FPS Keeps It Cool – and Efficient
Freezing potato products: selecting a control system
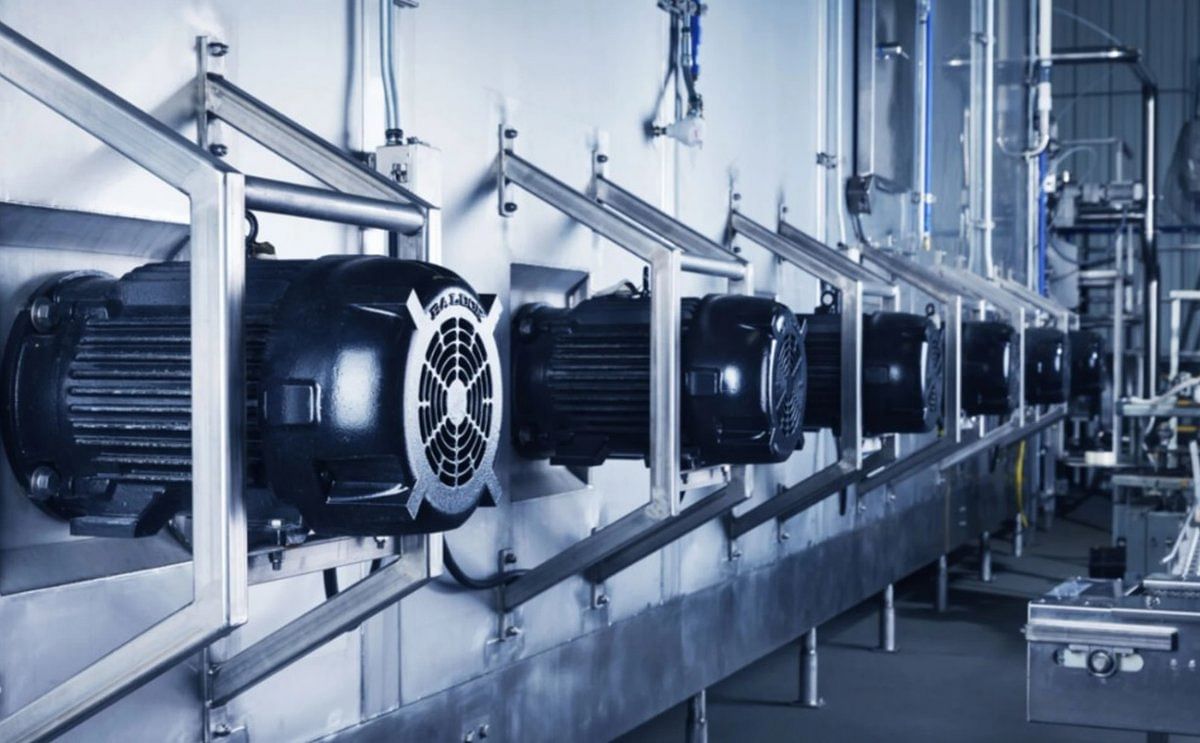
When consumers pay top dollar for food, they expect consistent quality. And whether the buyer is selecting items for a restaurant menu or the family table, frozen food is hard to beat when it comes to preserving nutrients and flavor.
But food is finicky.
Sean Cao, electrical engineering manager, FPS Food Process Solutions:
“Even a slight change in temperature or time during the freezing process can affect the quality, taste and texture of food.”
“Maintaining consistent temperature control – and maximizing throughput – is critical in industrial applications.”
A global leader in food cooling and freezing equipment, FPS Food Process Solutions provides innovative systems designed to meet stringent hygienic demands. Fueled by a strong reputation in the food industry, the privately owned company has experienced double-digit growth in recent years. FPS is headquartered in Richmond, a suburb of Vancouver, British Columbia, Canada.
Midstream Challenges – Times Two
Recently, an Idaho-based food and agribusiness company specializing in restaurant-quality frozen products approached FPS for a solution. Based on the success of its potato product line, the food company planned to expand production capacity at a new facility in Winnipeg.
The new plant was designed to run two processing lines – one for French fries and one for formed potato products, such as hash browns. FPS was contracted for the freezers on each line.
Sean Cao:
“The two products have vastly different processing requirements and require different freezer technologies.”
A tunnel freezer is appropriate for French fries, which are flash frozen. A spiral freezer is ideal for formed potato products, which must be cooled more slowly. In both cases, the freezing process takes place midstream – between cooking and packaging.
Sean Cao:
“Since our freezers are in the middle of the process, they impact both upstream and downstream applications.”
“So machine reliability and uptime are critical – and impact the productivity of the entire line. In fact, when a freezer goes down, often the entire line must stop.”
Custom Solutions Every Time
Like all FPS freezers, the solutions for the potato processing facility were custom designed to meet specific application requirements.
FPS built the tunnel freezer for a capacity of 56,000 pounds per hour and the spiral freezer for a capacity of 13,000 pounds per hour.
In the tunnel freezer, an Individual Quick Frozen (IQF) process drops the temperature of the freshly blanched French fries from 190°F to 0°F in about 20 minutes. The IQF process uses a system of refrigerator coils and fans to circulate cold air as the French fries advance through the tunnel on a conveyor.
Sean Cao:
“The spiral freezer is based on a similar refrigeration concept but uses a spiral conveyor to transport product – and retain the unique moisture and texture of the hash browns. The cycle time in the spiral freezer is approximately 45 minutes”
Maintainable Construction. Efficient Control.
To maximize cleanability and uptime, FPS minimizes the number of internal components by mounting them outside when possible. In addition, all electric motors can be externally located to improve durability – and reduce the number of internal components to clean.
A maintainable, hygienic design is just one part of the uptime equation. The other is consistent and precise airflow – and an easy-to-use control system. FPS built their new industrial freezers on PlantPAx® DCS, a modern distributed control system from Rockwell Automation.
Sean Cao:
“Our customer was standardizing on PlantPAx in their new facility. They asked us to use PlantPAx to streamline integration throughout their operations.”
Challenge
Ease design and integration of custom freezers for new potato processing plant.
Solution
Smart process control solution based on PlantPAx DCS and featuring:
- Allen-Bradley ControlLogix Controllers
- Allen-Bradley PowerFlex 753 and 525 AC Drives
- Allen-Bradley PanelView Graphic Terminals
Results
- Decreases engineering time and panel assembly by about 20%
- Speeds integration with the plant-wide system
- Achieves energy-efficient operation
- Eases troubleshooting and maintenance
The control platform for both freezers features an Allen-Bradley® ControlLogix® 5570 controller. Allen-Bradley PowerFlex® 753 and 525 AC drives control the fans and conveyors. The HMIs are based on Allen-Bradley PanelView™ graphic terminals and the systems are integrated on an EtherNet/IP™ network.
Various RTD sensors are integrated into the system to monitor freezer and product temperature. PID loops are used to adjust refrigeration valves and conveyor speeds to match requirements.
Fan control is central to the operation of both freezers – and key to efficiency.
Sean Cao:
“In the tunnel freezer, the PowerFlex drives control 22 fans. Precisely matching the fan speed to the process requirements of each recipe helps reduce energy consumption.”
A Smarter Path to System Design
While FPS was very familiar with Rockwell Automation control systems, this latest solution represents just the second time the company used PlantPAx DCS for system design.
Lessons learned in the first implementation – a large, site-wide project – easily scaled to the two smaller freezer systems.
Sean Cao:
“Regardless of project, the foundation for all system programming has already been developed in PlantPAx. In other words, the PLC and HMI coding is predefined – and the Add-On Instructions (AOIs) and global objects make configuration much easier.”
FPS estimates that the PlantPAx system helped reduce their design time by about 20%.
Sean Cao:
“With PlantPAx we streamlined our process – and met our customer’s requirements for a consistent system that eases integration, operation and maintenance.”
Highlighted Company
Products
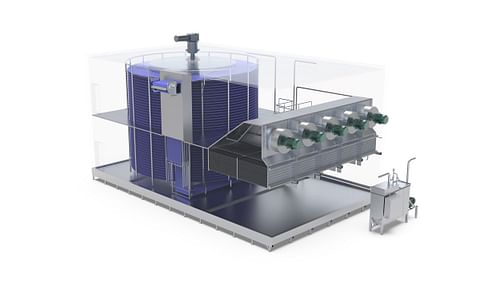