With over 50 years of knowledge and experience in the field of processing potatoes into chopped and formed products and other shredded specialties with the latest technologies and techniques, Idaho Steel, together with its global partners Kiremko and Reyco Systems, provides you with industry leading knowhow that goes far beyond simply specifying the necessary equipment.
Formed potato specialties have been around for decades. Worldwide these products are found in our diets, be it in the shape of hash brown patties, tater tots, potato pancakes or potato gems. The basis of these products typically being a shredded, grated or riced potato, formed into a particular shape, and pan-fried.
In the potato processing industry, a Form Processing Line can be a stand-alone unit or be part of a french fry plant. In the latter case, rejected and off-sized potatoes from the primary processing lines are used to create a high quality formed product and through this, improve the overall yield of the potato processing facility.
Many different products and shapes can be made, such as hash brown patties, waffles, rounds, triangles and more complex shapes like cartoon characters, letters or numbers. A formed product made with vegetables like peas and carrots mixed with potatoes, is also possible.
The products are delivered pre-fried and frozen and distributed into the same channels as french fry products.
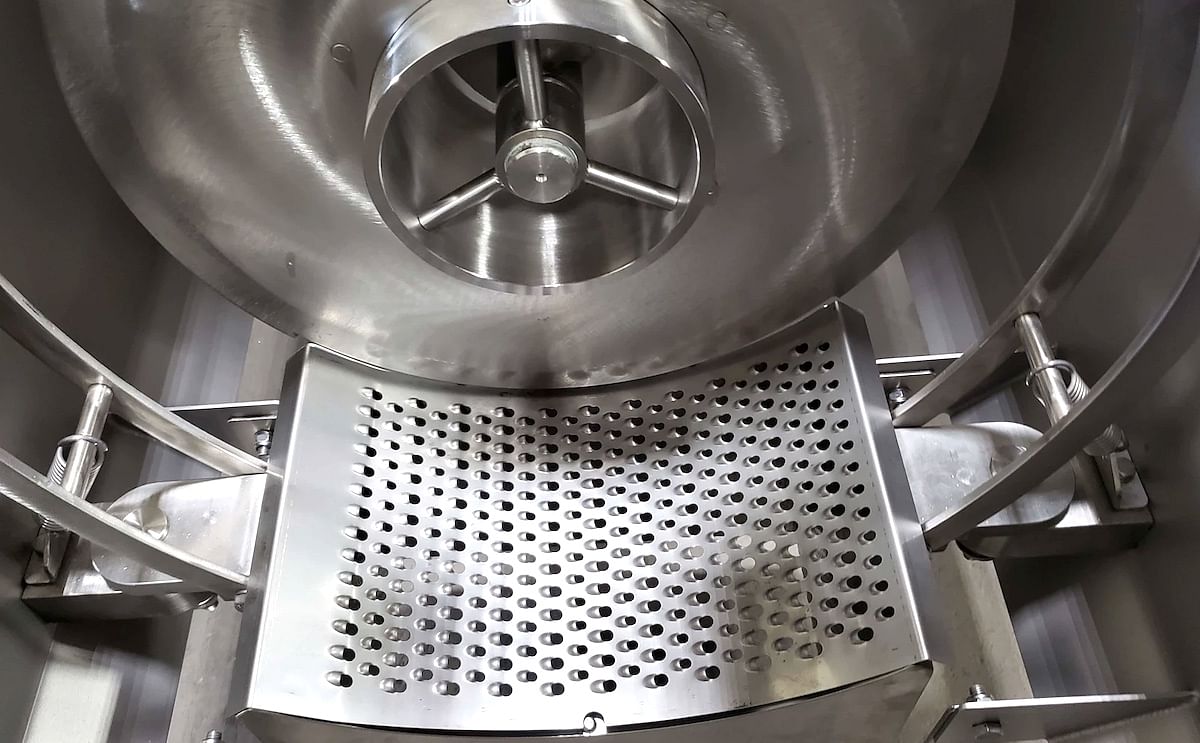
Form Line Process
Our group designs, manufactures and integrates all the necessary components to complete this process for hash brown products. From the washing and peeling lines, optical sorters, blanchers, retro-graders, shredding and mixing units, forming and frying systems up to the spiral freezer and if required, the final packaging solutions.
The machinery is designed for high capacities, ease of operation and maintenance and in compliance with worldwide safety and hygiene standards. Together with our strategic partners we have the ability to deliver small, medium, and large processing lines in all the defined market groups.
Prior to forming, the potatoes are shredded. This is done by the Nex-Shred potato shredder. The size of the shred influences the look of the product, but also the texture experienced during consumption.
With a wide range of different shredding plates, the Nex-Shred is able to shred in numerous sizes; from very fine, almost mash-like, to large potato pieces.
With the Nex-Gem Rotary Former from Idaho Steel in the heart of the process, our Form Processing Lines can be considered the most productive processing lines available. We offer complete systems from 2,000 lb/hr up to unprecedented capacities such as 20,000 lb/hr of hash brown patties in a single line.
For these high capacities, both the Nex-Gem Rotary Former and Fry by Wire specialty fryer, have been further developed to become the largest available in this particular segment.
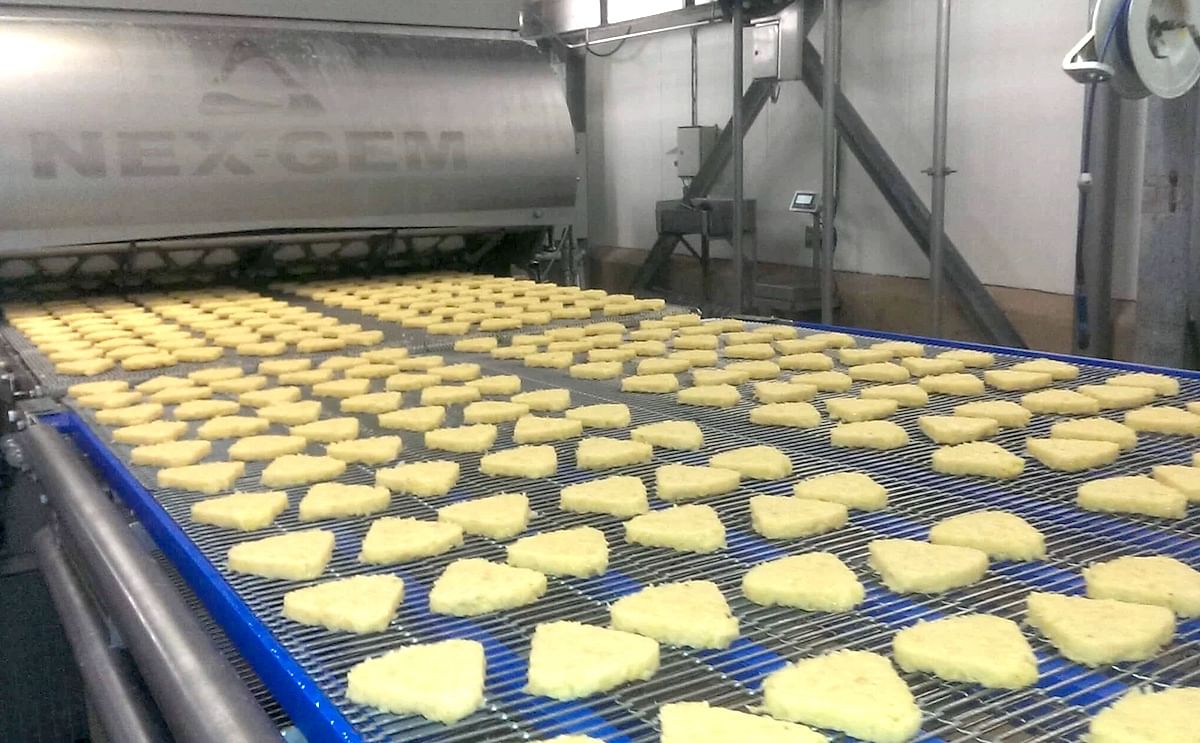
Flake Application
In the forming process it is critical that the potato shreds will hold together in the correct shape. To achieve this, the product is prepared through a series of steps to remove moisture and condition the starch cells to ensure that the shreds stick together. This is done in a unique unit called the Retro Grader.
The Fry by Wire specialty fryer is an ingenious system that maintains the frying oil level to the top level of the product. This prevents it from floating and damaging the shape or disturbing the stacking pattern on the belt, which is essential for a proper frying and freezing process.
After frying, the EcoMiser™, a unique design by Reyco Systems, is installed to recover surface frying oil. The recovered oil will then be filtered to remove crumb and reintroduced into the fryer. During this process, from the moment the formed product touches the oil, during the oil filtering process and afterwards, the freezing, the shape, consistency and color of the product will never be compromised.
Process control, data-collection and self-managing functionalities in processing lines are of increasing importance. All lines can be delivered with SCADA systems for automatic control and continuous process monitoring and data recording.