Potato Store design: the Dutch, the American or the British way?
Potato Store design: the Dutch, the American or the British way?
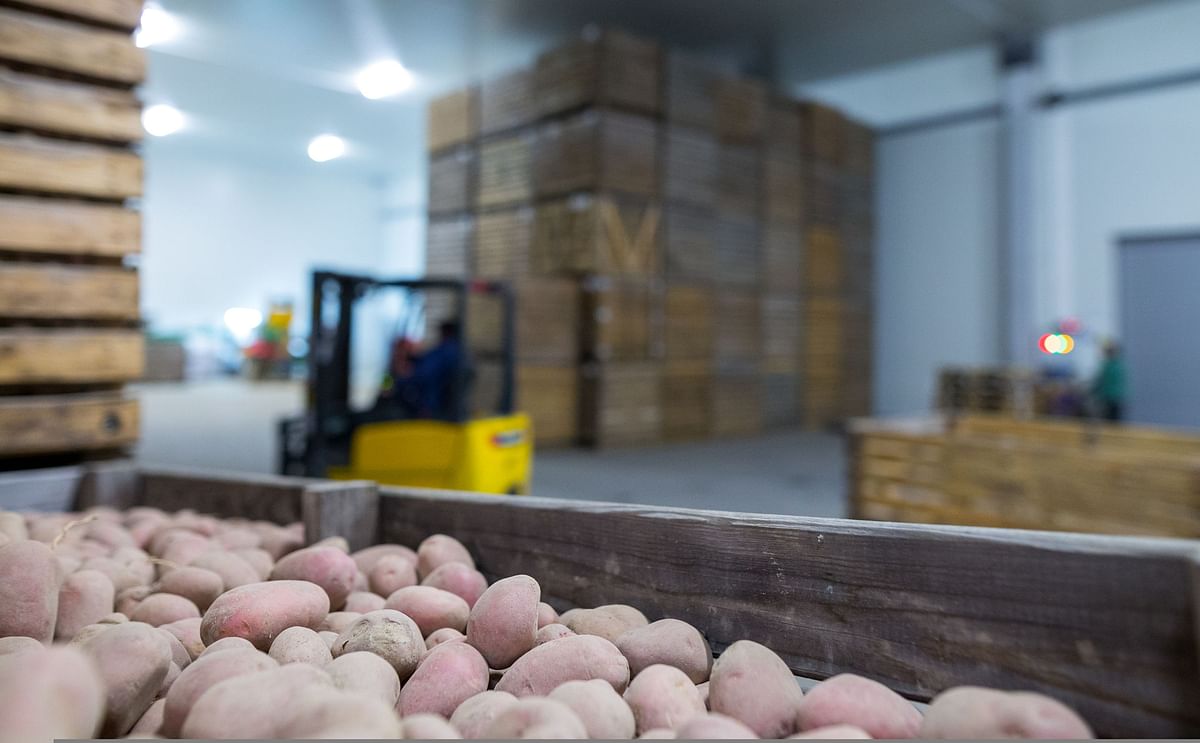
Potato store operators must ensure they specify both airflow and air pressure when planning new stores, says Ray Andrews, from crop storage specialists Crop Systems Limited.
If they only specify air flow, they run the risk that their store will not work efficiently in bad years, because the store’s fans simply will not be able to maintain airflow through wet or dirty crops.
While there is much discussion on the correct airflow at the moment – and specifically about the merits of airflows used in Dutch and American stores – he questions whether the figures these countries use are relevant for the UK. In particular he warns against quoting figures for air flow volume without pairing it with system pressure:
“British potato growers should recognize the risk of adopting systems that are not proven in British conditions. The penalty for failure is severe, and store operators should stick to some basic rules when equipping new facilities.
“Different equipment suppliers specify fans that are bare quoted at anything from 40 cubic feet per minute to 90 cubic feet per minute per tonne (cfm), but do not quote the pressure.
“The widely accepted British standard is 40 cfm at two inches water gauge pressure, a combination which has been proven over decades to be appropriate for British conditions. That is why Crop Systems Limited has always used it when designing stores.
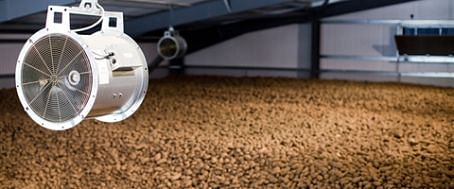
Potato Storage in bulk
“If the store is rated at 40 cfm/t and 2” water gauge you have enough pressure to move the air through a heavy soil laden crop. In good conditions the store will normally operate with about ½” pressure in the ducts – and you might find you are achieving anything up to 58 cfm/t airflow.
“But it is not uncommon to see the pressure rise to ¾” or even 1” in difficult years, and even higher in severe conditions.
“If you don’t have that extra pressure available then you might struggle to maintain air flow through the crop as it settles. You might also struggle if conditions like the increasingly common Blackleg cause patches of tubers to rot, which closes up the air gaps between tubers and can severely restrict air-flow.
“If you have insufficient pressure to maintain airflow through the filled store air flow can cease and your crop is at risk. If it cannot get through the crop, the air backs up in the ducts and causes ‘fan stall’, where the fan continues to rotate but moves no air into the store.
“A well equipped potato store is a bit like your four wheel drive vehicle: the vast majority of the time you don’t actually need the four wheel drive, but you would be stuck if you didn’t have it on those occasions that you do. The same applies to potato store fans”.

Potato Storage in boxes
Mr Andrews says adding an inverter to a poorly designed fan system and the problems multiply, while adding one to a well-designed system enables operators to run them at full speed when needed, but then cut speeds when less airflow is required:
“As you can run a fan at 80% capacity for just 50% of the electricity, there are significant cost savings to be made. In Sutton Bridge Crop Storage Research Trials (INVERTER TRIAL S402) on over 15 stores, reducing fans speed to 80% gave a corresponding volume of 80% - proof, if any were required, of the value of inverters.
“Store design needs to take into account worst case conditions, late harvests, lots of wet soil and excess tonnage. These are exactly the combination of problems that will test a store to its limits and cause it to fail if it is not well enough equipped”.