View on the French Fry processing line in the McCain Foods New Zealand -Timaru production plant (Courtesy: Andar Manufacturing Engineers)
Finding opportunities to save energy in potato processing: McCain Foods Timaru
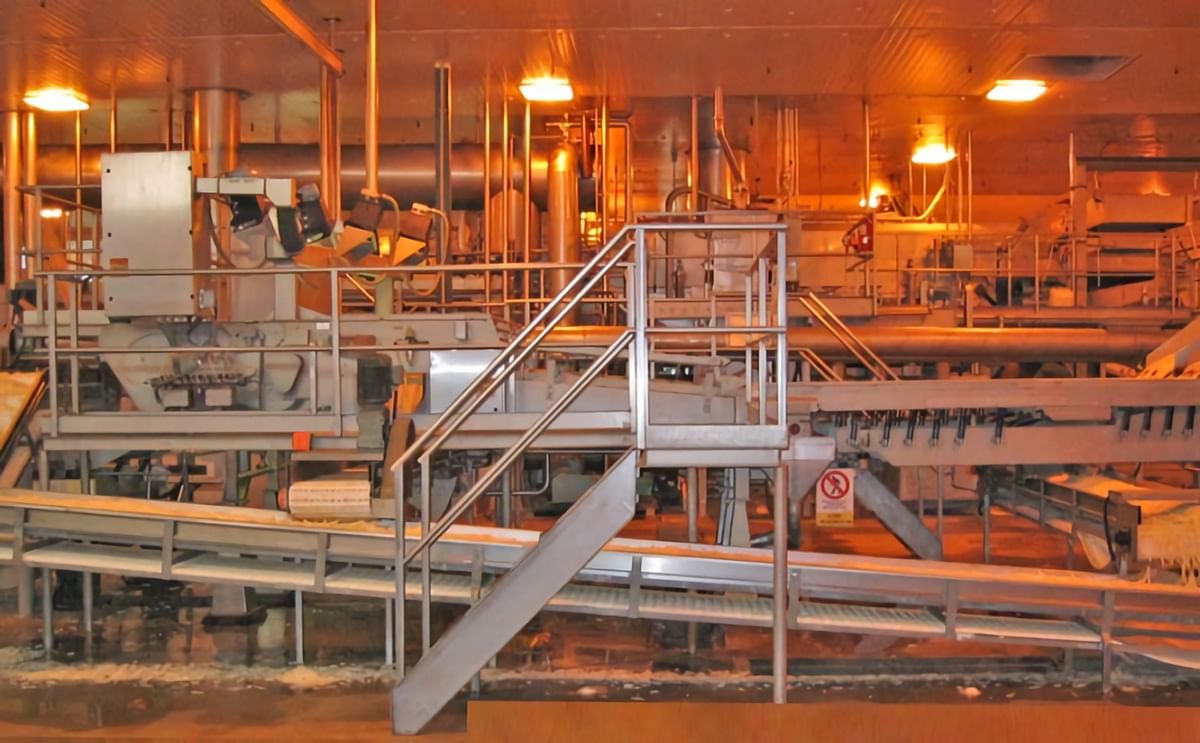
Management at one of McCain Foods’ processing plants in Timaru, New Zealand, has found over 100 opportunities for improvement in its logistics following a two day “energy blitz” from employees.
Production Manager Sonny Quilliam explains the thinking behind the move, with energy efficiency being key to the facility’s operations.
Sonny Quilliam, Production Manager:
“We’d picked all the low hanging fruit through previous work but we needed ideas to generate more energy and water saving opportunities.”
“We knew they were there but we needed to shine a light on possibilities.”
Twenty people from all areas of the facility that produces 146,000 tonnes of french fries annually took part, from management to factory floor workers.
Armed with a checklist to prompt team members to look for common energy-saving opportunities, the team scoured every area of the plant, including the production plant, boiler house, cold store, potato storage, dry store, refrigeration and administration.
The morning effort concentrated on energy loss, with water losses being the main focus in the afternoon.
At the end of the day, the teams came back and every idea, big or small, was put on the table. The energy management experts then organised the opportunities in a spreadsheet - an impressive 113 in total.
On day two, the full blitz team went through a prioritisation process, ranking ideas against criteria such as implementation time, approximate cost and likely benefit.
The top 20 were selected for immediate action and the remainder placed on the long list to be addressed in due course.
At the top of the list is a big project to optimise refrigeration systems that will save both heat and water. Other priority work includes recycling heated water instead of heating cold water from scratch, removing a pump that is no longer needed, fixing steam and water leaks and fitting flow nozzles to hoses used for washing down.
Sonny Quilliam:
“I was delighted with what we achieved.”
“Completing the prioritised projects will reduce energy and water use and save thousands of dollars a year.”
“This frees up energy and water for the local community and allows us greater freedom to invest back in the business.”
Can your business benefit?
Businesses of any size can benefit from a hunt for wasted energy, says Paul Bull, business account director at the Energy Efficiency and Conservation Authority (EECA) in New Zealand.Paul Bull:
"An exercise like this helps to identify opportunities companies can act on immediately.”For a checklist of simple ways to save money on energy bills in offices and on industrial sites, visit www.eecabusiness.govt.nz.
“The blitz worked well because it was well planned and had a clear scope. Also, the way staff were involved throughout the process gave them a strong sense of ownership."
Research exercises like this can be greatly beneficial to businesses, with the Energy Efficiency and Conservation Authority quoting that firms can save up to 20% on energy costs with smarter energy use.