Gpi delivers additive line for the new Lamb Weston/Meijers factory in Kruiningen
Gpi delivers additive line for the new Lamb Weston Meijer potato flake factory in Kruiningen
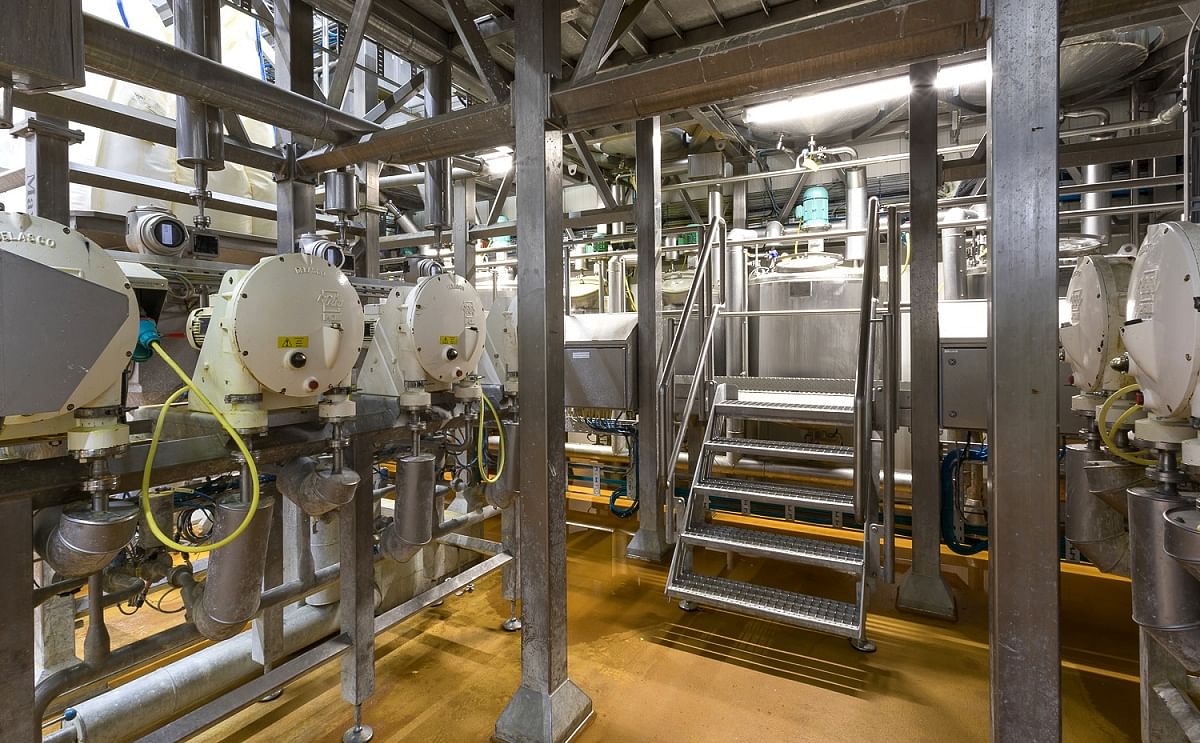
Lamb Weston see more than just a potato: they see opportunities. Opportunities to feed a growing world population and opportunities to create new products and production methods for their clients. This philosophy was explained to them by Lamb Weston/Meijer (LWM) when they met them for the first time.
Lamb Weston/Meijer is one of the world’s biggest potato processors and is known for their deep-frozen coated and uncoated fries as well as other potato products such as potato flakes and specially shaped products like Twisters and Crisscuts.
The construction of a new flake factory to expand the existing production site in Kruiningen will increase its annual production capacity by 180,000 tonnes. As a result, LWM will be able to satisfy the increasing demand for dried potato flakes. Gpi De Gouwe was called in to deliver the additive preparation system for the new site.
Leo Smits, Sales Design Manager at Gpi De Gouwe:
The provision of additives such as emulsifiers are vital to maintain consistent quality of the end product. Thanks to Gpi’s new system, additives can be easily and accurately added to the potato starch in precise dosages in order to produce potato flakes in the new factory.
The additive preparation system (additive line) for the new factory consists of Big Bag unloading stations, vacuum transport systems, dosage and mixing tanks, tipping trays, piping and many other components, all of which are made of 100% stainless steel. The decision to work with Gpi was simple.
Richard van de Sande, Project Manager at Lamb Weston/Meijer:
Sustainability is a key priority at Lamb Weston/Meijer. In everything they do, from harvesting to smart processing methods, their goal is to work as efficiently as possible and minimise harm to the environment. The new factory will enable Lamb Weston Meijer to reduce its emissions.
Marc Schroeder, CEO of Lamb Weston/Meijer:
Lamb Weston/Meijer is one of the world’s biggest potato processors and is known for their deep-frozen coated and uncoated fries as well as other potato products such as potato flakes and specially shaped products like Twisters and Crisscuts.
The construction of a new flake factory to expand the existing production site in Kruiningen will increase its annual production capacity by 180,000 tonnes. As a result, LWM will be able to satisfy the increasing demand for dried potato flakes. Gpi De Gouwe was called in to deliver the additive preparation system for the new site.
Leo Smits, Sales Design Manager at Gpi De Gouwe:
"It took some time to create the definitive design, but we ultimately produced an additive line that perfectly matches the client’s needs and wishes."The system introduces additives to the potato flakes in an easy and user-friendly manner to ensure consistent quality of potato products throughout the entire year. Potatoes are a natural product and their quality depends on conditions during both the cultivation period and the harvest season.
The provision of additives such as emulsifiers are vital to maintain consistent quality of the end product. Thanks to Gpi’s new system, additives can be easily and accurately added to the potato starch in precise dosages in order to produce potato flakes in the new factory.
The additive preparation system (additive line) for the new factory consists of Big Bag unloading stations, vacuum transport systems, dosage and mixing tanks, tipping trays, piping and many other components, all of which are made of 100% stainless steel. The decision to work with Gpi was simple.
Richard van de Sande, Project Manager at Lamb Weston/Meijer:
"Gpi is a great sparring partner during the design process and they very quickly quoted us an extremely reasonable price accompanied by a clear schedule. Gpi De Gouwe is also a very open, honest and well-organised business."Alexander Kraaijkamp, Managing Director at Gpi De Gouwe:
"We can look back proudly on an extremely pleasant collaboration with results that both companies can be proud of."A factory with one eye on the future
Sustainability is a key priority at Lamb Weston/Meijer. In everything they do, from harvesting to smart processing methods, their goal is to work as efficiently as possible and minimise harm to the environment. The new factory will enable Lamb Weston Meijer to reduce its emissions.
Marc Schroeder, CEO of Lamb Weston/Meijer:
"This is crucial to our sustainability strategy. This investment will boost the global position of Lamb Weston/Meijer. and enable us to achieve our growth ambitions, deliver new product innovation and improve our customer service."
¿Te gustaría recibir noticias como esta por correo electrónico? ¡Únete y suscríbete!
Únete a nuestra Telegrama ¡Canal para actualizaciones periódicas!
Empresa Destacada
Contenido Patrocinado
Contenido Patrocinado
Contenido Patrocinado
Contenido Patrocinado
Contenido Patrocinado