Key Technology's new vibratory conveying systems designed to feed pick-and-place robots on packaging lines
Key Technology Introduces New Conveying Systems for Robotic Pick-and-Place Packaging
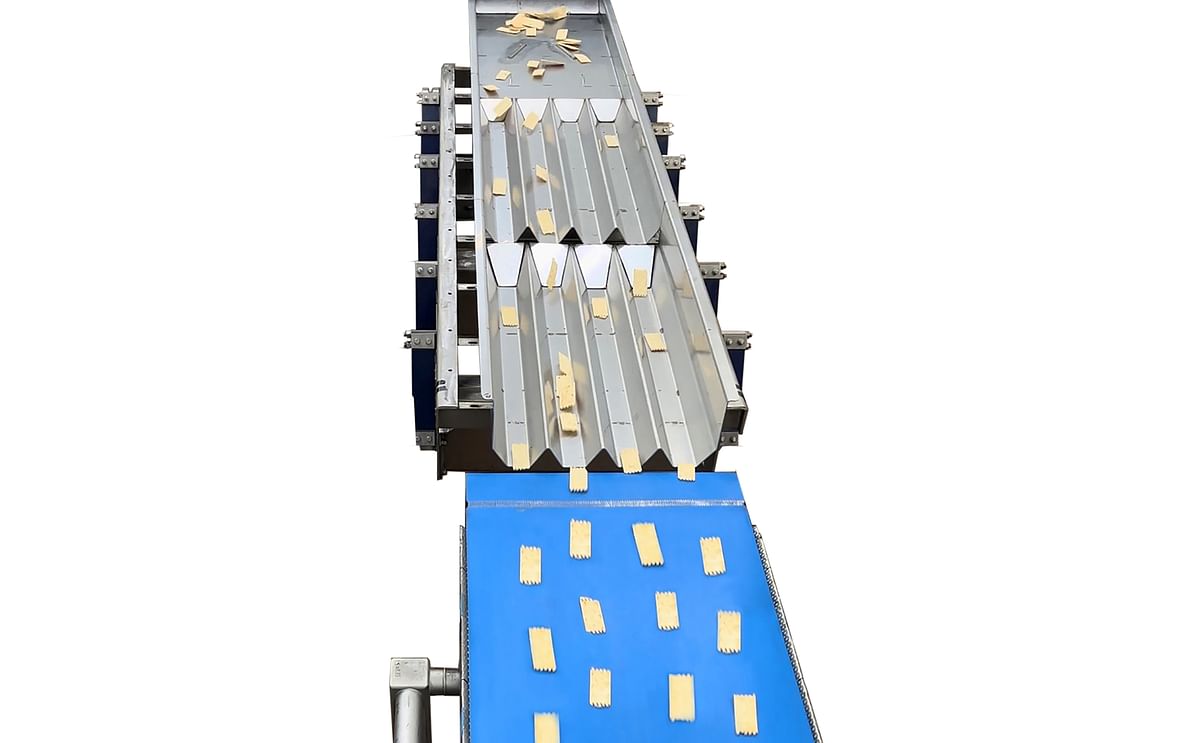
Key Technology, a member of the Duravant family of operating companies, introduces their new vibratory conveying systems designed to feed pick-and-place robots on packaging lines.
Each series of integrated conveyors meters, separates, singulates and/or aligns product, depending on the application, to provide the optimal product separation, speed and orientation for ideal presentation to the robotic system for pick-up. By minimizing hand packing, these new systems help increase production efficiency, reduce labor and improve sanitation.
Jack Lee, Duravant Group President - Food Sorting and Handling Solutions:
The integrated conveying system often begins with an optional shaker or belt conveyor to meter product, if needed. Then, a separating shaker evenly spreads product, followed by a singulating shaker that directs product into single-file lanes. The next shaker aligns the product in the correct direction, if required, and achieves the optimal speed to feed one or more pick-and-place robots, which are installed on one or both sides of the conveyor. Products that are not picked up by the robots can either be collected in a hopper or recirculated to the beginning of this system.
Key’s robust vibratory conveyors are designed for superior sanitation with stainless-steel bed surfaces, open designs and oil-free drives. When a processor automates primary packaging, sanitation is further enhanced by eliminating the manual handling of unpackaged products in the packing process while reducing the chance of accidental foreign material contamination by a worker.
Key manufactures conveyors and other equipment in both the U.S. and Europe, supports customers worldwide through its extensive sales and SupportPro service network and offers integration services, from pre-engineering to line start-up. Key’s conveyor beds and structural components are backed by their industry-leading, five-year warranty.
Each series of integrated conveyors meters, separates, singulates and/or aligns product, depending on the application, to provide the optimal product separation, speed and orientation for ideal presentation to the robotic system for pick-up. By minimizing hand packing, these new systems help increase production efficiency, reduce labor and improve sanitation.
Jack Lee, Duravant Group President - Food Sorting and Handling Solutions:
"As a food processor grows, they come to a point when hand packing has to be minimized or is no longer feasible. Manually packaging, especially 24/7 with several workers at a time, is expensive, inconsistent and can be unsanitary, plus these jobs are physically grueling with high turnover. It’s a huge pain point for many of our customers – automation makes sense."Key designs, builds and then tests every integrated conveying system to identify the optimal speed, stroke, lane widths and step sizes to consistently present the processor’s products to the robot’s end of arm tooling. Suitable for primary or secondary packaging, these systems can handle frozen foods such as potato products, meat, poultry and seafood as well as dry products such as cookies, pet treats, confectionaries and snacks.
"The challenge is that lining up products for presentation to a pick-and-place robot requires a degree of precision that’s unusual in conveying. Drawing on our team’s deep expertise, we work closely with each processor to design the perfect solution for their specific application."
The integrated conveying system often begins with an optional shaker or belt conveyor to meter product, if needed. Then, a separating shaker evenly spreads product, followed by a singulating shaker that directs product into single-file lanes. The next shaker aligns the product in the correct direction, if required, and achieves the optimal speed to feed one or more pick-and-place robots, which are installed on one or both sides of the conveyor. Products that are not picked up by the robots can either be collected in a hopper or recirculated to the beginning of this system.
Key’s robust vibratory conveyors are designed for superior sanitation with stainless-steel bed surfaces, open designs and oil-free drives. When a processor automates primary packaging, sanitation is further enhanced by eliminating the manual handling of unpackaged products in the packing process while reducing the chance of accidental foreign material contamination by a worker.
Key manufactures conveyors and other equipment in both the U.S. and Europe, supports customers worldwide through its extensive sales and SupportPro service network and offers integration services, from pre-engineering to line start-up. Key’s conveyor beds and structural components are backed by their industry-leading, five-year warranty.
Like to receive news like this by email? Join and Subscribe!
NEW! Join Our BlueSky Channel for regular updates!
精选企业
Sponsored Content
Sponsored Content
Sponsored Content
Sponsored Content
Sponsored Content