Bedford Industries Launches Plant-Based Bag Closure
Bedford Industries Launches Plant-Based Bag Closure
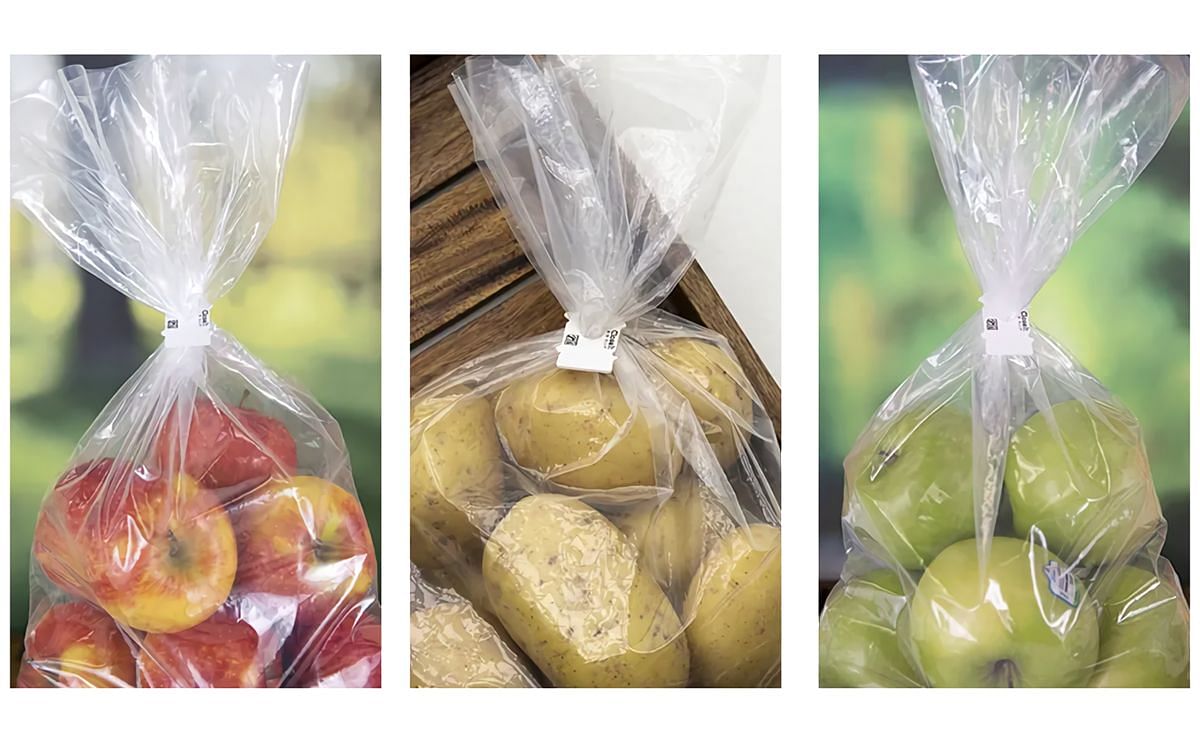
Bedford Industries today introduces CloseIt® Bio-Clip, its new plant-based bag closure containing 100% USDA certified biobased content that is commercially compostable.
A global leader in producing packaging solutions for the produce, bakery, coffee, and medical industries, the Minnesota-based manufacturer set the ambitious goal of creating a compostable clip upon introducing its line of CloseIt clips in 2018.
Jay Milbrandt, Bedford President:
Composed of materials derived from plant, marine, or agricultural resources, Bio-Clip far exceeds the minimum compostability requirements set forth by each certifying body.
Milbrandt said Bio-Clip presented unique engineering challenges to Bedford’s research and development team, who was tasked with developing a greener closure without sacrificing product quality.
Jay Milbrandt:
A global leader in producing packaging solutions for the produce, bakery, coffee, and medical industries, the Minnesota-based manufacturer set the ambitious goal of creating a compostable clip upon introducing its line of CloseIt clips in 2018.
Jay Milbrandt, Bedford President:
"We set out to do something that had not been done: deliver a closure that met global compostability standards and was made from biobased materials."Bio-Clip earned BPI Commercial and OK Compost Industrial certifications after undergoing rigorous evaluation by the certifying organizations in the United States and Europe, respectively. These certify Bio-Clip is compostable where industrial/commercial compost services are available. Bio-Clip also exceeded USDA ASTM D6866 testing requirements to become a USDA Certified Biobased Product.
Composed of materials derived from plant, marine, or agricultural resources, Bio-Clip far exceeds the minimum compostability requirements set forth by each certifying body.
Milbrandt said Bio-Clip presented unique engineering challenges to Bedford’s research and development team, who was tasked with developing a greener closure without sacrificing product quality.
Jay Milbrandt:
"Not only did we have to develop a proprietary biopolymer that would work in current automation equipment, but we also had to develop a printing technology that could deliver meaningful instructions to the end user on how to dispose of the closure."Belinda Heidebrink, Marketing Specialist:
"We’ve long been hearing about our customers’ ambitious sustainability goals for their packaging. It has been inspiring to do business with other companies that share our common goal in delivering quality products that are mindful of the environment."
Like to receive news like this by email? Join and Subscribe!
Join Our Telegram Channel for regular updates!
精选企业
Sponsored Content
Sponsored Content
Sponsored Content
Sponsored Content
Sponsored Content