Egyptian snack leader Future Foods sets up pretzel production using tna equipment and expertise.
tna helps Egyptian pretzel manufacturer Future Foods to set up efficient processing and packaging line
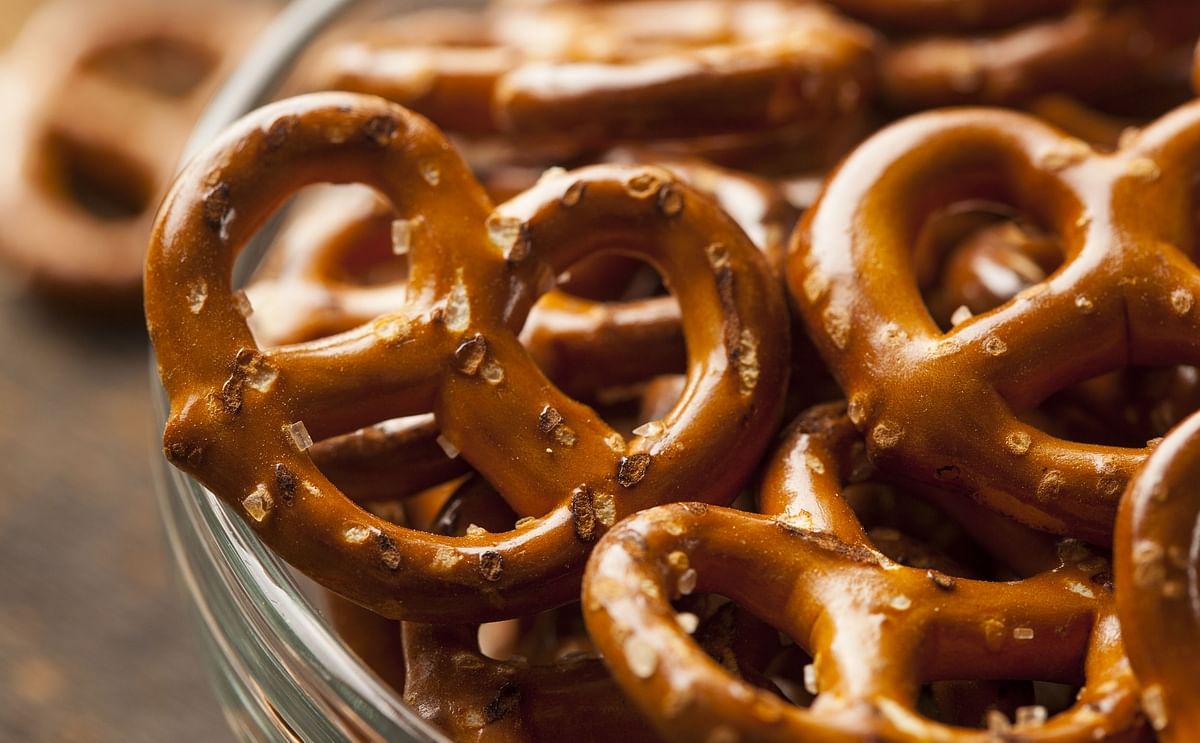
Egyptian snack manufacturer, Future Foods, has successfully launched a new pretzel range after collaborating with tna, a leading solutions provider in the food processing and packaging industry, to successfully install a seasoning, processing and packaging line.
This launch has helped Future Foods achieve 100% productivity at high speeds of up to 165 bags per minute (BPM).
Founded in 2016, in Giza, Egypt, Future Foods prides itself on bringing new and innovative products to the market. With pretzels being the fastest growing segment in the savoury snacks category and expected to achieve a CAGR of 5.8% during 2016–2020[1], the company decided to invest in a high-quality pretzel range that delivers a healthy, guilt-free snacking experience, to its consumers.
To maximise the opportunities this flourishing sector offers, Future Foods required equipment to optimise seasoning application, capitalise on packaging efficiency and minimise waste to ensure the successful launch of its new range.
Precise seasoning control
Gaining consumer acceptance at the very first bite is vital when launching any new product. Future Foods needed to feel confident that its new product range would meet consumer expectations to ensure repeat purchase and gain a foothold in the market.
In addition, application accuracy was a key consideration for the snack manufacturer. Applying an incorrect level of seasoning can have a significant impact on both input costs in terms of raw materials and wastage costs from rejected products that are either over- or under-seasoned.
Opting for seasoning technology featuring a responsive variable mass seasoning mechanism with dynamic vibratory weigher, the tna intelli-flav OMS 5, Future Foods can precisely control seasoning application within the drum.
This enables an accurate, proportional amount of seasoning to be evenly applied to the product for consistent coverage and flavour dispersion, meeting the need for a high-quality, evenly seasoned end-product.
George Soussou, Vice-Chairman & Operations Director at Future Foods:
“As we produce a delicate product that is new to the market, we had to make sure we deliver a consistently seasoned, great tasting product to appeal to the consumer. tna helped us efficiently spray our seasoning powders with zero waste.”Further performance benefits are achieved through the enhanced position of the scarfplate on the tna intelli-flav OMS 5 infeed. Mounted to the edge of the drum, the scarf better directs the product into the spraying and flavouring area, providing an even amount of seasoning on each pretzel.
“This is ultimately why our snacks taste better than those of the competition. With the new seasoning system our powder consumption never exceeds 5%.”
Additionally, the scalloped infeed conveyor design allows more product to enter the seasoning drum, while also helping to control product direction for greater seasoning accuracy and reduced waste. This helped Future Foods achieve cost savings and increase profitability.
Smooth product transfer
When it came to choosing a distribution system for the new range, minimising product breakage and ease of cleaning were critical factors. From the start, Future Foods knew reducing the risk of potential product damage or loss of flavour was key for success. For this reason, the company opted for equipment that aided a gentle transfer.
The chosen distribution system, the tna roflo HM 3 horizontal motion conveyor, ensures a smooth product transfer through the line, while keeping product damages to a minimum, as there is no vertical lifting or bouncing of the product and no flavour build-up in the pan.
Unlike traditional conveyors that use mechanical gates, the patented 'true' gateless design of the tna roflo HM 3 helps protect the pretzels from damage with servo controlled 'virtual gates' that simply open up a gap between the pans where the product is discharged.
The risk of any potential damage to the product is significantly reduced and practically eliminates any loss of flavour. With the installation of several tna systems, including the tna roflo HM 3 and tna intelli-flav OMS 5, breakage level from seasoning to packaging is less than 0.5%.
tna’s roflo conveyors also offer significant maintenance benefits due to their overall mechanical simplicity, resulting in greater equipment reliability and therefore lower total cost of ownership over the lifespan of the system.
The tna roflo HM is the only conveyor in the world that uses a single linear servo motor.
One of the main benefits of this design is that there is almost zero maintenance as there are no big drives, shafts, belts or pulleys.
High-speed, efficient packaging
Offering a new range of pretzels in 16g, 35g and 100g pillow-style bags, Future Foods was looking for a system that would deliver consistently high speeds. Beyond this, quick changeovers to maximise throughput and reduce downtime were also a necessity.
With the installation of two tna robag FX 3ci vertical form, fill and seal (VFFS) packaging systems, the production line offers flexibility and improved performance in a compact, easy-to-clean set up. With their rotary double jaws, the new baggers were quickly able to deliver speeds of up to 165 BMP, while quick-release formers ensure that Future Foods is able to change between bag sizes in less than three minutes.
George Soussou:
“The new packaging systems are very reliable, achieving 100% productivity at very high speeds. What’s more, with less than 1% film waste, we’re able to achieve significant cost savings.”One partner, multiple solutions
“Adding to that, the user-friendliness of the machine and the ease of changeover between bag sizes keeps downtime to a minimum, further increasing our production efficiencies.”
“It’s not just the products tna offers. The tna team was always on hand to support and train our team members throughout the entire commissioning, installation and start-up phase.”
“That way, tna ensured that our new equipment always operates at its maximum level of performance.”
“For us, tna is much more than just a supplier, as a true partner, its turnkey solutions make production line equipment virtually carefree and put any company on the road to success.”
Soussou:
“As a new company it was essential for Future Foods to work with a reliable partner that could ensure a smooth start up, achieve the line efficiencies we were looking for and deliver the best return on investment in the long term.”With over 140 products, tna offers one of the widest equipment portfolios for the snack industry. This includes fryers, conveyors, seasoning and coating systems to metal detectors, weighing and inserting and labelling solutions, bagging and case packing equipment, making it the only global supplier that can deliver equipment for the entire snack production line.