Tyrrells Crisps set to reduce carbon emissions by over 14% with switch to LNG
Tyrrells Crisps set to reduce carbon emissions by over 14% with switch to LNG
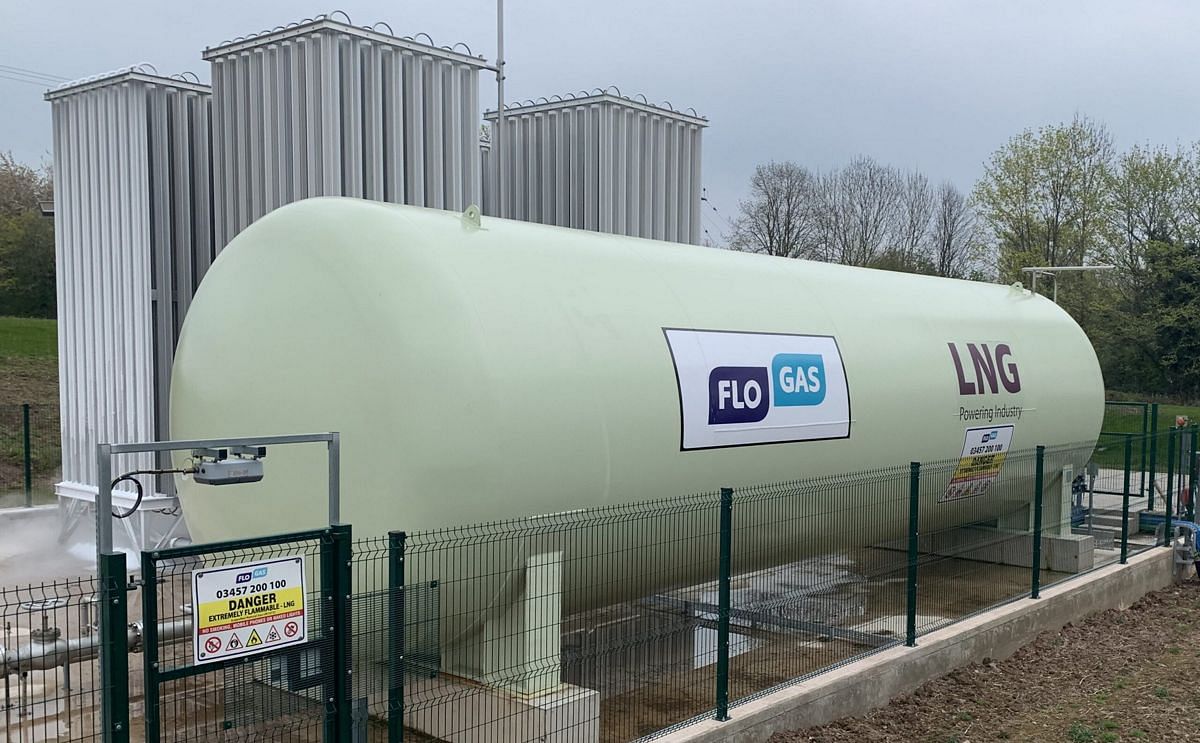
One of the UK’s largest potato crisp manufacturers, Tyrrells, has taken its latest step in a continued sustainability drive by converting its energy supply to liquefied natural gas (LNG) which will reduce its carbon emissions by over 14% per year.
Based at their potato crisp factory in Herefordshire and part of the KP Snacks family, Tyrrells produces over 86 million bags of crisps every year. With high energy demands to consider, the company wanted to find a way of increasing efficiencies in order to lower its carbon footprint.
Additionally, a solution was needed to reduce the number of weekly fuel deliveries in order to improve site safety, which was proving challenging with onsite vehicle movements. As proven experts in delivering innovative solutions for high energy users, Flogas were approached by Tyrrells to help resolve their energy and site challenges and deliver a turnkey energy solution.
Eileen Wilkes, Head of Manufacturing from Tyrrells:
Mark Rutherford, from Flogas:
Based at their potato crisp factory in Herefordshire and part of the KP Snacks family, Tyrrells produces over 86 million bags of crisps every year. With high energy demands to consider, the company wanted to find a way of increasing efficiencies in order to lower its carbon footprint.
Additionally, a solution was needed to reduce the number of weekly fuel deliveries in order to improve site safety, which was proving challenging with onsite vehicle movements. As proven experts in delivering innovative solutions for high energy users, Flogas were approached by Tyrrells to help resolve their energy and site challenges and deliver a turnkey energy solution.
Eileen Wilkes, Head of Manufacturing from Tyrrells:
"As a company, we’re constantly evaluating the way we work to introduce new sustainability measures. By working with Flogas and switching to LNG, we will be reducing our carbon emissions by over 14% and cutting our production costs in the process, thanks to the cleaner burning nature of natural gas."By choosing Flogas LNG, Tyrrells can also benefit from working with a supplier that’s committed to offsetting all its level 1 and level 2 CO2 emissions. Outlined in its 2040 Vision, Flogas launched a long-term strategy to reduce its own environmental impact year-on-year and supply customers with 100% renewable energy by 2040. LNG will also help Tyrrells to meet on-going government energy legislation, which encourages businesses to use lower carbon, cleaner burning off-grid fuels.
"From a site safety perspective, one of the main issues we faced with the previous layout of the site was that we were limited in terms of our storage space. This meant that as our business grew, several deliveries of fuel were needed each week to meet energy demands, which in turn presented potential risks with additional vehicle movements around a busy factory."
"Working alongside Flogas, enabled us to identify an area on site, then design, plan and construct a purpose-built gasification plant. Working with their planning partners and the site team, Flogas took care of all of the specific planning requirements, so we didn’t need to worry about them."
"As the LNG is now self-contained and located to the side of the main factory, delivery trucks will no longer need to interact with site movements, which will minimise the risk to staff. This solution will also allow us to reduce site deliveries by 40%, resulting in less transport emissions and less disruption to local residents."
Mark Rutherford, from Flogas:
"From the initial planning stages in 2019 through to the sites final completion we’ve been able to embed ourselves entirely within the Tyrrells business. This has allowed the project team to gain a deep understanding of the site energy needs and deliver a solution that’s improved the business across the board."Eileen Wilkes:
"This project is a great example of how LNG can be of huge benefit to a large-scale energy users, whilst improving the safety of workers on site."
"The switchover to LNG has been seamless. Factory downtime was kept to a minimum as the switchover was made in incremental stages, with new tanks being installed on site whilst existing tanks were still in operation. Flogas have been there to guide us each step of the way and we’ve been kept well informed throughout the entire process. We look forward to creating the same top-quality crisps we’ve become known for but with less of an impact on the environment."
¿Te gustaría recibir noticias como esta por correo electrónico? ¡Únete y suscríbete!
Únete a nuestra Telegrama ¡Canal para actualizaciones periódicas!
Empresa Destacada
Contenido Patrocinado
Contenido Patrocinado
Contenido Patrocinado
Contenido Patrocinado
Contenido Patrocinado