The new HMI 4.0 is a central element in machine operators’ everyday work and for the connectivity of Bosch’s industry 4.0 solutions. Thanks to the guided workflow, tasks can be completed even quicker and more efficiently. (Courtesy: Bosch)
Bosch presents the connected factory, Industry 4.0 at Interpack
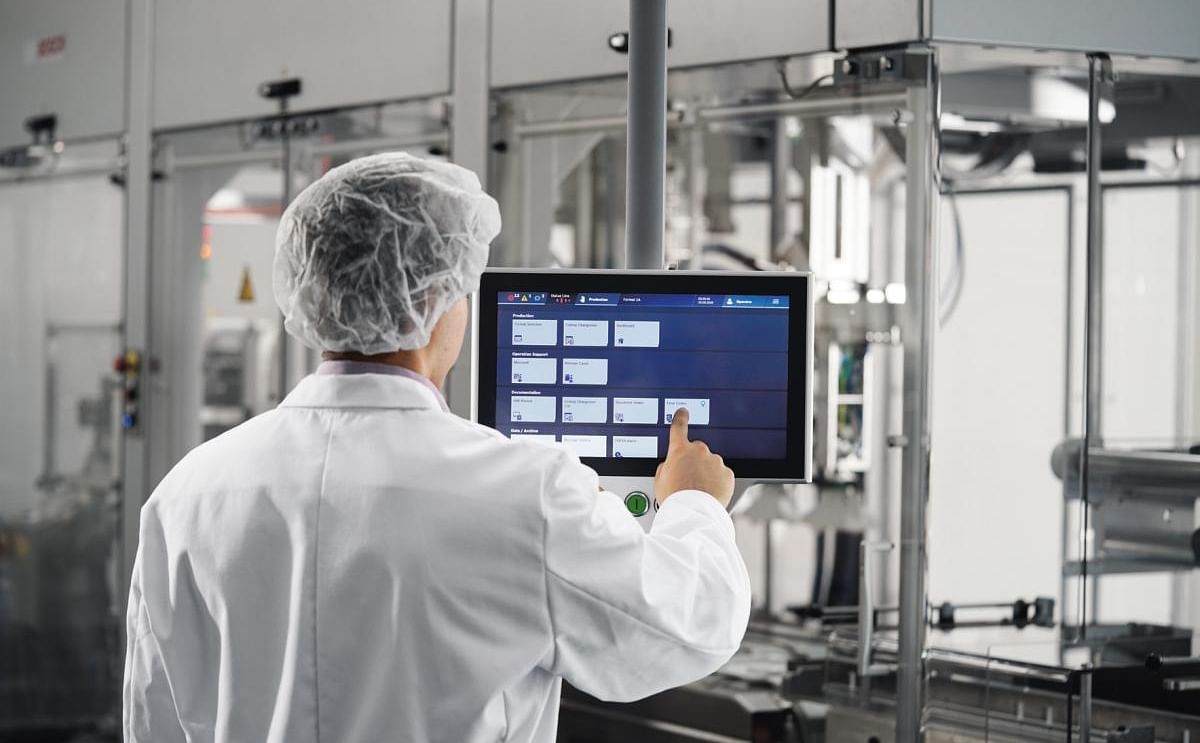
At interpack 2017, Bosch Packaging Technology will show that the connected factory is becoming reality in the process and packaging industry.
Stefan König, president of Bosch Packaging Technology:
“How can we increase productivity, efficiency, quality and safety through Industry 4.0 solutions?”
“At our booth, we will provide answers during live demonstrations.”
“Thanks to the optimum connectivity of machines and IT, we do not only achieve higher transparency throughout the entire value chain.”
“Our solutions also use the possibilities of digitization to support companies and staff in optimizing their processes and workflows in a completely new way. This will help us raise production performance and productivity to a new level.”
Support for more productive work processes
Machine operators, maintenance staff and production managers come across Industry 4.0 solutions from Bosch in numerous processes during their daily work.
For instance, the shift manager can present all relevant production parameters and data, as well as production targets and tasks in an easy-to-understand, paperless manner to his employees on the Shopfloor Dashboard in real-time.
This saves time and simplifies production and shift planning for those in charge.
The next generation Human Machine Interface developed by Bosch, HMI 4.0 is a central element in machine operators’ everyday work and for the connectivity of Bosch’s Industry 4.0 solutions.
Thanks to comprehensive data collection, transfer and visualization, the HMI 4.0 forms the basis of machine operation.
The easy, guided operation leads employees through all process steps, and enables them to complete their tasks even quicker and more efficiently.
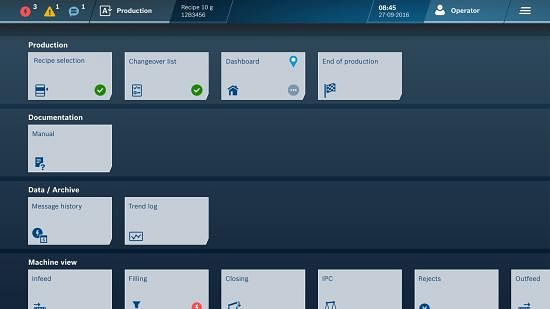
Human machine interface HMI 4.0 with improved functions
Maintenance support for higher performance
Planned and unplanned maintenance activities are an integral part of production. However, they significantly influence productivity by consuming a lot of time for diagnosis and organization. With the Maintenance Support System (MSS) from Bosch, itineraries, repair times and the search for spare parts is reduced considerably.
Once a problem is detected, a service order is sent immediately. Service personnel receive all relevant information on their mobile devices, so that they can check the availability of spare parts and complete the maintenance assignment efficiently thanks to detailed instructions.
If manufacturers require support in planning their maintenance activities due to time or capacity constraints, Bosch offers them tangible assistance with the Condition Monitoring Service.
Bosch experts continuously monitor the customer’s machines and their condition, for instance via the Bosch IoT cloud. In case of deviations, they send maintenance recommendations, as well as information about the availability of spare parts and service technicians by email or text message.
Customers can now proactively plan maintenance appointments, reduce machine downtime to a minimum, organize their spare parts stock more efficiently, and ultimately increase productivity across the entire facility.
Keeping an eye on OEE and energy consumption
Production transparency is a fundamental prerequisite for higher Overall Equipment Effectiveness (OEE) – which is the main goal of the management and analysis tool Shopfloor Management Cycle (SMC).
By bundling and visualizing production and machine data transparently, the tool enables production managers to determine the current OEE.
Based on the SMC, they perform a target/actual comparison of quantities or cycle times, and have the results visualized, for instance in pareto diagrams.
Faults such as downtime or bottlenecks are easy to identify and to troubleshoot. Moreover, the optimization of production planning and processes is facilitated.
Stefan König:
“Thanks to the additional ‘Management View’ function, production managers always have an overview of their machine status at any time – also across several facilities.”
A detailed overview of a facility’s energy consumption is provided by the Energy Monitoring platform from Bosch.
Special sensors evaluate consumption, for instance of compressed air or electricity. The data is processed and visualized on the Energy Monitoring platform.
This way, fluctuations, peaks and irregularities, as well as potential for energy and cost savings can be identified.
Moreover, defects are easier to localize, for example if a machine uses more compressed air due to a leakage. This reduces time-consuming troubleshooting, avoids unnecessary energy costs, and increases both machine utilization and performance.
Developments to be continued
Stefan König:
“Apart from the marketable Industry 4.0 technologies showcased at interpack, we are constantly developing new solutions for the connected factory of the future.”
“In the not too distant future, we will bring much more intelligence into the machines, so that they can adapt to alterations, and prevent or troubleshoot defects independently.”
An exemplary application can be seen on a vertical packaging machine: an integrated sensor precisely detects when the product falls, and adapts the sealing movement and the multi-head weigher automatically.
Stefan König:
“This way the speed of the machine can be maximized without a product being sealed in the transverse seam. That’s a new level of productivity!”