Intralox ThermoDrive belting Reduces Cleaning Labor and Cleaning Time for Snack Producer Calbee
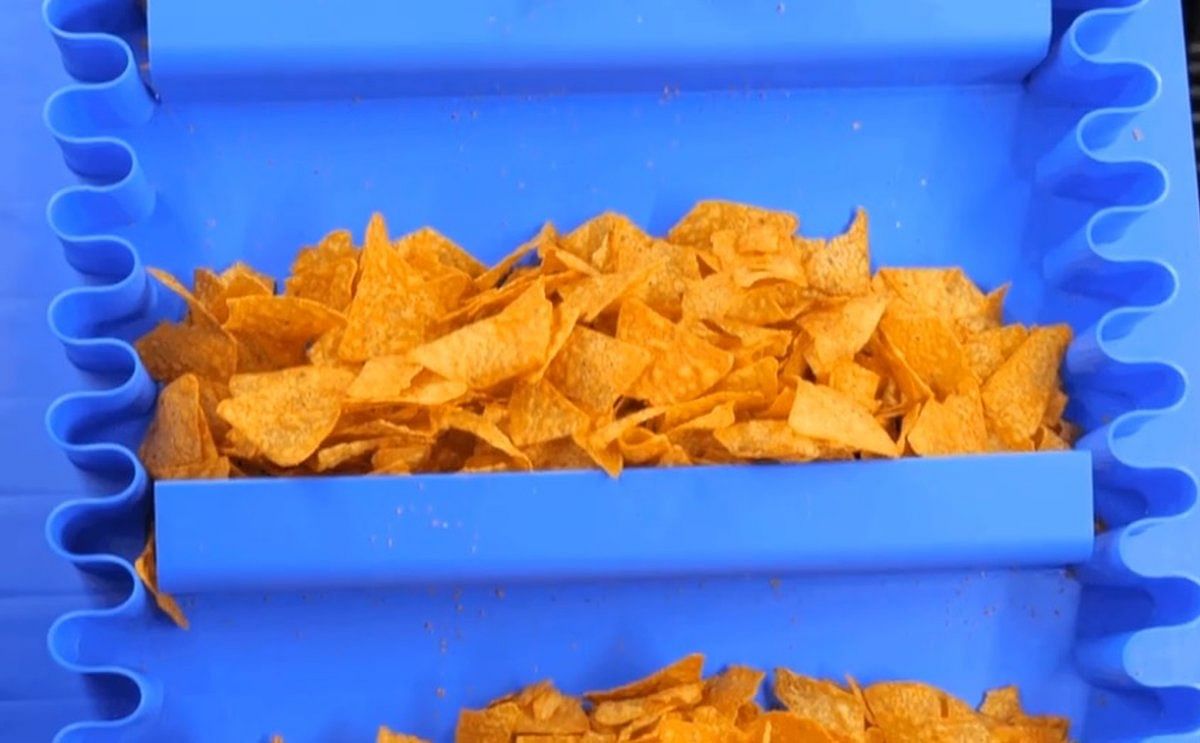
This case study by Intralox at US subsidiary of snack manufacturer Calbee shows how a proper choice of belt type can reduce both cleaning labor and cleaning time.
Calbee is a Japanese manufacturer of alternative snacks. Its plant in Senatobia, Mississippi, produces dried snacks made from extruded peas, black beans, and lentils for its Harvest Snaps brand.
The challenge that Calbee faced was that the snacks produced dust particles that migrated into the hinges, cracks, and crevices of the incline conveyor belt at the exit of one of its three dryers. This resulted in time-consuming cleaning and sanitation periods and significant unscheduled downtime.
Pre-rinsing took about 40 minutes and required three or four people to lift the belt, clean the frame, and remove debris. Cleaning often had to be repeated several times due to the belt's failure to pass ATP swab tests, which was critical to ensure food safety and quality.
The belt was at the end of its life cycle and required regular inspections and repairs that resulted in up to two hours of additional downtime every week. Clearly it was time for a replacement.
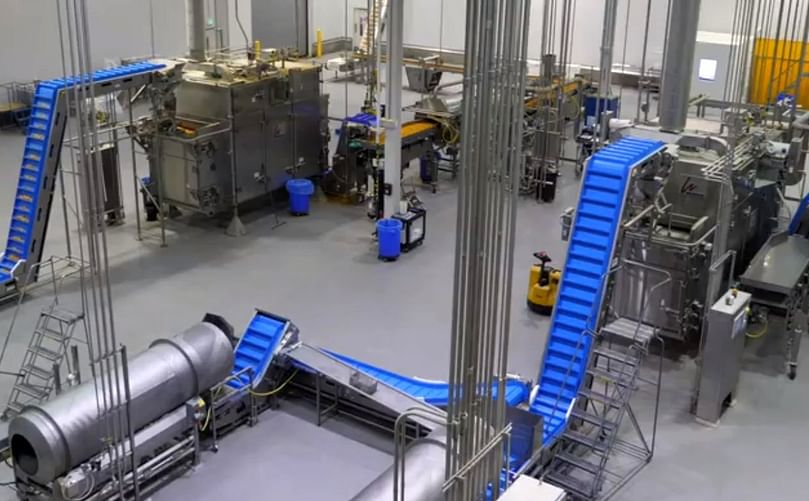
Intralox's new ThermoDrive® belts in polyurethane A23 material can help you significantly extend belt life along snack incline-to-packaging conveyors.
ThermoDrive belting's fully closed, homogeneous flat surface is easier to clean, and its lightweight design makes cleaning in place easier and less labor intensive. A23 material has a high temperature rating of 212°F (100°C), making it a good match for fresh-from-the-dryer product.
During the first month after the retrofit, Calbee saw tremendous results. Now it only takes one person to easily lift the belt and clean the frame, reducing cleaning labor by 75% and cleaning time by 50%. Moreover, the sanitation team achieved a 100% passing score on ATP swabs without additional cleaning cycles.
Cory Kennedy:
“Once we switched to the ThermoDrive belt, cleaning was made much simpler because there were no cracks and crevices. That engineering solution solved our problem.”Continuing the successful partnership, Calbee and Intralox are currently working on a project to replace other modular belts at the Senatobia plant over the next two years.