Mydibel high bay cold storage
Potato Processor Mydibel highlights 25th anniversary
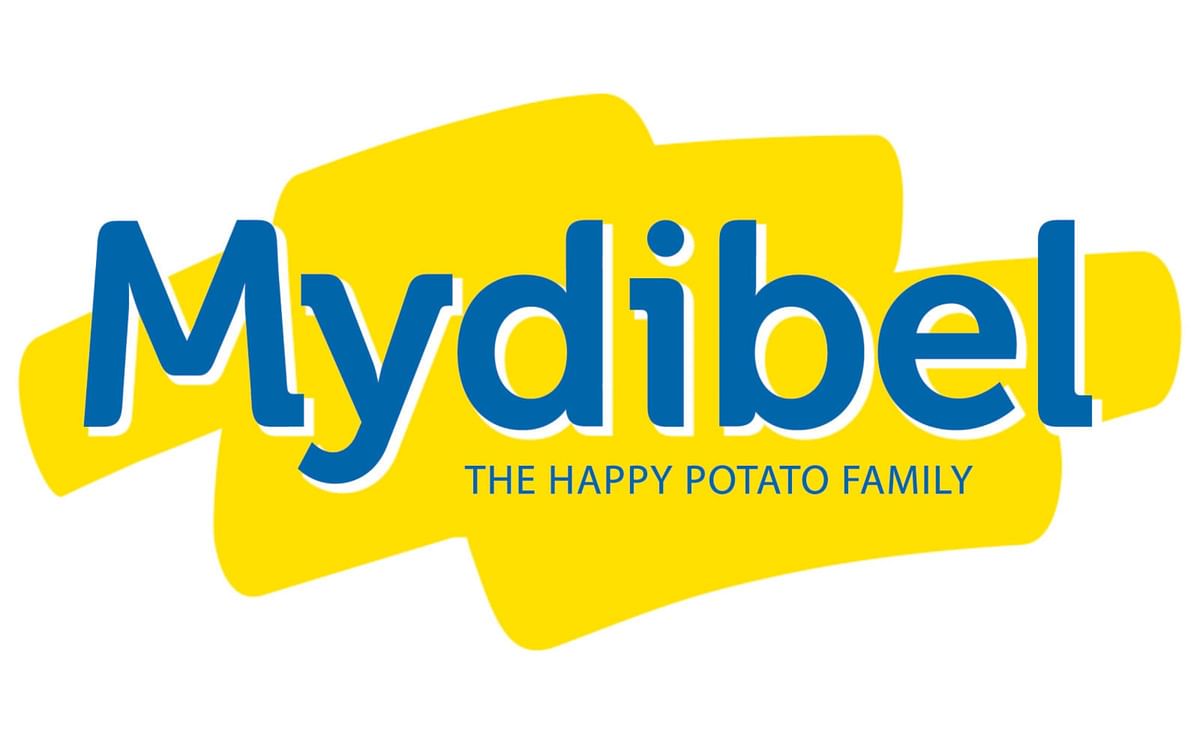
Mydibel has existed for 25 years as of 2013 and they are not letting this go by unnoticed. The site in Moeskroen has changed into a striking eye-catcher. The state of the art automatic high bay warehouse has been beautifully decorated with the image that communicates the brand name of the company. Besides the recent launch of the new corporate identity and package design, there has also been investment in the field of production and logistics.
Production, logistics, storage
In 2011 a new potato processing production unit was built where specialities such as potato croquettes, potato nuts, rosti and fresh puree could be made from fresh potatoes. This new unit is the most modern of its kind. Then came a new logistics centre with 8 loading bays and a fully automated cold store, designed to eliminate the remote storage locations and enable work to be carried out more efficiently. The distribution centre of 6000m² and 32m high can accommodate 31.000 pallets and is fully automatic. No hands come into contact with the products until the pallets are loaded. About 120 pallets can be loaded per hour.
Also particular to the automatic high rise warehouse is that the Orbiter - a compact storage system which has shuttles to allow the pallets to move in channels - can organise the pallets into the right sequencing order for the lorries. This is very unique in this sector, there is no need for a large organisational area and it is very efficient.
Flexibility
Carlo Mylle underlines the importance of this investment for the Mydibel group. "With the great competition in our sector, it is important to make continued investments so we can offer our clients a better service. This covers many areas: reduction in general costs, faster order processing, accurate order tracking, accurate inventory control, faster loading etc. We are sure this flexibility enhances our strength. The outside décor with the Mydibel brand, completely finishes the location giving it an eye catching style.
The building, with its spacious cold house aims to meet the needs of predicted long term growth. In the first place, to stock pile the production growth of recent years, and secondly to continue stocking. Planned further expansion is expected in 3 to 5 years, expanding production sites for sliced potato and potato specialities. This expansion, in turn, requires an investment in the potato washing and sorting area. In 2013 Mydibel started the construction of a new fermentation plant, the largest in the potato processing industry.
The present waste from the three production factories is taken by lorry to the final destination at the moment, to be processed at the Mydibel site into 100% green electricity and thermal energy. This will triple the green electricity and provide the company with 85% of its own energy and 25% of its own thermal energy requirements.
Source: FreshPlaza