For the 2024 season, GRIMME is introducing the new generation of the well approved RH 20 / RH 24 / RH 28 receiving hoppers.
For the 2024 season, GRIMME is introducing the new generation of the well approved RH 20 / RH 24 / RH 28 receiving hoppers
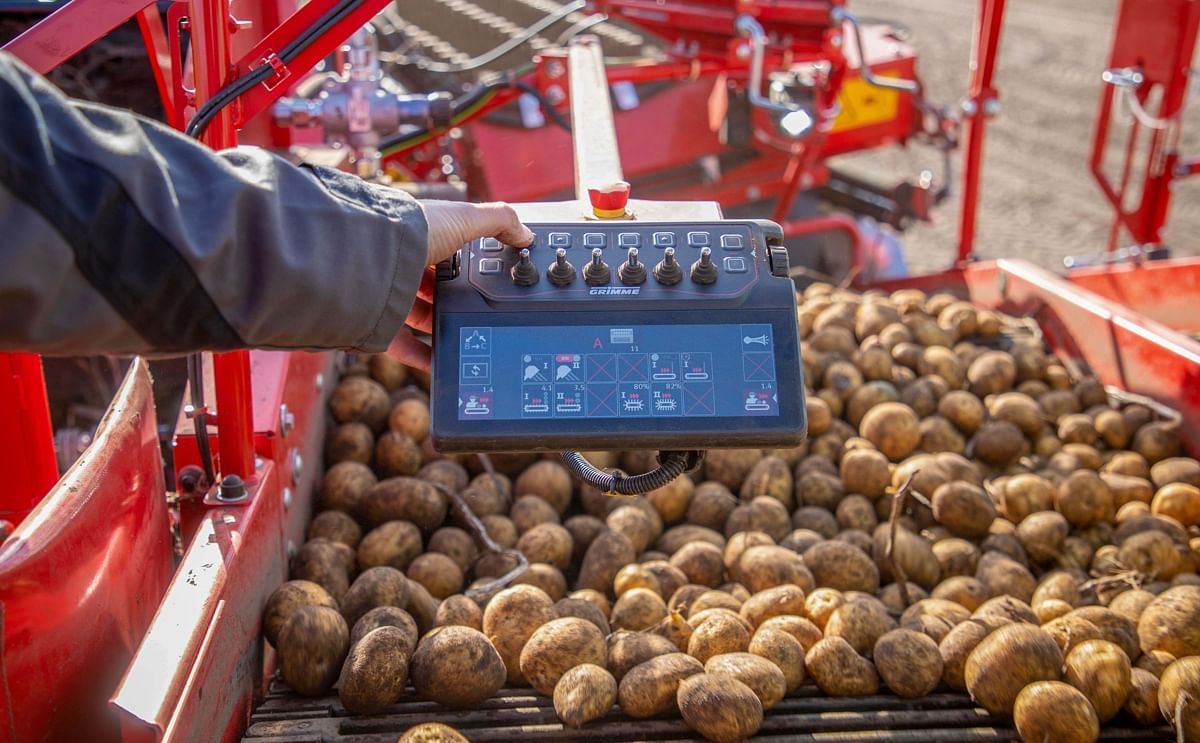
The new generation of the proven GRIMME RH 20, RH 24 and RH 28 receiving hoppers features numerous further developments in terms of throughput capacity, crop protection, convenience, and variety of equipment, which are visible through the new design of the machine.
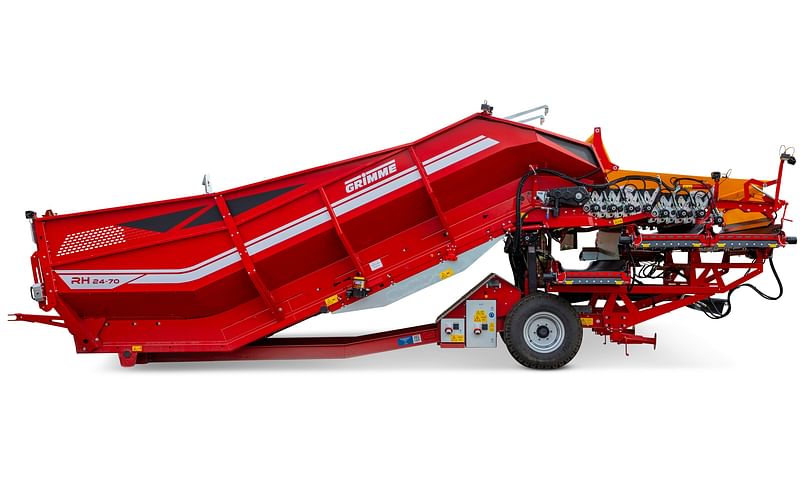
The modern design of the hopper offers visual windows in the front section, as well as freely accessible connections and operating elements.
Improved hopper floor
With the new receiving hoppers, the hopper floor speed can be set in a wide range from 0.2 to 6.0 m/min. The considerably deeper pockets of the hopper floor lead to an optimised conveying effect and enable the hopper to be emptied quickly and completely. The revised "Capacity Control" feature now enables the hopper floor speed to be controlled by specifying the throughput rate in tonnes per hour.
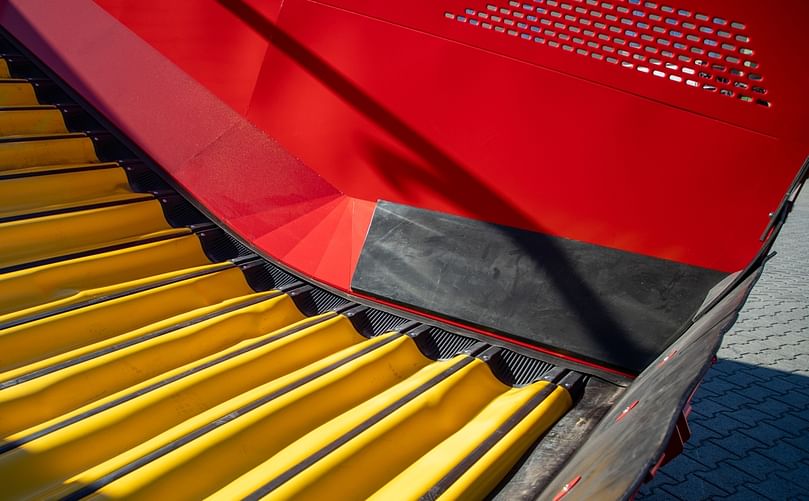
Cushioning in the front section and soft stuffing of the crossbars of the hopper floor ensure improved crop protection.
To increase the performance and improve the crop flow, the incline angle of the hopper belt was reduced. The 10 cm wider front section provides an increased intake volume and makes it easier to manoeuvre trailers to the hopper.
Approaching is also simplified by the new manoeuvring aid with "traffic light control". The new LED working lights allow working comfortably - even in the dark.
Comfortable operation
Operation of the hopper is simple and intuitive with the help of the new IBX 300 ISOBUS operator unit.
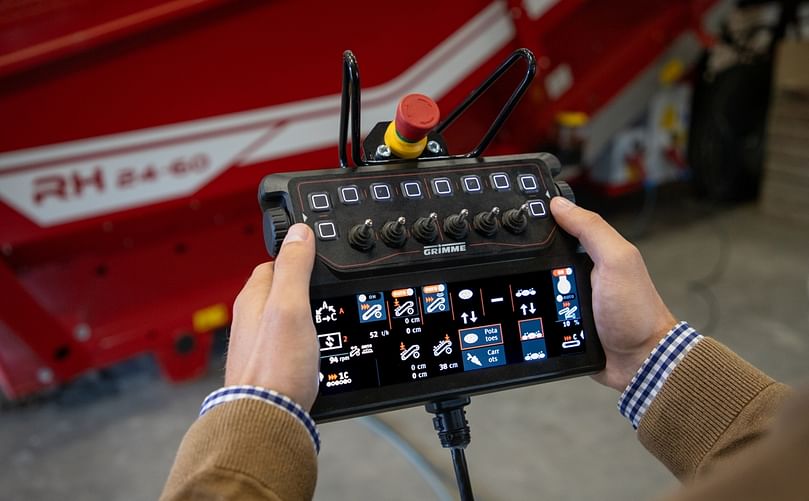
The operator unit IBX 300 can be equipped with a 15 metre cable and an emergency stop for convenient, mobile operation of the hopper.
Operation can be extended using the CCI 800 ISOBUS operator terminal. Various assistance systems take the strain off the user when operating the machine.
All relevant settings such as roller speed, roller spacing, and tilt angle are now visualised in an even more user-friendly way and can be easily reproduced.
The new feature called "Remain Control" function measures the remaining crop layer in the hopper. When refilling the hopper, the crop does not fall directly onto the hopper floor, but onto a defined, small amount of crop. This significantly improves crop protection.
Optimised Soil cleaning and pre-grading
Thanks to the revised design of the roller spacing adjustment, the soil cleaning and pre-grading rollers can be adapted even better to the respective operating conditions.
The "VarioClean" function enables high cleaning performance, especially in heavy and sticky harvesting/handling conditions. An additional transition step has been installed within the roller package for the soil removal, which also loosens up the crop flow.
In addition, the rollers in front of and behind the step can be aligned slightly upwards, which extends the dwell time of the crop on the rollers and thus increases the cleaning time.
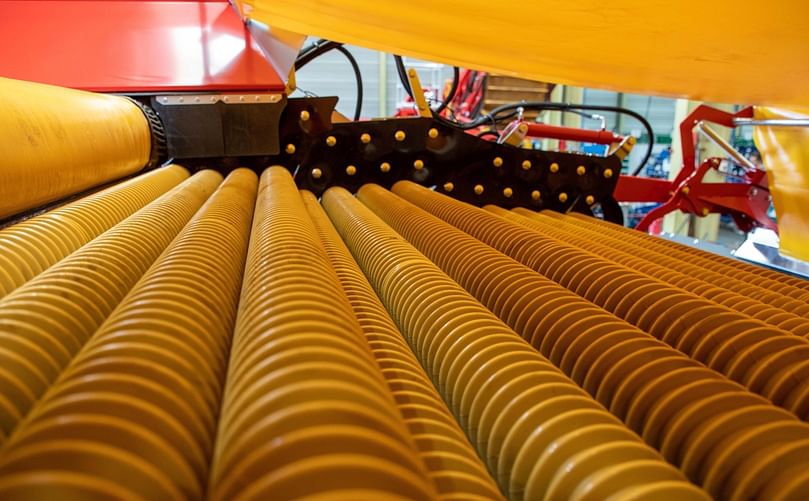
VarioClean - The soil cleaning rollers can be be adjusted upwards in particularly heavy conditions and downwards in sandy/light conditions.
Another new feature is that the PU spiral rollers can rotate against the crop flow in the "Turbo-Clean" function. The majority of the cleaned soil is guided towards the soil cross conveyors and the bunker floor, but not onto the crop cross conveyor. This reliably prevents any accumulations of soil in the potato store.
New variety of features and options
The RH 28 scores with a high throughput rate thanks to the 2.80 m wide soil cleaning rollers.
The new RH 24 XT version is also available as an efficient alternative for storing potatoes. In this model, there is a large sorting table behind the cleaning rollers, which can optionally be combined with an opto-electronic sorting unit.
Another new machine is the receiving hopper, type RH 24-60 S, which rises in a straight line. The machine can be equipped with an onion distributor, an additional presentation belt (i.e. a transfer belt between the hopper floor and roller installation) and plain rollers, which are made of steel. It is particularly suitable for sensitive crop such as onions and carrots.
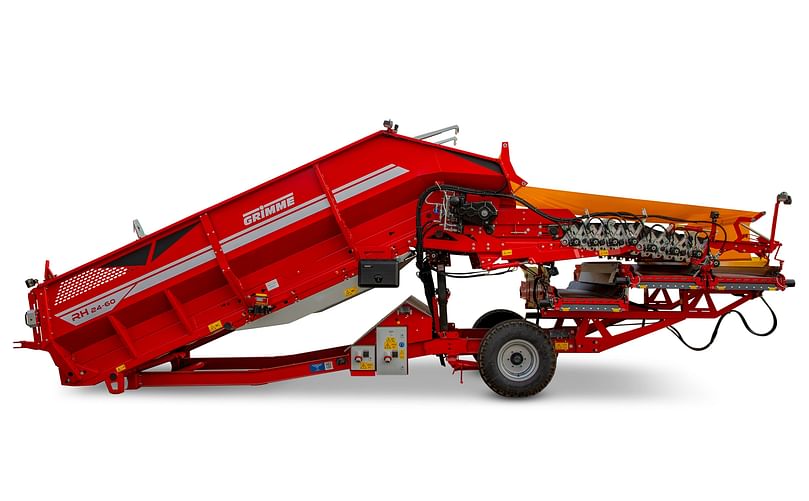
The straight hopper design of the S version is particularly suitable for field vegetables (e.g. carrots)