Herbert Potato washer
Eighth Herbert Washer for World Leading Snack Food Manufacturers
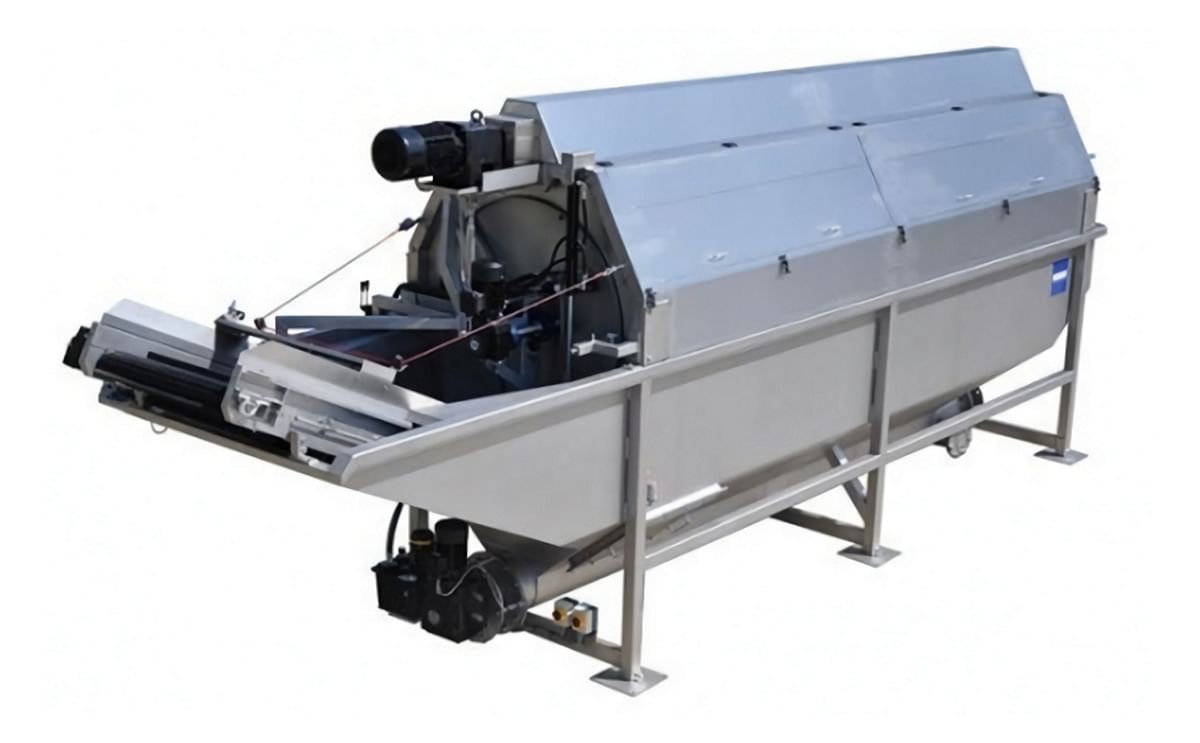
R J Herbert Engineering, the leaders in agricultural handling systems, has supplied three further potato washer systems for one of the world’s largest snack food companies. This brings the total supplied to eight in the Asian, Middle Eastern and African continents, the three most recent being supplied to Egypt and South Africa, demonstrating Herbert’s commitment to serving the global market.
Herbert manufactures an extensive range of auger based barrel washing systems with options to reduce water usage and capable of cleaning up to 50 tonnes of product per hour.
The five-metre barrel washer for this customer has to meet some of the toughest key performance indicators within the industry. These cover product tolerances, which are exceptionally tight, cleanliness of product, efficiency of de-stoning and very strict control of water usage, which has to be kept to a minimum.
The fully stainless steel construction, including the webs and auger, allows for caustic cleaning to achieve the customer’s very high food safety standards.
These bespoke washing lines feature a water weir separation system for the effective removal of stones. The integral de-stoner unit is linked to the washer tank and is designed to avoid dead spots where dirt and detritus can collect.
The automated water dumping system only uses one cubic metre per hour, and the floating object remover follows the water level to effectively take out wood and other surface debris.
Sludge washed from the potatoes sinks to the bottom of the washer and is removed from the tank by means of an auger and scraper chain. As well as keeping the water cleaner by avoiding a sludge build up, it minimises water usage and also allows washing to continue for up to 20 days before stopping for cleaning.
Glen Burt, sales engineer at Herbert Engineering, said: “The specification for these washing plants is exceptionally taxing and we have designed a number of features to meet the customer’s strict requirements for long production runs and minimal water usage. The customer has seen significant benefits as a result of the innovative solutions we have offered with the eight washing plants we have designed and built. Improved cleaning with reduced water usage alongside less maintenance and reduced downtime have been the key successes with these projects.”
After pre-delivery inspection and sign off, the systems are supplied to the customer in a freight friendly format with minimal fitting required on site.
Source: Herbert Engineering