Pulsemaster PEF-System: the tubers are dropped into the PEF-Treatment tank unit and the pulse generator is situated against the wall. The unit has a capacity of up to 30 t/h of tuber processing.
McCain Foods Tasmania installs Pulsemaster PEF-tech innovation, reduces water use by more than 100,000 litres per day
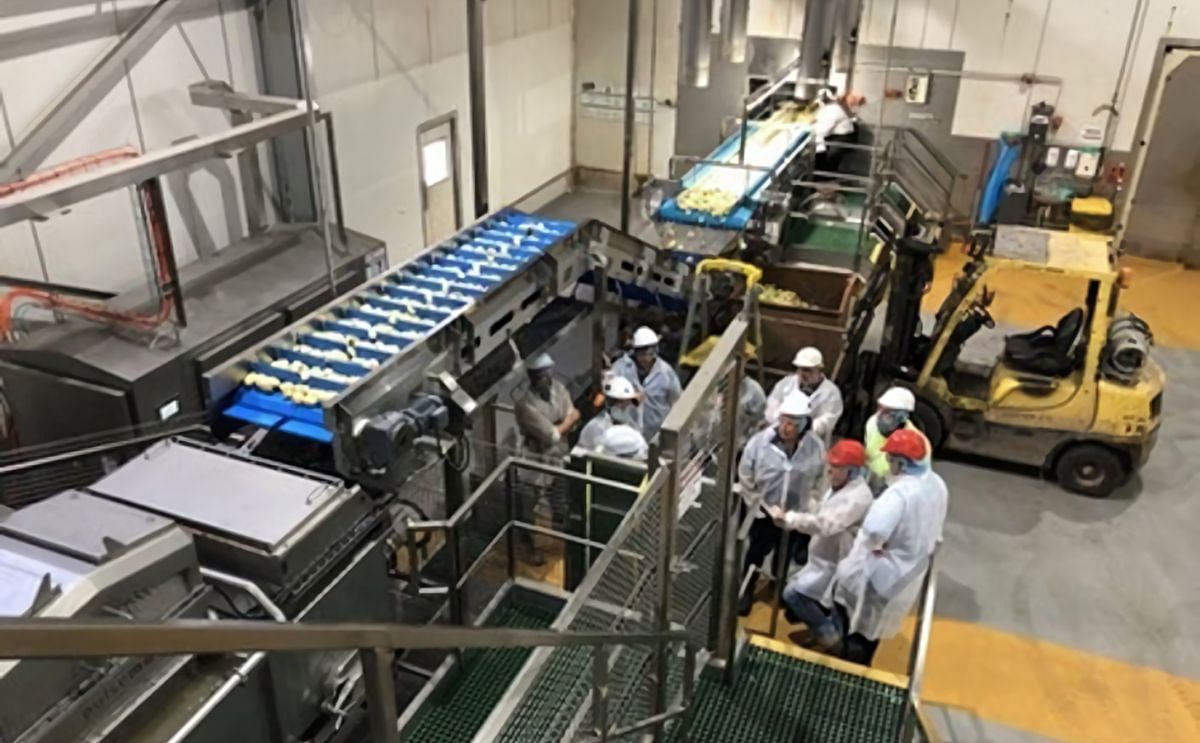
World's largest manufacturer of frozen french fries, McCain Foods has installed proprietary world-leading technology in the form of a Pulsed Electric Field (PEF) generator, as part of the company’s latest upgrade to its Smithton plant in Tasmania.
The PEF generator is another example of McCain’s commitment to producing more with less, as the USD 1.8 million project, which incorporates McCain’s proprietary technology, results in potatoes being pulsed with an electric field rather than steamed, slashing the plant’s energy and water usage
The plant has reduced water usage this year by more than 100,000 liters per day, and the PEF system will also save the plant approximately 276 tonnes of carbon each year, and around 33,000 gigajoules of energy due to the increased efficiency and reduced wastage.
Traditionally, McCain used steam – generated primarily by burning wood – to heat the water used in the pre-treatment process, which is no longer required. In addition, the electric field that is pulsed through uncut potatoes results in less oil being absorbed when the potatoes are cooked.
It is also physically smaller than the old pre-heaters, saving space within the plant – creating a brighter, more spacious work environment. Smithton operates 24 hours, seven days a week to process potatoes into a range of frozen french fries products for Australian consumers.
McCain Foods Smithton Plant Manager, Gordon Gillies, said adopting this new technology was fundamental to the company’s growth strategy, and is an important step in reducing McCain’s environmental footprint and continuing to improve its sustainable practices.
Gordon Gillies:
The PEF generator is another example of McCain’s commitment to producing more with less, as the USD 1.8 million project, which incorporates McCain’s proprietary technology, results in potatoes being pulsed with an electric field rather than steamed, slashing the plant’s energy and water usage
The plant has reduced water usage this year by more than 100,000 liters per day, and the PEF system will also save the plant approximately 276 tonnes of carbon each year, and around 33,000 gigajoules of energy due to the increased efficiency and reduced wastage.
Traditionally, McCain used steam – generated primarily by burning wood – to heat the water used in the pre-treatment process, which is no longer required. In addition, the electric field that is pulsed through uncut potatoes results in less oil being absorbed when the potatoes are cooked.
It is also physically smaller than the old pre-heaters, saving space within the plant – creating a brighter, more spacious work environment. Smithton operates 24 hours, seven days a week to process potatoes into a range of frozen french fries products for Australian consumers.
McCain Foods Smithton Plant Manager, Gordon Gillies, said adopting this new technology was fundamental to the company’s growth strategy, and is an important step in reducing McCain’s environmental footprint and continuing to improve its sustainable practices.
Gordon Gillies:
"We’re really excited to implement this cutting-edge technology at Smithton, due to the working capabilities and environmental benefits it incorporates."The propriety technology was deployed at McCain Foods’ Timaru plant in New Zealand late last year as a region-first, and now Smithton after significant success in New Zealand. Smithton halted production on January 26 this year to install the PEF generator, before resuming on February 25 and returning to full production.
"This was an opportunity to set new benchmarks in our industry as we continue to focus on becoming even more environmentally responsible. This contributes to McCain’s global commitment to reducing CO2 emissions from our plants by 50 percent by 2030."
Like to receive news like this by email? Join and Subscribe!
NEW! Join Our BlueSky Channel for regular updates!
Highlighted Company
Sponsored Content
Sponsored Content
Sponsored Content
Sponsored Content
Sponsored Content