Ray Andrews of Crop Systems with the firm's new web-based potato store controller called SmartStor.
(Courtesy: Mark Bullimore / Eastern Daily Press)
UK potato store operators ill-informed on energy use
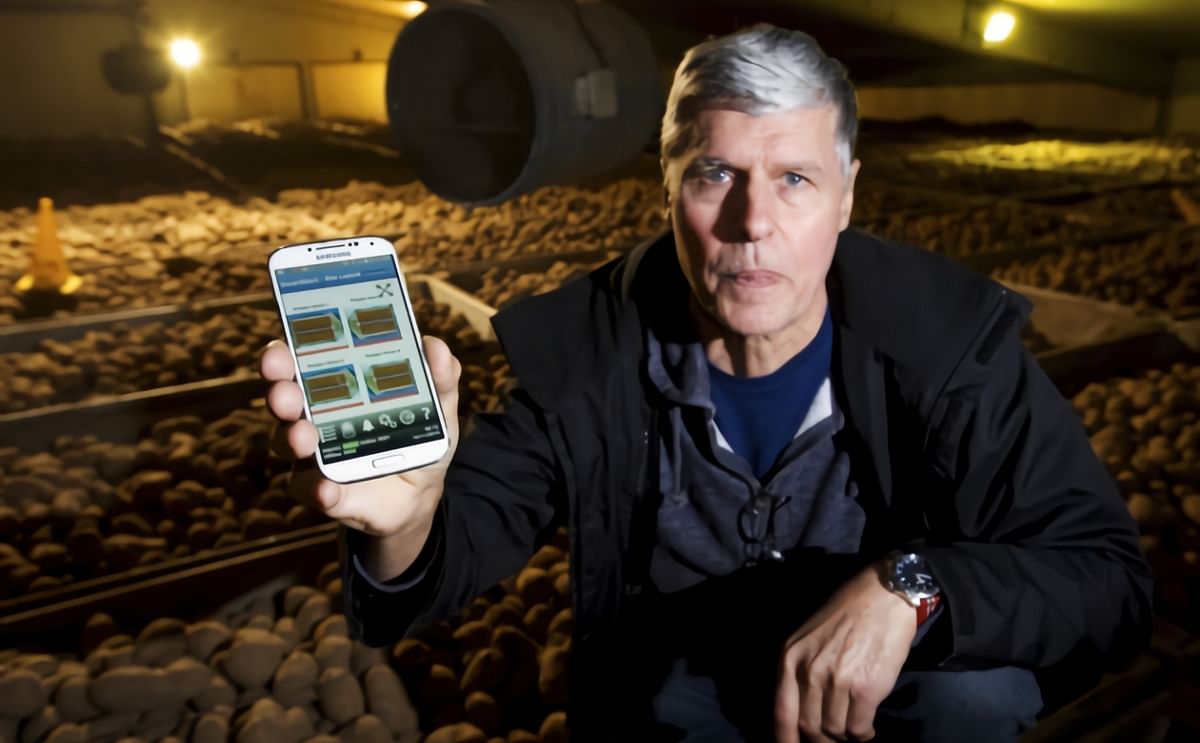
Many potato store operators could make significant savings in energy costs if they obtained more usage data to make informed decisions, according to Ray Andrews of Crop Systems Limited.
Many farmers assume their local farmer co-operative will provide the best price, but Ray said he’d worked with farmers paying 13.5% less by dealing direct with the energy company.
Ray recommended using a control system, such as Crop Systems’ SmartStor, and said it is important to also make sure parts of the store equipment that consume energy are working efficiently.
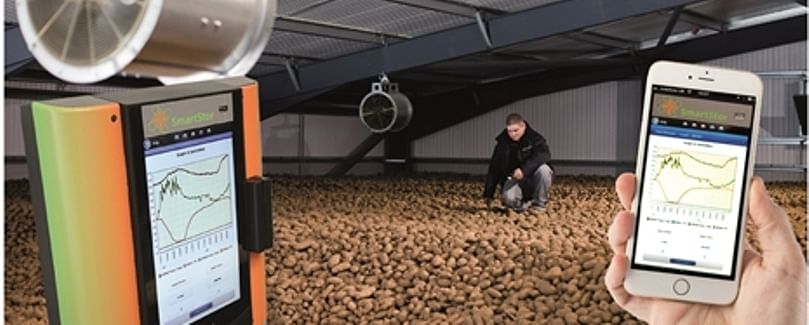
Crop Systems Ltd is launching SmartStor™ - their newest innovation, a cost effective crop store control system that that enables users to monitor and manage their stores via their smartphone or tablet anywhere, anytime.
Ray Andrews Managing Director at Crop Systems Ltd:
“I don’t think many operators realise how much energy prices vary, or how frequently in any 24-hour period they change. Bear in mind that peak energy prices are often three times higher than off-peak rates.”
“And these things are not fixed. I am sure many people don’t know how frequently suppliers change their pricing structures and timings."
“Our advice would be to look beyond the headline ‘unit cost’ and work out the cost, including things like the capacity charge, renewal obligation, feed-in-tariff, reactive power charge, forecast charge, operational charge, data collection charge, administration, and climate levy. Having that day-to-day control is now imperative.”
“Fans come in all shapes and sizes and generally push out a set quantity of air for every kw of power used. That is great if they are the correct size for the job in hand, but bad news if they are not correctly sized. In our experience, grain fans used in potato stores can consume 35% to 40% more energy than correctly-sized fans that are designed for the job. And always remember that new fans are likely to be far more efficient than old ones.”
“They also need to be correctly matched to the ducts and laterals used in a bulk store, or the pressure in them may rise to above the fans’ characteristics.”
“The savings reduce when they run at lower speeds, but at that stage it is more important to ensure you are achieving the required airflow to maintain efficiency.”
While high capacity fans are required to dry and cure crops, or to blast them if they come in wet, the key to efficient energy use is to know how far you can slow them down at other times of the year. If fans are run at 80% of their capacity, they use half the energy than at full speed.
Recirculation is essential to maintain performance, he adds. If airflow is insufficient, then the air will not move through the crop effectively, while too much movement risks wasting energy and increasing dehydration.
Most operators now use CO2 purging to counter conditions like Blackheart, but they need to be sensible about the levels they use, Ray stressed. If they try to reduce it to 1,500ppm, it consumes a large amount of energy. Even moving from higher levels – 3,500ppm to 4,500ppm – makes a huge difference.
Similar issues affect fridges, with poorly performing units often using double the energy of efficient ones, while still struggling to achieve the same effect.
If the coil temperature is too low, it can trigger a succession of problems, starting with fans having to run longer than ideal, the potential for premature icing which may restrict airflow, air short circuits and expansion valves shutting.
De-frosting then puts unwanted heat back into the store and uses more energy. A control system enables this to be monitored and will highlight any problems, while adiabatic cooling can help with humidity, Ray added.
Ray recently led an Innovate UK-funded industry project examining the efficiency of box stores which showed that suction chambers can help improve air flows by up to 65%. Even greater improvements were achieved by the addition of features such as plenum walls and side/top sheets.