Secondary Packaging Automation: Is it Time?
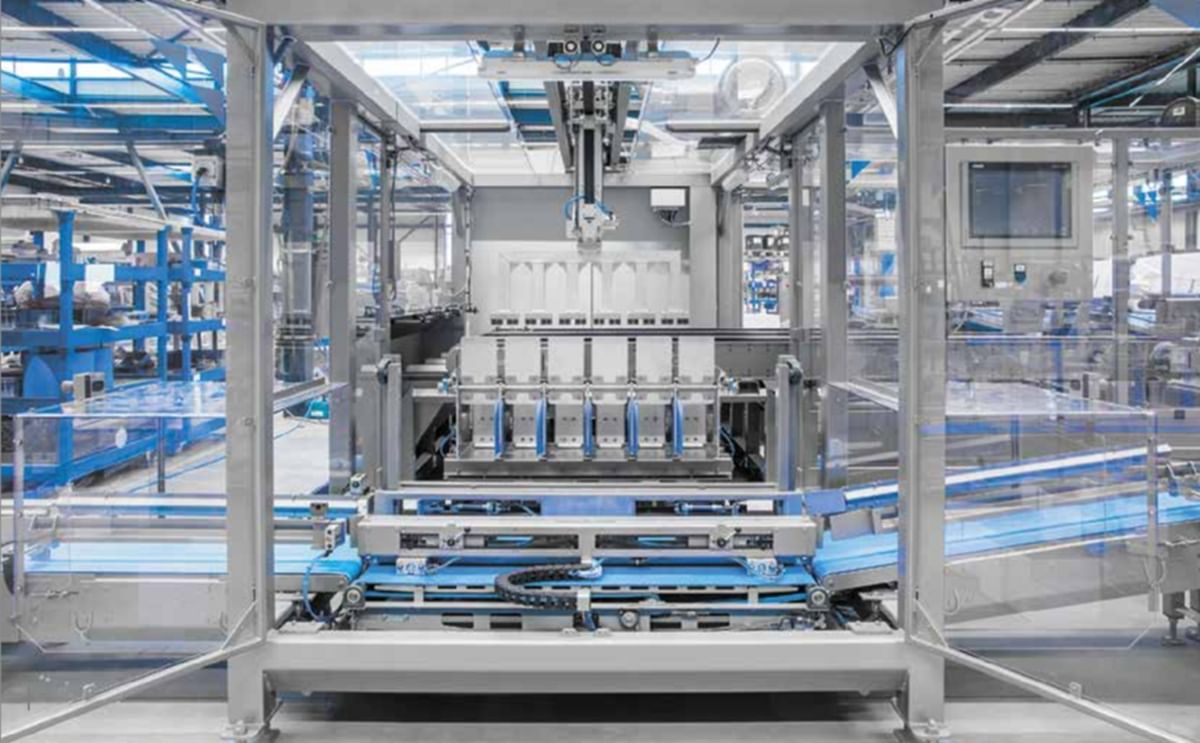
BluePrint Automation Gantry 300 swing
Secondary packaging refers to the process of packaging and labeling final products for display, shipping, or storage purposes. In most cases, it involves packaging products that have already been packaged, such as bottles, boxes, and bags. Examples of secondary packaging include cases, cartons, trays and totes.
Automated secondary packaging can help firms boost their productivity, reduce costs, enhance efficiency, and increase accuracy. As such, it is crucial for firms to know when it is time to automate their secondary packaging lines.
This article discusses some of the key signs that indicate that a firm needs to automate its secondary packaging line.
High Labor and Material Costs
One of the signs that a firm needs to automate its secondary packaging line is when it has high labor and material costs. Manual secondary packaging can be expensive in terms of labor and material costs, especially when dealing with large quantities of products.
Automation eliminates the need for manual labor, allowing companies to save on staffing costs such as recruitment, training, and wages. Moreover, choosing to automate your secondary packaging line(s) reduces manual handling of products, reducing material loss during handling and decreasing labor requirements.
Additionally, automated packaging machinery can ensure uniformity and consistency in packaging size, shape, and weight, enabling companies to reduce material usage, maintain product quality, and reduce the need for manual labor.
Automating the secondary packaging line can help reduce labor and material costs by eliminating errors, enhancing efficiency, and increasing productivity.
Inconsistency in Product Quality
Product quality is critical in ensuring customer satisfaction and repeat business. Inconsistent product quality can lead to customer complaints, returns, and reduced revenues. Failure to address the issue of inconsistent product quality can harm a firm's reputation and competitive advantage.
In this sense, secondary packaging serves a practical purpose. It organizes or stabilizes products to get them shelf ready. It also makes for easier and safer storage, so when it comes time for a manufacturer to ship off more units, you can trust they make it to consumers intact.
Automating the secondary packaging line can help improve product quality by eliminating errors, ensuring accurate labeling, and enhancing consistency.
Increased Production Demands
Increased production demands is another sign that a firm needs to automate its secondary packaging line. Automated packaging equipment is faster and more accurate than manual processes, which leads to increased production output.
The use of manual labor can be time-consuming and limit the rate of production, leading to delays in the delivery of products to the market. With automation, products can be packaged at a faster rate, giving industries the opportunity to produce more goods in less time and increase their overall output.
Need for Increased Line Flexibility
Firms that need to package products of varying sizes, shapes, and weights may find manual secondary packaging challenging. Manual packaging may require different tools, materials, and packaging procedures for each product, leading to increased costs and reduced efficiency.
Automation can help increase line flexibility by accommodating a wide variety of products and packaging materials. For example, the Gantry 300 Swing case packer is a simple top and side load solution picking and loading product either standing up or laying down on the same machine.
The "Swing" can easily case pack into RSC or retail-ready cases, trays and other containers. With a quick changeover between recipes, the Gantry 300 Swing can run pouches, bags, cartons and more with no impact on productivity. A system such as this can help firms reduce operational costs, increase efficiency, and enhance customer satisfaction.
Increased Safety and Regulatory Compliance Requirements
Manual packaging may not meet the safety and regulatory compliance requirements of some products, especially those that require sterile packaging. Manual packaging can be prone to errors such as mislabeling, inconsistent packaging, and contamination.
The Dairy 3A Compliant Spider 100v is one solution to consider when sanitation requirements are your priority. Built to Dairy 3A specifications, design considerations include full stainless steel, open channel, sanitary wash down construction; including frame design, pick tools, robot mounting, etc.
This dairy 3A compliant system is also used for USDA environments where robots are picking meat or meat filled products.
Automating the secondary packaging line can help meet safety and regulatory compliance requirements by ensuring accurate labeling, consistent packaging, and sterile packaging.
Increased Need for Data Collection and Analysis
Secondary packaging automation can provide a wealth of data and analytics that can help manufacturers optimize their production processes, improve quality control, and increase efficiency.
By automating the process of packaging products in boxes, bags, or other containers, manufacturers can collect real-time data that can be used to make informed decisions about everything from packaging materials to shipping routes.
One of the main types of data that can be gleaned from secondary packaging automation is related to product quality. By tracking the weight, dimensions, and other characteristics of each package as it is produced, manufacturers can identify potential quality issues before they become a problem.
For example, if packages are consistently coming in underweight, that may indicate an issue with the packaging machine that needs to be addressed. By catching these issues early, manufacturers can avoid costly recalls and protect their reputation with customers.
Another important type of data that can be obtained from secondary packaging automation is related to production efficiency. By tracking production times, downtime, and other key metrics, manufacturers can identify bottlenecks in their packaging process and make adjustments to improve output.
For example, if a particular packaging machine is frequently breaking down or causing delays, it may be time to invest in an upgrade or additional training for employees.
The lifespan of secondary packaging equipment can vary greatly depending on factors such as the type of equipment, its frequency of use, maintenance and care, and technological advancements in the industry.
Generally, well-maintained and properly operated equipment can last for 10 years or more, while equipment that is poorly maintained or frequently used may need to be replaced in as little as 3-5 years.
Regular maintenance and repairs can help extend the lifespan of secondary packaging equipment and ensure it continues to operate efficiently and effectively. To keep your secondary packaging equipment running at optimal efficiency BluePrint Automation offers an Asset Health and Reliability Program (AHRP) customizable to new and existing equipment.
This program allows customers to increase asset health, optimize pe Customers who take advantage of the program can expect to receive the following:
The goal of this program is to build an ongoing relationship with the customer and extend the life cycle of the customers’ equipment. Benefits of the AHRP include:
In conclusion, automating the secondary packaging line can help firms reduce labor and material costs, increase productivity, enhance efficiency, and improve product quality. Firms need to be aware of the signs that indicate the need for automation, such as high labor and material costs, inconsistent product quality, increased production demands, and increased safety and regulatory compliance requirements.
Automation can help firms meet the demands of a fast-paced and competitive business environment by providing increased line flexibility, data collection, and analysis capabilities. Opting for automation can provide firms with a competitive advantage, increased operational efficiency, and enhanced customer satisfaction.
Automated secondary packaging can help firms boost their productivity, reduce costs, enhance efficiency, and increase accuracy. As such, it is crucial for firms to know when it is time to automate their secondary packaging lines.
This article discusses some of the key signs that indicate that a firm needs to automate its secondary packaging line.
High Labor and Material Costs
One of the signs that a firm needs to automate its secondary packaging line is when it has high labor and material costs. Manual secondary packaging can be expensive in terms of labor and material costs, especially when dealing with large quantities of products.
Automation eliminates the need for manual labor, allowing companies to save on staffing costs such as recruitment, training, and wages. Moreover, choosing to automate your secondary packaging line(s) reduces manual handling of products, reducing material loss during handling and decreasing labor requirements.
Additionally, automated packaging machinery can ensure uniformity and consistency in packaging size, shape, and weight, enabling companies to reduce material usage, maintain product quality, and reduce the need for manual labor.
Automating the secondary packaging line can help reduce labor and material costs by eliminating errors, enhancing efficiency, and increasing productivity.
Inconsistency in Product Quality
Product quality is critical in ensuring customer satisfaction and repeat business. Inconsistent product quality can lead to customer complaints, returns, and reduced revenues. Failure to address the issue of inconsistent product quality can harm a firm's reputation and competitive advantage.
In this sense, secondary packaging serves a practical purpose. It organizes or stabilizes products to get them shelf ready. It also makes for easier and safer storage, so when it comes time for a manufacturer to ship off more units, you can trust they make it to consumers intact.
Automating the secondary packaging line can help improve product quality by eliminating errors, ensuring accurate labeling, and enhancing consistency.
Increased Production Demands
Increased production demands is another sign that a firm needs to automate its secondary packaging line. Automated packaging equipment is faster and more accurate than manual processes, which leads to increased production output.
The use of manual labor can be time-consuming and limit the rate of production, leading to delays in the delivery of products to the market. With automation, products can be packaged at a faster rate, giving industries the opportunity to produce more goods in less time and increase their overall output.
Need for Increased Line Flexibility
Firms that need to package products of varying sizes, shapes, and weights may find manual secondary packaging challenging. Manual packaging may require different tools, materials, and packaging procedures for each product, leading to increased costs and reduced efficiency.
Automation can help increase line flexibility by accommodating a wide variety of products and packaging materials. For example, the Gantry 300 Swing case packer is a simple top and side load solution picking and loading product either standing up or laying down on the same machine.
The "Swing" can easily case pack into RSC or retail-ready cases, trays and other containers. With a quick changeover between recipes, the Gantry 300 Swing can run pouches, bags, cartons and more with no impact on productivity. A system such as this can help firms reduce operational costs, increase efficiency, and enhance customer satisfaction.
Increased Safety and Regulatory Compliance Requirements
Manual packaging may not meet the safety and regulatory compliance requirements of some products, especially those that require sterile packaging. Manual packaging can be prone to errors such as mislabeling, inconsistent packaging, and contamination.
The Dairy 3A Compliant Spider 100v is one solution to consider when sanitation requirements are your priority. Built to Dairy 3A specifications, design considerations include full stainless steel, open channel, sanitary wash down construction; including frame design, pick tools, robot mounting, etc.
This dairy 3A compliant system is also used for USDA environments where robots are picking meat or meat filled products.
Automating the secondary packaging line can help meet safety and regulatory compliance requirements by ensuring accurate labeling, consistent packaging, and sterile packaging.
Increased Need for Data Collection and Analysis
Secondary packaging automation can provide a wealth of data and analytics that can help manufacturers optimize their production processes, improve quality control, and increase efficiency.
By automating the process of packaging products in boxes, bags, or other containers, manufacturers can collect real-time data that can be used to make informed decisions about everything from packaging materials to shipping routes.
One of the main types of data that can be gleaned from secondary packaging automation is related to product quality. By tracking the weight, dimensions, and other characteristics of each package as it is produced, manufacturers can identify potential quality issues before they become a problem.
For example, if packages are consistently coming in underweight, that may indicate an issue with the packaging machine that needs to be addressed. By catching these issues early, manufacturers can avoid costly recalls and protect their reputation with customers.
Another important type of data that can be obtained from secondary packaging automation is related to production efficiency. By tracking production times, downtime, and other key metrics, manufacturers can identify bottlenecks in their packaging process and make adjustments to improve output.
For example, if a particular packaging machine is frequently breaking down or causing delays, it may be time to invest in an upgrade or additional training for employees.
The lifespan of secondary packaging equipment can vary greatly depending on factors such as the type of equipment, its frequency of use, maintenance and care, and technological advancements in the industry.
Generally, well-maintained and properly operated equipment can last for 10 years or more, while equipment that is poorly maintained or frequently used may need to be replaced in as little as 3-5 years.
Regular maintenance and repairs can help extend the lifespan of secondary packaging equipment and ensure it continues to operate efficiently and effectively. To keep your secondary packaging equipment running at optimal efficiency BluePrint Automation offers an Asset Health and Reliability Program (AHRP) customizable to new and existing equipment.
This program allows customers to increase asset health, optimize pe Customers who take advantage of the program can expect to receive the following:
- Health assessment workbook
- Full assessment of every assembly/part in the machine/line (blueprint sold equipment)
- Thermography
- Assessment of the operator and maintenance personnel skillset
- Assessment of machine tuning, rate and overall operation
- Assessment of current PM program
- Updated spare-parts list with pricing good for 60 days
- Quote for immediate replacement parts and available upgrade
- Closeout meeting to explain workbook, quotes and PM recommendations.
The goal of this program is to build an ongoing relationship with the customer and extend the life cycle of the customers’ equipment. Benefits of the AHRP include:
- Optimized system performance
- Increased machine life
- Further knowledge on care and maintenance of your system
In conclusion, automating the secondary packaging line can help firms reduce labor and material costs, increase productivity, enhance efficiency, and improve product quality. Firms need to be aware of the signs that indicate the need for automation, such as high labor and material costs, inconsistent product quality, increased production demands, and increased safety and regulatory compliance requirements.
Automation can help firms meet the demands of a fast-paced and competitive business environment by providing increased line flexibility, data collection, and analysis capabilities. Opting for automation can provide firms with a competitive advantage, increased operational efficiency, and enhanced customer satisfaction.
¿Te gustaría recibir noticias como esta por correo electrónico? ¡Únete y suscríbete!
Únete a nuestra Telegrama ¡Canal para actualizaciones periódicas!
Empresa Destacada
Contenido Patrocinado
Contenido Patrocinado
Contenido Patrocinado
Contenido Patrocinado
Contenido Patrocinado