As the demand for food continues to rise in line with a growing global population, optical sorting is no longer seen as ‘optional’ but, rather, as the industry benchmark for maintaining operational efficiency, product quality and food safety.
Getting to the Root of Food Safety in the Potato Industry
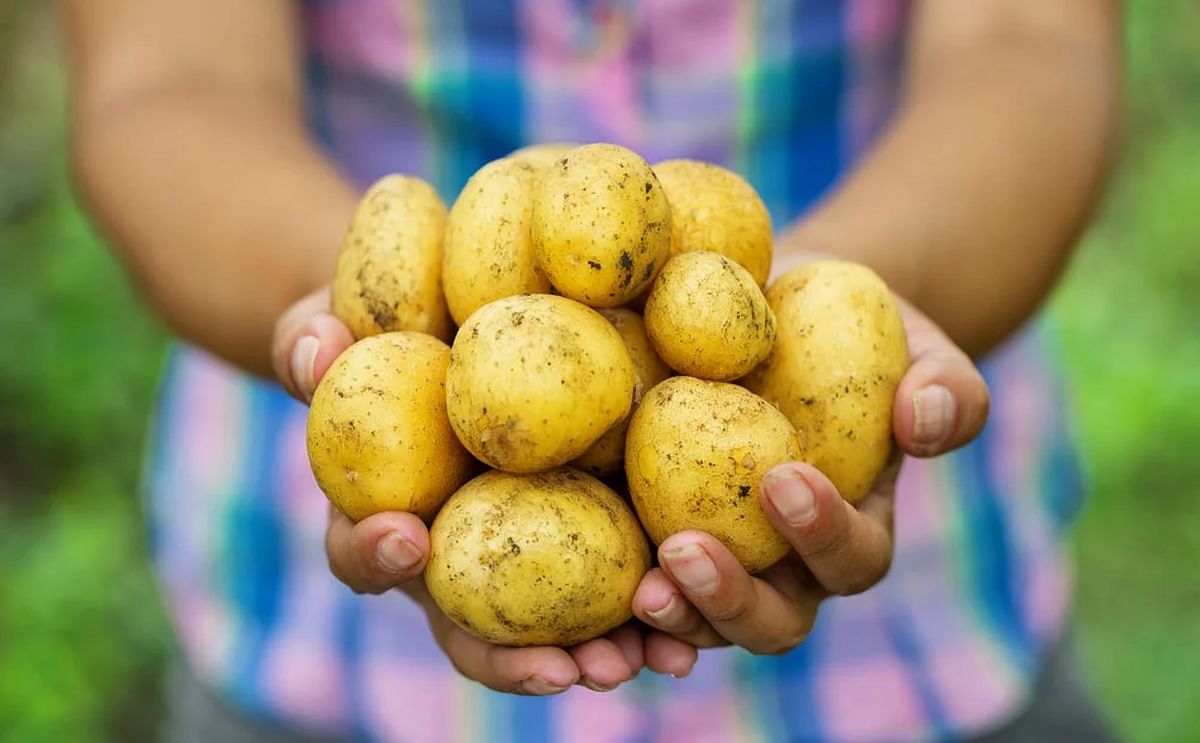
From sticks and stones to plastic bottles and golf balls, potato farmers encounter an ever-increasing spectrum of hazardous foreign material in their fields making effective sorting a critical element of the processing line.
While large foreign objects such as rodents, insects, stones, soil, wood and plastic might be easier to spot, public safety relies on food being free from microscopic contaminants and transparent items like glass that are not usually visible to the human eye.
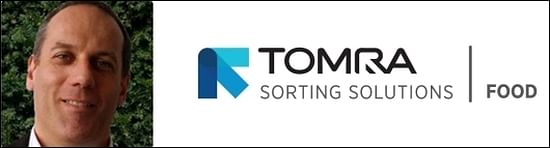
This article was written by Jeffrey Steemans, global product manager at TOMRA Sorting Food. He is based in Leuven, Belgium.
Product recalls: Something no business can afford
Product recalls set in motion a domino effect that negatively impacts every single stage of the food supply chain. They are costly in terms of business, brand and the environment – unnecessary stoppages in production result in increased energy consumption while recalled product has nowhere to go further contributing to waste in landfills.
When things go wrong, a product recall can be truly devastating for a potato manufacturer in terms of financial loss and status meaning that automated sorting is not just good for business, it’s vital.
Manual sorting: Ineffective and unavailable
While foreign materials pose a significant threat to the quality and safety of a product, manual labor also opens up the potential for human error which can result in other objects making their way into the food stream. Within the context of food safety, the limitations of manual sorting are clear however sociological factors such as rural depopulation and an increasingly educated workforce mean that farmers no longer have the same access to labor as they once did.
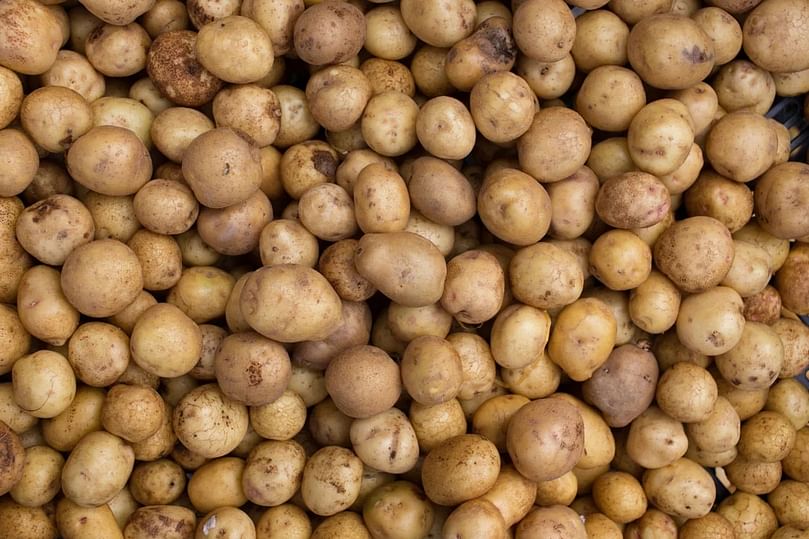
From sticks and stones to plastic bottles and golf balls, potato farmers encounter an ever-increasing spectrum of hazardous foreign material in their fields making effective sorting a critical element of the processing line.
TOMRA: Improving productivity, quality and value
As partners with some of the world’s most influential potato suppliers, we’ve developed a unique insight into some of the biggest challenges facing potato producers and processors today – the findings of which we’ve used to drive innovation that continues to deliver the world’s most advanced grading, sorting and peeling technology.
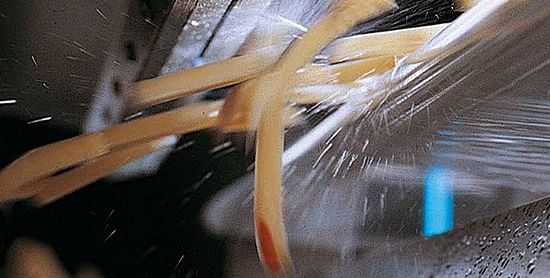
TOMRA sorting application for French Fries
Equipped with innovative technology, TOMRA’s potato sorting solutions can detect and reject product defects based on biological characteristics, shape and size, structure, colour and density while recovery sorting ensures no good product goes to waste.
Furthermore, sophisticated LED illumination and multispectral cameras facilitate the identification of very small foreign materials and contaminants, as well as abnormal solanine (greening)/chlorophyll content which can be time-consuming to inspect and remove.
Download TOMRA e-Book
From international regulatory bodies to brands, as key stakeholders continue to raise the bar for food safety across all areas of the supply chain the responsibility of delivering a quality product to spec rests with producers and processors. As global concerns over yield, food security and sustainability grow, an effective sort will ensure the minimum amount of food is wasted whilst delivering a safe, high-quality final product to customers.