Information Technology is developing rapidly: the Internet of Things, Big Data, Sensors, RFID, global connectivity, all are having an impact on how factories and production chains operate now and in the future.
How a company that provides such "Industry 4.0" solutions itself applies this technology in house, would provide some useful insights, we thought here at PotatoPro.
Bosch provided the following overview of solutions on occasion of their presence at the Hannover Messe 2015. For each application, a Bosch associate explains what benefits the solution offers:
Turning inventory into a walk in the park
Zhao Chunya, product planner in Suzhou, China: “Before, we had to devote a lot of time and effort each year to doing inventory. Plant 1 alone has four manufacturing areas, each with up to 2,500 machines, test benches, and measuring equipment. The process sometimes took up to a month for ABS manufacturing alone, with some of the equipment standing idle during that time. We used to print out lists and head off in search of the equipment. Sometimes we had to crawl between the machines to find the stickers with the information.
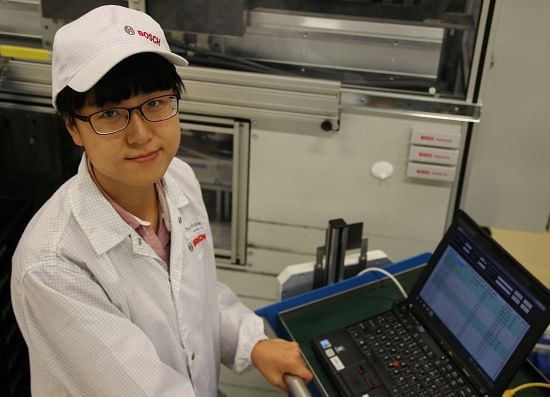
Taking a walk: thanks to RFID, Zhao Chunya saves a lot of time when doing inventory.
All that has changed completely. Now I’m able to do it alone in just four hours. We fitted all of the machines and equipment with RFID transponders. This allows objects to be identified without physical contact. We then built this RFID trolley with antennas on the side. I download an inventory list from the network to my laptop. Then I push the trolley through the aisles along a prescribed route. Little by little, the machines and devices are automatically identified thanks to the RFID technology. As they are, more and more lines on my spreadsheet turn green. It cuts the time needed for inventory by 97 percent, or 440 man-hours.
In the future, we plan to replace the RFID transponders with connected sensors. That would mean we wouldn’t even need to do the walking part. And I could spend more time focusing on my real job. I am a product planner, after all!”
The warehouse talks to the supplier
Attila Szabó, machine accessories and spare parts coordinator in Hatvan, Hungary: “We have about 5,000 machines for the various production and testing processes at our plant, which are very different from one another. Some of them are 15 years old, while others are much newer. That’s why we need lots of different spare parts. So far we’ve equipped the majority of them with RFID transponders.
As a result, we need only twelve man-days for inventory – instead of 180. I can focus more on improvement processes now. What’s more, we’ve also partly automated the ordering process thanks to this technology. A part is automatically reordered from the supplier once its quantity dips below a certain level. We used to do that by sending an e-mail, but the process took more than two and a half days. We’ve already implemented this for 14,000 of the 25,000 part types. Soon it will be all of them.”
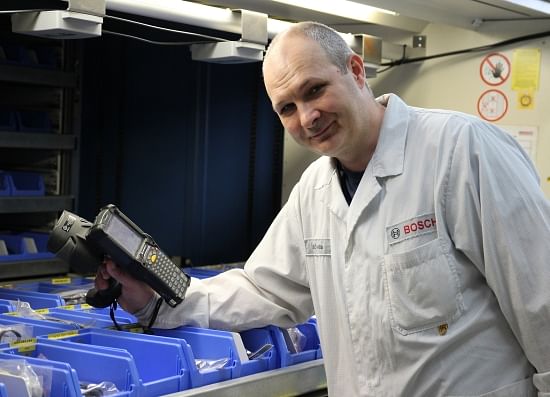
Calculated in a split second: Attila Szabó holds a scanner to the shelf and finds out how many spare parts are still on hand.
The right person to call in an emergency
Krisztián Anda, service technician in Hatvan, Hungary: “I just got a text message asking me to come to this production line in circuit board assembly right away. The operator reported a fault using a small, portable computer right at the machine. Our new system automatically notified me immediately.
In the past, the operator would have informed his or her supervisor of a problem first, then the supervisor would have called the service technician. That would sometimes take 15 minutes. And I used to get called a lot, even though I’m not an expert for this line. Thanks to the small computers and new software, we’ve cut the reaction time.
Now, on average, it’s much less than five minutes – sometimes only about 30 seconds. I can submit the support ticket on site directly into the system. I don’t need paper anymore.
Plus, all of us are only called out to look at machines that we’re familiar with, thus enabling fast and effective troubleshooting.”
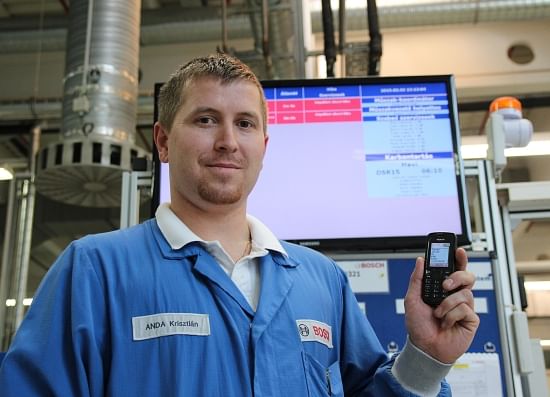
When a fault occurs, Krisztián Anda gets an SMS within seconds – if he’s the expert for that machine.
Learning with sensors
Patrick Arnold, skilled production worker in Reutlingen, Germany: “We manufacture the power electronics for electric and hybrid vehicles on this production line. At my station, I tighten a part onto radiators. We have now equipped the Bosch Rexroth nutrunner with a sensor that measures the speed at which I put the screw in and gives me feedback.
The figures are entered directly into our computer system. It additionally stores the torque and rotation angle for each screw so that we can analyze it in greater depth later. It gives you a better feel for what you’re doing and improved quality assurance.”
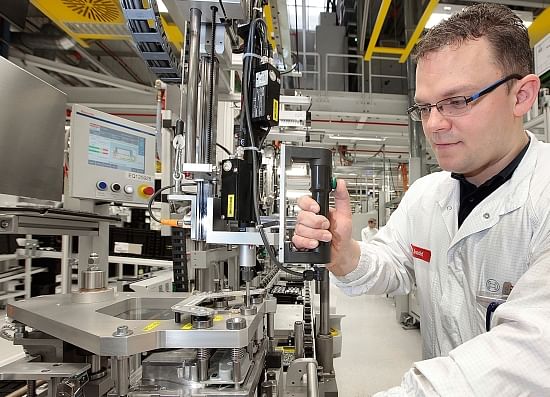
A new sensor on his tool tells Patrick Arnold whether he has tightened the screw gently enough.
Storage in production reduced by nearly one third
Andreas Müller, logistics and RFID expert at Bosch: “At the Homburg plant, we produce injection nozzles for diesel engines. There, RFID radio tags monitor the workpieces’ progress through the factory by identifying the position of transport crates. This enables precise details to be known about the process steps each piece undergoes and when the injectors will be ready.
That data, in turn, can be used to determine when the finished product will be packaged, shipped, and installed. Bosch has involved one of its suppliers (Variopack) and one of its customers (Opel) in this process, so that we can all jointly plan and produce better.
Using this system, Bosch has been able to boost productivity by ten percent in logistics alone – and reduce storage in production by nearly one third. To ensure that the systems work to the advantage of all stakeholders, we established a common standard for exchanging data.”
RFID technology
The term RFID (radio frequency identification) refers to technology that can identify objects quickly and without physical contact. RFID tags containing a code can be mounted on transport crates, spare parts, or tools, for example. A scanner uses radio waves to read the code.Depending on the type of RFID technology used, this works over a distance of anywhere from a centimeter to a meter.
Bosch is boosting the competitiveness of its factories by applying these Industry 4.0 solutions. At present, the Bosch Group has over 100 projects on this topic, with this number rising rapidly.