Burgess Farms boosts efficiency and quality with a new potato wash line from Haith Group at Sutton Bridge.
Burgess Farms Enhances Potato Processing Efficiency with New Haith Wash Line
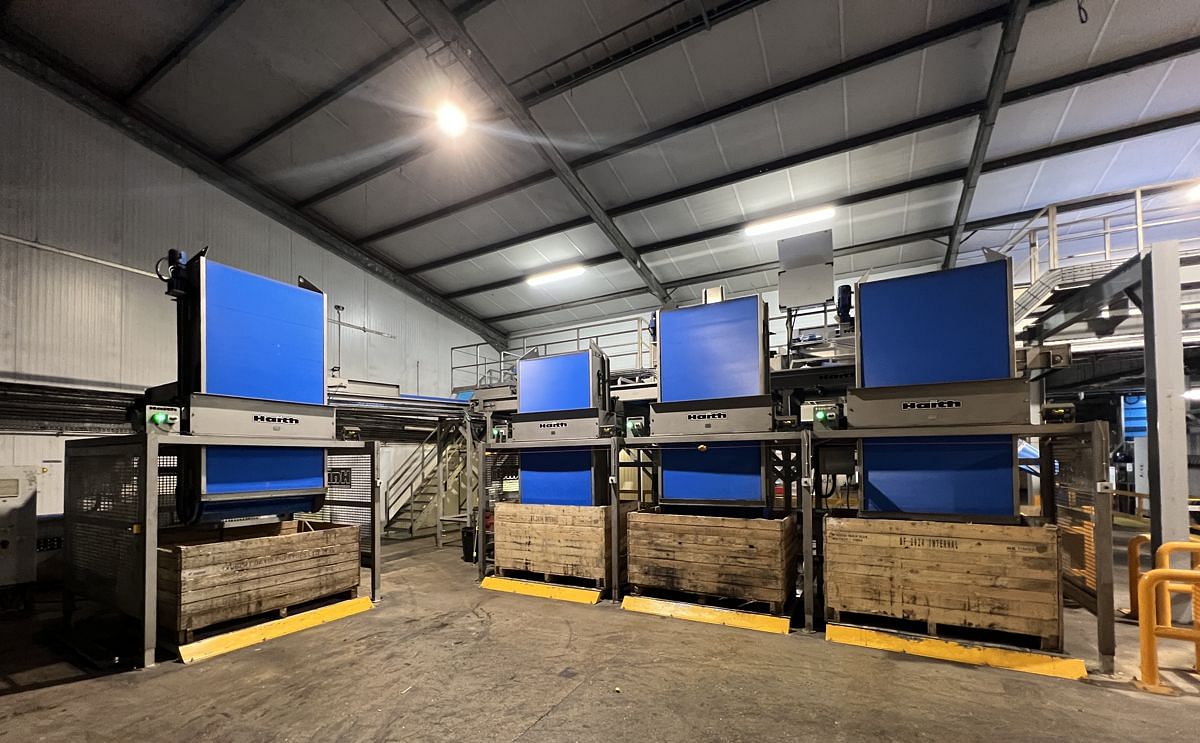
It has taken just six months for Burgess Farms to see the benefits of working with Haith Group on its new potato wash line, with the improvements being ‘clearly visible’. Installed in October last year, the new line has significantly increased Burgess Farms’ throughput and added further optical grading and sorting capabilities to the company’s Sutton Bridge site.
Burgess Farms has washed and packed its potatoes at Sutton Bridge for over 25 years, following in a long and proud tradition. The first potato was packed at the Sutton Bridge site in 1964, when the Potato Marketing Board ‘Experimental Station’ was officially opened.
Today, Burgess Farms and its grower’s clear ambition is to be the UK’s leading supplier of sustainable roots, potatoes, and organic vegetables. Building on the company’s established organic heritage, the company is uniquely placed to be at the forefront of progressive regenerative farming activities across the UK.
The Sutton Bridge potato team is absolutely focused upon providing its strategic customer partners with a full range of high quality, innovative and seasonal fresh produce, which are available in most pack sizes, formats and packaging materials, ranging from a 200g individual portion pack to a 25kg sack, and above.
In 2024 Burgess Farms identified that there was an opportunity to improve their current product washing and product grading capabilities and began looking for viable options to continue to positively drive their business forward, from an efficiency but also equally importantly from a customer product quality perspective.
David Booth, Engineering Manager at Burgess Farm:
"The senior management team were aware that the line could be significantly improved with investment in new technologies and were keen to take further advantage of optical sorting and grading. They asked me to specify a washing and packing line with a Newtec Celox at its centre."
With the specification agreed, David went to the market, undertaking his due diligence which included a visit to Haith’s factory and some of the company’s customers to see to their potato washing and packing lines in operation.
David Booth:
"I’ve been in the industry for a long time and have worked with Haith previously, but that didn’t mean we didn’t do our research, The size of the investment was considerable, and we wanted to ensure we got the best value for money and that the new line would offer us the capability, reliability, and longevity we were looking for. Haith has a reputation for building high-quality machines that last, and that is what they’ve delivered."
The new line starts with a RotaTip TE. The award-winning box tipper is fully electrically powered and ejects the empty box upwards to reduce forklift movements. Potatoes enter the system over a web which removes any loose soil from the crop before transferring it into a SupaFlume de-stoner. The crop is then washed through a semi-submerged barrel washer which features a fully rubber pintle lined barrel and floating debris removal system.
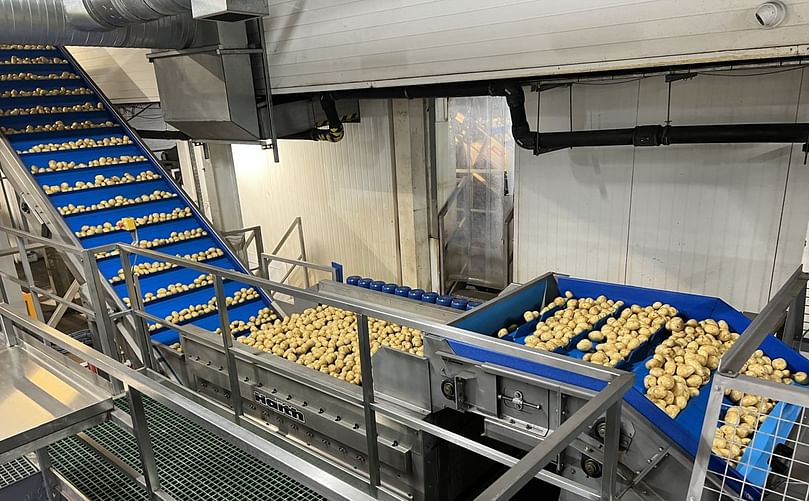
A closer look at the advanced potato processing system at Burgess Farms, featuring Haith’s innovative washing, drying, and sorting equipment, designed to optimize quality and sustainability.
The potatoes are then dried by passing over a Direct-Drive Sponge Roller Dryer. Each roller is driven directly by a shaft mounted drive which significantly reduces maintenance costs compared to the traditional chain driven machines. Two pintle lined rubber infeed rollers aid dewatering & debris removal.
Once dried, a Newtec Celox P-DUAL-UHD Camera sorts the potatoes by size, shape, and quality, identifying fresh damage, black spot, dry cuts, grey damage, green and rot in a single-stage process. The Celox allows up to sixteen categories to be selected for grading and sorting and will feed four, eight or 12 lanes depending on capacity. In this setting, Burgess Farm asked for each lane installed to feature a Haith VertiFill Pro box filler and weigh platform scales with weight indicator.
Once commissioned, David oversaw the installation of CCTV along the line, allowing the single operator to see and control every element of the line from his workstation, even including the door on the washer.
Mike Scott, Managing Director - Potatoes at Burgess Farms:
"As our high quality potato business continues to expand at Sutton Bridge, it was essential that this project delivered not only increased efficiencies but also enhanced operational flexibility and accuracy that further supports our potato quality culture at the Sutton Bridge site."
Rob Highfield, Sales Manager at Haith:
"We are always thrilled when we receive positive feedback from people who we have only just started to work with. Haith prides itself on developing long-term relationships with its customers and we have undertaken lots of repeat projects over the years. We are very pleased and grateful to Burgess Farms for putting their trust in us and I certainly hope that this new line will be the first of many projects that we deliver for them."
For more information about Haith and its vegetable handling equipment, including single machines, complete lines, and turnkey projects, visit Haith's official website. To learn more about Burgess Farms, visit their official site.