiency (HE) boiler house, currently considered best-in-class. This included the addition of an additional heat exchanger in the fryer exhaust to recover waste heat that can be reused in drying and blanching. Frying vapours now also are burned in a new efficient incinerator.
Any positive effects of these changes are not yet visible in energy use data. In fact, construction and start-up is thought to have affected the carbon footprint negatively.
Direct energy use in the plant is estimated to contribute about 40% of the total carbon footprint of Lamb Weston's potato products, second only to the contribution of the agricultural contribution of the potato and vegetable oil crops estimated to be over 50%
Compared to baseline year 2008, Energy Intensity was reduced by 21.3% and energy related Emission Intensity 17.2%
Transport
LWM has Increased transport of its product to its customers by water and rail, reducing road transport by more than 6 million kilometres per year. This reduction does not positively reflect on the overall product carbon footprint, since transport to the customer is not included in this calculation.
Agricultural Carbon Footprint
A reevaluation of the agricultural carbon footprint (per ton of potatoes) showed a reduction of 17 percent compared to 2007, when the first carbon footprint study was done.
Chemical and organic fertilisers have the greatest impact on this carbon footprint, together counting for over 70% (see top image for more details). LWM is sharing the learnings from its carbon footprint study and working with the growers to further reduce the climate impact from growing and storing potatoes.
Total carbon footprint (agriculture + processing) was reduced by 14.6%.
More on cutting Energy and Emissions...
Potato and Waste
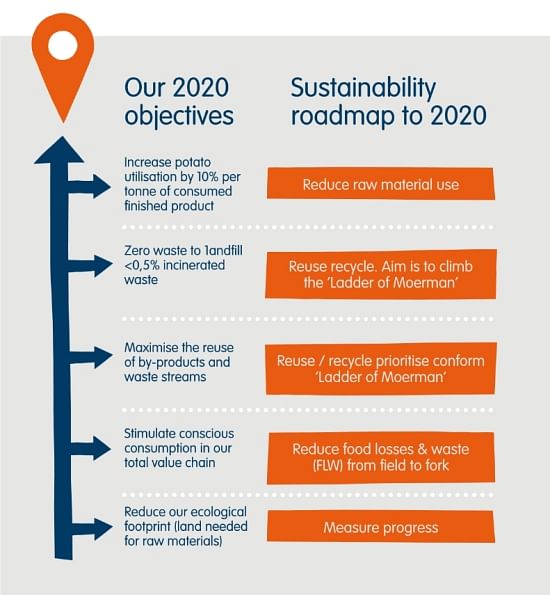
Utilising the whole potato
Lamb Weston suggests the actual progress may be even better than this number indicates, because of low average potato solids in recent years and the fact that they "decided to be brave and bold" and not correct for the changing product mix.
Results have been achieved by implementing best practices across their plants:
- Eco-peeler
LWM installed the state-of-the-art eco-peeler in four of its plants. The eco-peeler removes potato peel more efficiently than traditional steam peelers. The eco-peeler also uses 20 percent less steam per tonne of potatoes peeled.
- Model Predictive Control (MPC) system
LWM implemented Model Predictive Control (MPC) system at four of its five plants, helping to create more consistent quality levels. Model Predictive Control acts as an ‘automatic pilot’ for the production lines, adjusting process settings to optimize the process and removing subjective operator influence.
- Optical Sorting
LWM installed optical sorters in the grading process at four of its plants, sorting the potatoes on length and improving line efficiency as potatoes are sorted prior to entering the main production line. This prevents processing of the wrong size of potatoes, reducing energy usage and cutting food loss and waste.
LWM has reached a stage where hardly any waste (only 0.2%) is left from the production processes. LWM sees its next challenge as moving from good disposal to a more functional and valuable valorisation and has assigned dedicated resources to achieve this.
More on utilising the whole potato...
Employees
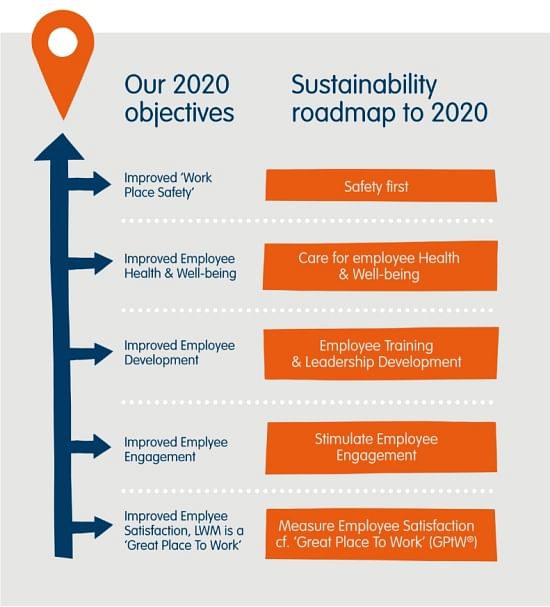
Being the employer of choice
Its 2020 objective is to improve the workplace safety, health and well-being of our employees, their development and job satisfaction. LWM wants to be a great place to work!
2016 progress has been made in particular with a 48% reduction in the Total Incident Rate (TIR) to 0.96 and a 37% reduction in Employee Turnover to 6.4%
More on Being the employer of choice...
Food Safety and Quality
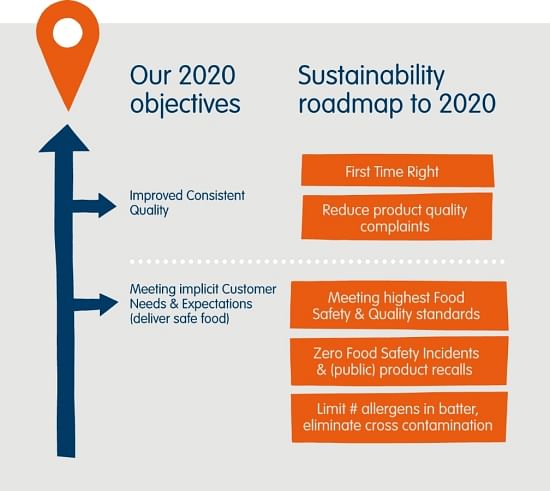
Meeting customer expectations, every day
They want to know where their food was grown and produced. In other words, they expect transparency.
At the same time, the introduction of more stringent food safety regulations and the continuing globalisation and integration of supply chains is changing the food industry.
Organisational
Lamb Weston Meijer has focused strongly on the organisational aspects of Food Safety and Quality, such as readiness, systems, methods and partnerships.
Foreign Materials
In addition to above mentioned organisational aspects, eliminating foreign material (FM) was emphasized.
Product quality complaint level is consistently low, but foreign material (FM) makes up the largest complaint category and thus offers best opportunities for improvement. Over the last 15 years LWM has implemented different options to prevent and reduce FM complaints, with optical sorting systems being the most effective.
More on meeting customer expectations, every day...
Nutrition and Health
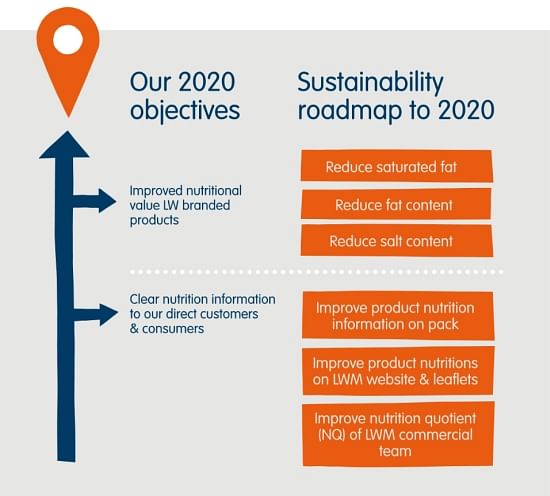
75% less saturated fat and 30% less salt
Over 82 percent of all LWM products are now fried in healthier frying oil – mostly sunflower oil – with a maximum of 12 percent saturated fats and maximum 1 percent trans fat (oil based). This reduces the amount of saturated fats by 75 percent for the majority of the total volume produced.
LWM also looks for opportunities to reduce the total fat content in both its parfried and ready to eat products.
Reducing Salt levels
LWM further reduced salt levels in our specialty fries (Lamb Weston Stealth® and Private Reserve®), going from 0.55 percent to 0.49 percent salt, a 30 percent reduction versus 2008 level. LWM developed a 30 percent reduced salt recipe for its seasoned potato products intended for the foodservice market, going from typically 1 percent to 0.69 percent salt, with adjusted spice levels to keep the desired taste. The seasoned products with reduced salt meet the 2017 UK FSA salt target and will be included in our product portfolio per 2017. Our retail products typically contain 0.49 percent salt as consumed, since 2008. We do not add salt to any of our regular French fries during processing.
Moving towards gluten free and clear and clean labels
The reduced salt recipe for seasoned potato products that will be included in LWM's product portfolio in 2017 is also gluten free.
Clear nutrition labelling has been introduced on all EMEA packaging; This includes full nutrition information in a tabular format on all packaging, even when this is not required by legislation. LWM is currently in the process of introducing the revised packaging for its export markets, starting with the Middle East region, including labelling of trans fats.
More on Nutrition and Health