A slippery surface for liquids with very low surface tension promotes droplet formation, facilitating heat transfer.
(Courtesy: Karim Khalil et al. / MIT)
New surface treatment developed at MIT could improve refrigeration efficiency
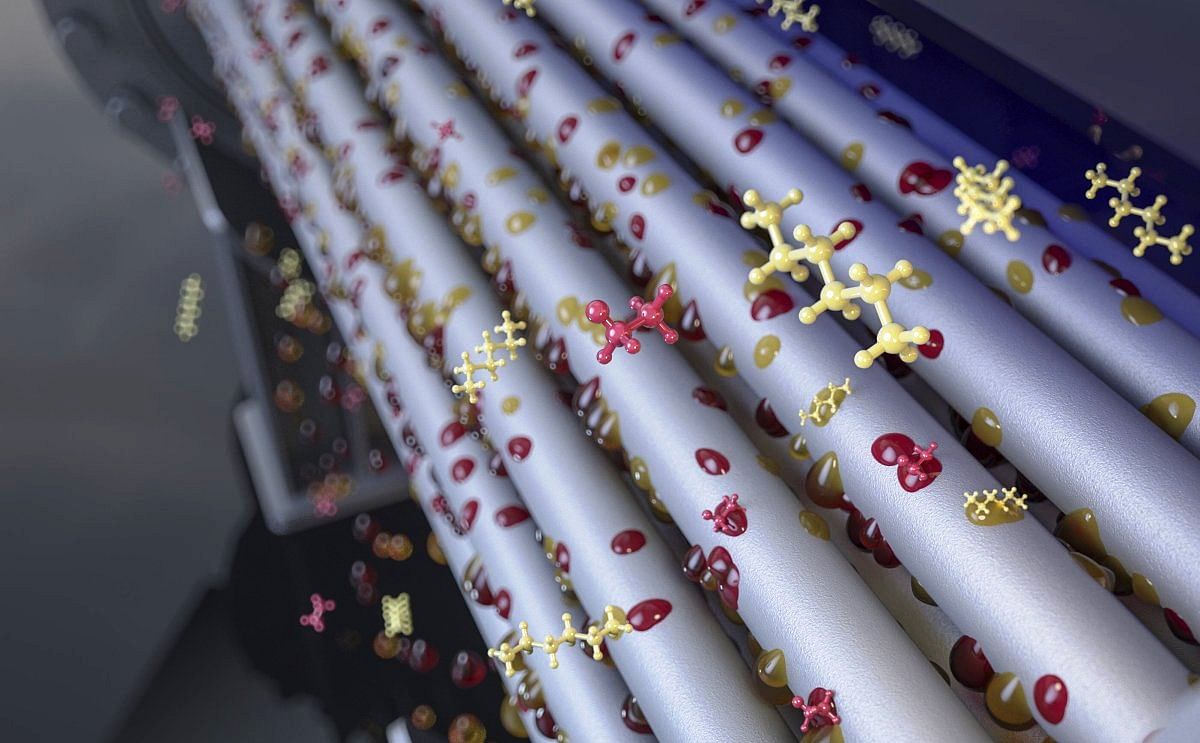
Unlike water, liquid refrigerants and other fluids that have a low surface tension tend to spread quickly into a sheet when they come into contact with a surface. But for many industrial process it would be better if the fluids formed droplets, which could roll or fall off the surface and carry heat away with them.
Now, researchers at MIT have made significant progress in promoting droplet formation and shedding in such fluids. This approach could lead to efficiency improvements in many large-scale industrial processes including refrigeration, thus saving energy and reducing greenhouse gas emissions.
The new findings are described in the journal Joule, in a paper by graduate student Karim Khalil, professor of mechanical engineering Kripa Varanasi, professor of chemical engineering and Associate Provost Karen Gleason, and four others.
Reference
Karim Khalil et. al. Grafted Nanofilms Promote Dropwise Condensation of Low-Surface-Tension Fluids for High-Performance Heat Exchangers Joule, Volume 3, Issue 5, P1377-1388, May 15, 2019But other kinds of fluids—such as those used in refrigeration systems, liquification, waste heat recovery, and distillation plants, or materials such as methane in oil and gas liquifaction plants—often have very low surface tension compared to water, meaning that it is very hard to get them to form droplets on a surface. Instead, they tend to spread out in a sheet, a property known as wetting.
But when these sheets of liquid coat a surface, they provide an insulating layer that inhibits heat transfer, and easy heat transfer is crucial to making these processes work efficiently.
Kripa Varanasi, professor of chemical engineering :
“If it forms a film, it becomes a barrier to heat transfer.”But that heat transfer is enhanced when the liquid quickly forms droplets, which then coalesce and grow and fall away under the force of gravity. Getting low-surface-tension liquids to form droplets and shed them easily has been a serious challenge.
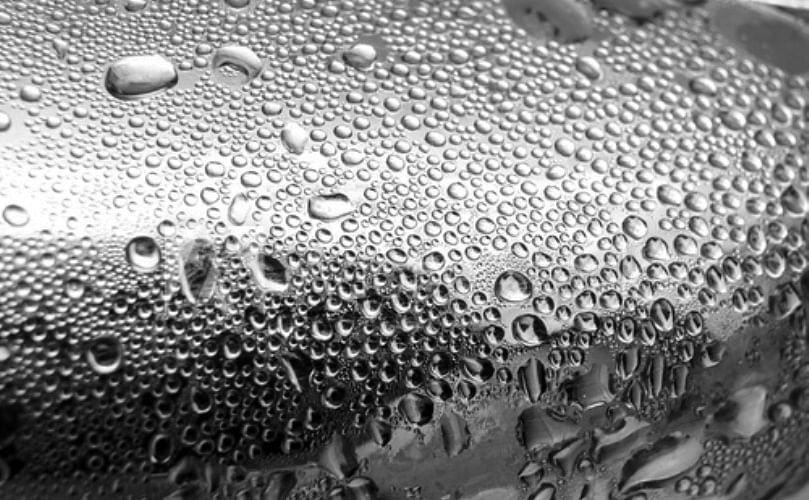
On a copper pipe coated with a hydrophobic material, but without the layer of oil, few droplets form, and they stay on the surface longer and grow much larger before falling away. (Courtesy: Nenad Miljkovic and Rong Xiao / MIT)
By promoting droplet formation, he says, it's possible to achieve a four- to eightfold improvement in heat transfer. Because the condensation is just one part of a complex cycle, that translates into an overall efficiency improvement of about 2 percent. That may not sound like much, but in these huge industrial processes even a fraction of a percent improvement is considered a major achievement with great potential impact.
Karim Khalil, graduate student:
“In this field, you're fighting for tenths of a percent.”Unlike the surface treatments Varanasi and his team have developed for other kinds of fluids, which rely on a liquid material held in place by a surface texture, in this case they were able to accomplish the fluid-repelling effect using a very thin solid coating—less than a micron thick (one millionth of a meter). That thinness is important, to ensure that the coating itself doesn't contribute to blocking heat transfer, Khalil explains.
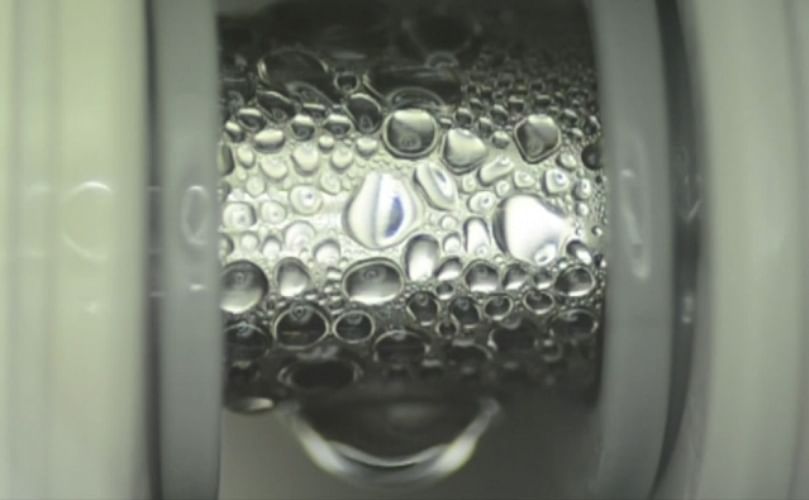
Specialized thin coatings developed by the MIT team cause even low-surface-tension fluids to readily form droplets on the surface of a pipe, as seen here, which improves the efficiency of heat transfer. (Courtesy: MIT News)
The authors optimized the iCVD process by tuning the grafting of coating molecules onto the surface, in order to minimize the pinning of condensing droplets and facilitate their easy shedding. The process could be carried out on location in industrial-scale equipment, and could be retrofitted into existing installations to provide a boost in efficiency.
The process is "materials agnostic," Khalil says, and can be applied on either flat surfaces or tubing made of stainless steel, copper, titanium, or other metals commonly used in evaporative heat-transfer processes that involve these low-surface-tension fluids.
Karim Khalil:
“Whatever material you come up with, it tends to be scalable with this process. The heat transfer improves by almost eight times."The net result is that on these surfaces, condensing fluids such as liquid methane will readily form small droplets that quickly fall off the surface, making room for more to form, and in the process shedding heat from the metal to the droplets that fall away. Without the coating, the fluid would spread out over the whole surface and resist falling away, forming a kind of heat-retaining blanket.
"These are inherently inefficient systems, but this could make them more efficient."
One area where such coatings could play a useful role, Varanasi says, is in organic Rankine cycle systems, which are widely used for generating power from waste heat in a variety of industrial processes.