Ellips, a manufacturer of optical grading equipment for individual potatoes, highlights the top challenges in potato grading and how to tackle them.
Ellips highlights the top challenges in potato grading and how to tackle them
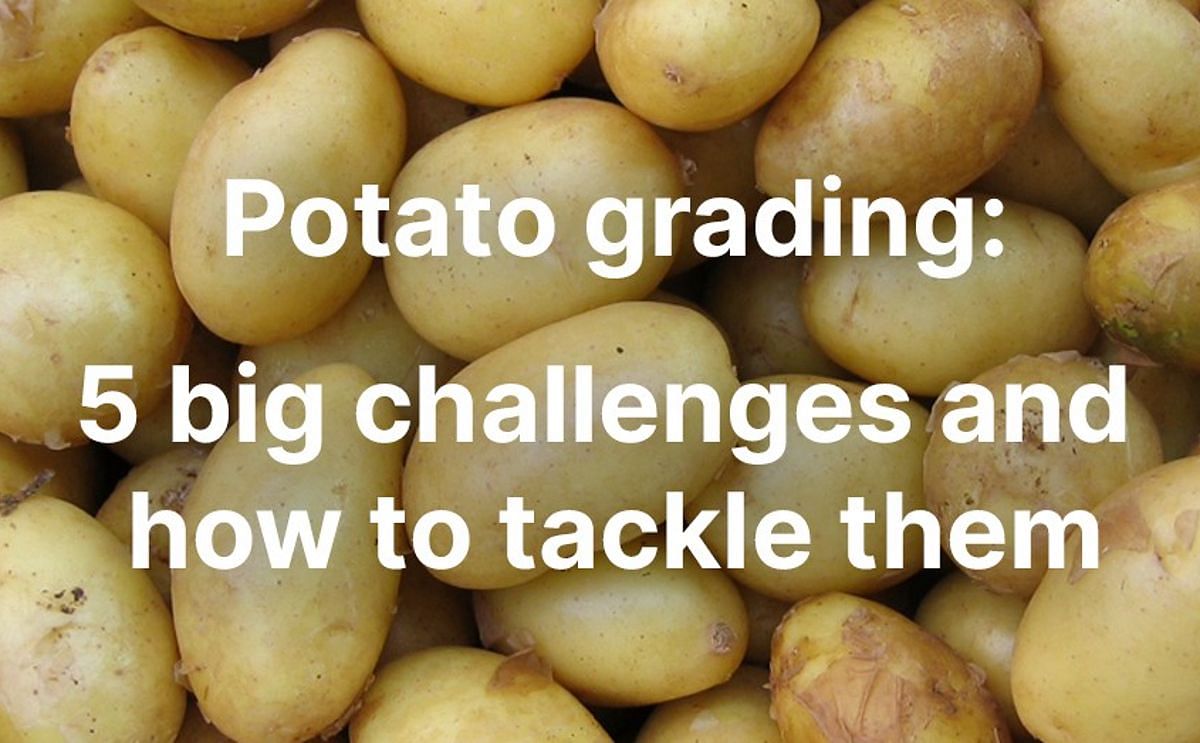
Ellips, a manufacturer of optical grading equipment for individual potatoes, highlights the top challenges in potato grading and how to tackle them.
When it comes to potato grading, growers and packers face a lot of challenges. In most cases, this effort requires many people who are tasked with manually assessing the quality of the product to meet the standards of their customers.
Based on this process, grading and sorting is often the limiting factor to increased production. Additionally, if there are internal quality issues, it is not possible for manual sorters to determine the presence of internal defects. Until now, there was no clear-cut solution.
There are 5 biggest challenges:
- Assessing internal quality
- Infection of good produce
- Efficient handling and grading of different shapes and sizes
- Increasing potato sorting capacity
- Shortage of good employees
But first: machinery and software must work together
When it comes to product throughput, efficiency, and quality, machinery and software must work seamlessly together to achieve the best result. The robust Elisam GranTorino Potato Grader coupled with our Ellips Grading Software forms the perfect potato grading and sorting solution.
Additionally, our technology ensures a maximum return on your harvest, while delivering exactly what your customer desires.
1. Assessing internal quality
When it comes to grading potatoes, you can sort your products based on the external quality (I.e., size, color, and weight). But the quality of the outside of your potatoes doesn’t necessarily guarantee the quality of your product as a whole.
While the outside of the potato might meet all the quality standards your customer expects, the internal quality may leave much to be desired. Potatoes can be affected by various internal diseases or defects like flecking, glazing, hollow hearts. To guarantee the desired quality, it is important to assess products both externally and internally.
Assessing 'under the skin' defects
It’s not possible to cut every potato – random quality control checking takes a lot of time, ruins a substantial part of products, and doesn’t guarantee the internal quality of every single potato.
Utilizing near-infra-red technology has enabled some limited detection of 'under the skin' defects. However, this only provided quality assessment a few millimeters underneath the skin which doesn’t provide a reliable indication of the overall internal quality of your produce.
The solution is an Elisam GranTorino potato grader that uses light transmission technology. This technology, give the possibility to see completely through the product (instead of just underneath the skin) by virtually ‘slicing’ potatoes into pieces.
Virtually slicing potatoes
The technology uses the spectra of transmitted light. Every potato will be virtually sliced into up to 20 slices. For each slice, the solution measures the absorption and transmission of different infra-red frequencies. Based on this ratio, it determines the internal quality of the entire potato.
2. Infection of good produce
The second challenge in grading potatoes is similar to the previous one because there are, at least, two reasons to examine potatoes for internal defects:
The quality of products should meet the customer's demands
- Avoiding good products from infected
- Removing potatoes with early-stage defects
Finally, their transmittance technology is so advanced that it can detect very small internal characteristics and defects. And their software can be set to your demands, so you can choose the characteristics and defects you want to assess.
When it is possible to remove potatoes with certain defects from your product, you’ll protect the products that will be delivered to your customers.
This will help maximize your returns by avoiding rejections while ensuring that your product meets the quality and consistency demanded by your customers. This means less food waste and an increase in the value of your harvest.
3. Efficient handling and grading of different shapes and sizes
The third challenge associated with effectively grading potatoes involves the ability to handle different varieties with a diversity of size and shape.
John Albert, General Manager of Ellips USA:
"Red potatoes can be round, while yellow and white potatoes can be oblong. The unique design of our Elisam GranTorino potato grader ensures that all potatoes (regardless of size and shape) can be run at high capacity while still achieving a consistent 360° rotation of each potato under the Ellips TrueSort optical grading technology."
"TrueSort utilizes hi-resolution multispectral cameras to take 90 photos of every potato while it rotates underneath the lens."

Efficient handling and grading of different shapes and sizes
Wrongly rejected potatoes
This capability enables you to deliver a consistent pack to your customers without the need for manual grading and sorting potatoes. In addition, fewer products are wrongly rejected which helps ensure a maximum return on your harvest while delivering exactly what your customer desires.
Dave Hughes, the Owner of Hughes Farms:
"The grading is so much better and we can finetune it, such that a potato that we might have thrown out last year, we have used for it this year. Just more efficient."
4. Increasing potato sorting capacity
When it comes to growing revenue, they believe that they know how to help. In bottom-line terms, it is very simple: you must be able to grade more potatoes in less time, with less labor, and with better quality and consistency.
Poor quality batches (lots) decrease capacity
Due to the increased frequency of severe/challenging weather conditions and more stringent regulations regarding the use of pesticides, potato quality is declining in some areas of the world. As a result, processing capacity decreases, and more employees are needed for grading.
That is why Wilhelm Weyers has chosen automation to help address these issues. Wilhelm Weyers started using the Elisam Grading potato grader in 2021.
Reinhard Krebbers, General Manager at Wilhelm Weyers:
"When we would still sort by hand, we would need about two people to grade a good batch. But with a bad quality batch, we would need eight or even ten people. But regardless of the quality of the batch, we are still able to sort the same capacity."
So even with a lower quality batch, Wilhelm Weyers increased their capacity and can sort more potatoes in less time.
The problem with organic (biological) potatoes
This is also crucial when you think about new regulations regarding the use of pesticides (especially in Europe). Growers must reduce the use of pesticides and grow more organic potatoes. Unfortunately, the quality of organic potatoes is not generally as high as conventional potatoes which means more employees are needed for grading your potatoes.
Sorting up to 36.000kg (80.000lbs) potatoes per hour
Depending on potato size, their solution can grade and sort over 4500kg (10.000 lbs )of potatoes per hour per lane. The Elisam potato grader is configurable based on the number of lanes and exits required.
So, with only two lanes it's possible to reach a capacity of 9000kg (20,000 lbs) per hour while a configuration including eight lanes would enable to achieve a capacity of 36.000kg (80.000 lbs) of potatoes per hour. This capacity is 2-4 times higher than other potato graders.
5. Shortage of good employees and reducing labor costs
GranTorino’s ability to grade based upon external and internal attributes is much more accurately than could ever be accomplished manually. It’s also evident that due to the sorting speed of the machine, the capacity is much higher (regardless of the quality of the batch) than other potato sorting equipment, let alone human hands.
In addition to these advantages, it is also very difficult to find (and keep) good employees these days. Automating the sorting process is a great solution to this problem.
In addition to addressing the labor availability problem, their solution delivers significant reductions in labor costs and maximum yield from each batch of potatoes. In this way, their customers can achieve an ROI in less than two years.
Happy customers and a healthy business
In short, by enhancing your existing packing operation with more efficient and accurate potato grading and sorting technology, you’ll save a lot of money while delivering exactly what your customers demand. Make every potato count
Ellips can help you optimize your grading, sorting, and packing operation by supplying the most advanced potato grading technology available.
Tel: +31623612514
levi.bakker@ellips.com