Significantly increased line efficiency and productivity at Potato Processor
Scott end-of-line automation increases efficiency and productivity at UK Potato Packer
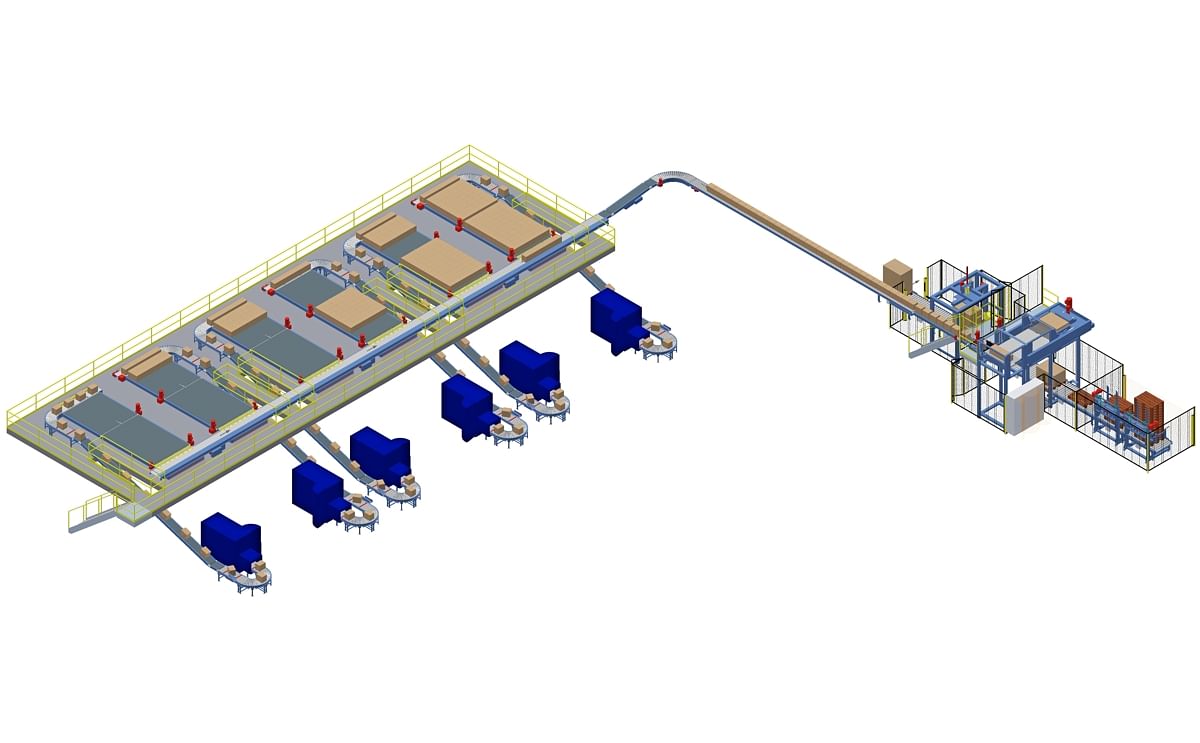
A major capital investment is now paying big dividends at a leading East Anglian veg packer. With multiple lines and manually driven packing and palletising, a decision was made to increase bagging rates, increase flexibility and remove all manual handling.
The project required the installation of 6 new automated bag packing lines handling a variety of plastic crates for the private label sector.
These crates or RTPs were both folding or so-called bale arm types, which required careful and precise packing of product up to 20 kg in weight, with bale arm closing and checking, at up to 13 crates per minute, per line. The nature of the product, the crates and the weights made for a challenging solution.
After careful assessment of the solutions offered, the customer chose Scott as one of the three partners required to work together on this project. Bag handling, orientation and packing was delivered by BPA, crate bale arm closing by Autarky and crate handling, buffering, palletising and wrapping by Scott.
With factory floor space tight, and access to each line required for empty crates and operators, the customer opted for the proven "multi-line" solution, where packed product is elevated up onto a mezzanine floor and buffered on simple, low maintenance, modular belts.
The buffering has the benefit of "disconnecting" the packing and palletising processes, which significantly reduces minor stoppages and increases line efficiencies.
Once a full load is ready, it passes to a queuing system and is then, in turn, conveyed directly into the warehouse, dramatically reducing handling and fork truck activity. The palletising is carried out on the latest generation Alvey PL8000 model layer palletiser.
Importantly, the palletising process guarantees that these crates, which must be lined up exactly one on top of the other to avoid toppling, can be handled accurately, reliably and at high speed. Crates like these do tend to sway when stacked, so clamping the load as it is built up delivers this accurate repeatability.
Additional benefits of the Multi-Line solution are:
All parties in the project worked together successfully, and supportively, with the in-house project team managing successfully the unenviable task of maintaining full production whilst installing all of this multi-million investment.
Operations team of UK Potato Packer:
The project required the installation of 6 new automated bag packing lines handling a variety of plastic crates for the private label sector.
These crates or RTPs were both folding or so-called bale arm types, which required careful and precise packing of product up to 20 kg in weight, with bale arm closing and checking, at up to 13 crates per minute, per line. The nature of the product, the crates and the weights made for a challenging solution.
After careful assessment of the solutions offered, the customer chose Scott as one of the three partners required to work together on this project. Bag handling, orientation and packing was delivered by BPA, crate bale arm closing by Autarky and crate handling, buffering, palletising and wrapping by Scott.
With factory floor space tight, and access to each line required for empty crates and operators, the customer opted for the proven "multi-line" solution, where packed product is elevated up onto a mezzanine floor and buffered on simple, low maintenance, modular belts.
The buffering has the benefit of "disconnecting" the packing and palletising processes, which significantly reduces minor stoppages and increases line efficiencies.
Once a full load is ready, it passes to a queuing system and is then, in turn, conveyed directly into the warehouse, dramatically reducing handling and fork truck activity. The palletising is carried out on the latest generation Alvey PL8000 model layer palletiser.
Importantly, the palletising process guarantees that these crates, which must be lined up exactly one on top of the other to avoid toppling, can be handled accurately, reliably and at high speed. Crates like these do tend to sway when stacked, so clamping the load as it is built up delivers this accurate repeatability.
Additional benefits of the Multi-Line solution are:
- Minimal pallet conveying hardware on the warehouse floor.
- Immediate delivery of the required empty pallet to the palletising position.
- Extremely small factory footprint.
- Immediate delivery of the full load to the wrapping position.
- Upwards of 50 crates a minute are being handled and up to 50 pallets per hour secured and delivered to the despatch bay.
All parties in the project worked together successfully, and supportively, with the in-house project team managing successfully the unenviable task of maintaining full production whilst installing all of this multi-million investment.
Operations team of UK Potato Packer:
"It’s good kit, and we like it. It was a great team effort. In these difficult times, we now have a robust production process and can guarantee continuity of supply to our key customers."
Like to receive news like this by email? Join and Subscribe!
NEW! Join Our BlueSky Channel for regular updates!
精选企业
Sponsored Content
Sponsored Content
Sponsored Content
Sponsored Content
Sponsored Content