United Kingdom based Potato Processing company M&F produced fresh cut and peeled potato products and supplied these to companies who further process these potatoes into ready meals for the UK’s major supermarkets.
UK based manufacturer of cut and peeled potato products closes shop
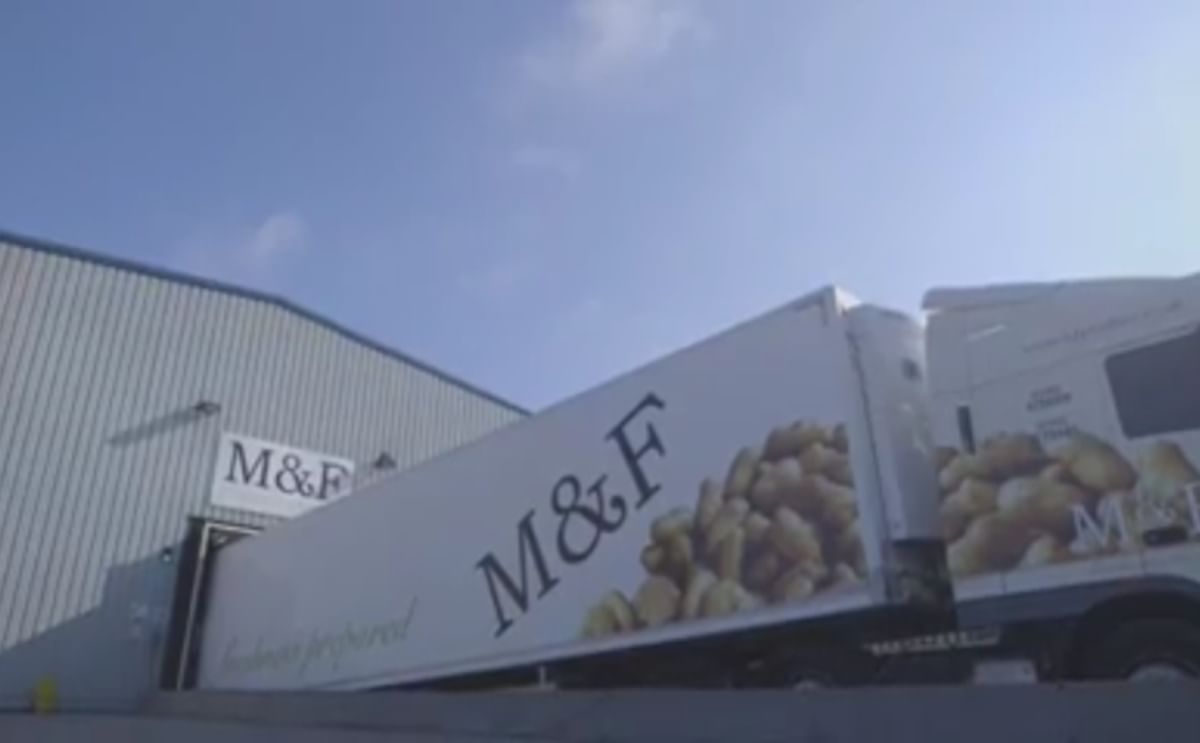
Potato Processing company M&F, a manufacturer of fresh cut and peeled potato products in the United Kingdom, has closed after losing one of its main customers.
Almost 100 staff have been made redundant following the failure of this £9m-turnover business (USD 11.2 million) which supplied its potato products to major supermarket chains.
Paul Stanley and Andrew MacKenzie of Begbies Traynor were appointed joint administrators at the request of the directors and are now looking to raise money for creditors by selling off assets.
The company’s existing factory at Plaxton Bridge Road, Woodmansey, outside Beverley, was able to process more than 100,000 tonnes a year of potatoes and other root vegetables.
The business was also planning the development of a new £4.4m anaerobic digestion plant on a site behind the plant to save hundreds of thousands of pounds in waste disposal costs, and generate an additional £400,000 of revenue.
Andrew MacKenzie of Begbies Traynor:
"The business was trading well, despite tight margins in the sector, prior to the loss of one major contract," said Andrew MacKenzie of Begbies Traynor.”
“It was clear very quickly that without the same level of revenue the business had no way to cover its costs, and unfortunately the doors had been closed on 10 March before our appointment.”
“Our early investigations concluded that without the company’s main customer, which was responsible for the majority of the revenue for the business, there was no alternative to keeping the business closed to prevent liabilities rising."
Business offered for sale
The assets of the business, which operated from leased premises, include various elements of processing machinery, several trucks and vehicles and general office equipment will be sold by auctioneer Eddisons, which has been appointed to dispose of the assets.More...
"We are hopeful that there will be interested parties who may want to operate the plant again, and will acquire the site as it is ready to go and has a readily available local workforce.”
“The potential for the waste plant, with all permissions secured, make this potentially attractive for trade buyers too."
M&F in a Tong Engineering Case Study (2015)
M&F Ltd supply processed potatoes to companies who further process the potatoes into ready meals for the UK’s major supermarkets. Handling over 100,000 tonnes of potatoes per year, the company produces high quality potatoes ranging from whole peeled to sliced, diced and chipped, and distributes them across the UK.In order to update their current processing operations, M&F Ltd required a complete potato handling facility, which Tong designed to comprise of five independent peeling lines for optimum throughput. The new facility gently handles the potatoes from receiving dirty crop in boxes to packing the processed crop ready for dispatch.
The lines start with a series of Tong box rotators at the infeed, which gently tip crop into five Tong bulk receiving hoppers, which ensure an even flow of crop into ten potato peeling machines.
Once crop is peeled, the potatoes pass through Tong stainless steel de-starch tanks with 900mm wide outfeed elevators and blue plastic modular belting to aid drainage of the crop after the de-starch treatment is complete.
Crop is then elevated onto roller inspection tables for manual inspection prior to packing. Once inspected, all crop passes through Tong SO2 dip tanks to give the potatoes an enhanced finish and prevent discolouration of the crop.
A series of metal detectors and slither removers are also incorporated within the peeling lines to ensure potatoes are in optimum condition before they are mashed, chipped, quartered, diced, sliced or roasted.
Graham Stark, Managing Director at M&F Ltd:
“Demand for processed crop continues to increase and in line with this, our peeling facilities needed some additions and upgrades to cope with the amount and variation of crop we now need to process on a daily basis. We handle between 1200 and 1800 tonnes of potatoes a week and we needed a very efficient potato processing line to handle our crop.”Simon Lee, Sales Manager at Tong Engineering:
“We have worked with Tong Engineering for a number of years and they have supplied us with grading and handling equipment that has helped to significantly improve the efficiency of our operations. That’s why, when it came to updating our peeling facilities, Tong was the natural choice for us to work with again.”
“We are very dedicated to ensuring our quality is amongst the highest in the industry, and our production plant operates to stringent health, safety and hygiene requirements. We worked very closely with Tong’s design team to ensure the new processing facilities include all the necessary processes to get a very high quality end product, whilst also allowing us to achieve several end products that meet our customers’ requirements.”
“We can now process up to 1800 tonnes of potatoes in just a week! Our whole potato handling process is safer, quicker and much more productive.”
“When M&F Ltd approached us regarding their new peeling requirements we could see that whilst they needed a significant amount of new equipment, some existing equipment could still be utilised in the new design.”Graham Stark:
“The new processing facilities have integrated both the new and existing equipment very effectively, allowing M&F Ltd to be very flexible and responsive to their customer demand. The introduction of de-starch tanks and SO2 dip tanks means the finished quality of M&F’s processed potatoes is at its optimum.”
“From design through to installation and after care, the team at Tong Engineering have worked very hard to provide us with a complete processing facility that will meet our requirements for many years to come.”
“With the new Tong lines, we are now very proud to be running one of the most efficient potato processing facilities in the UK.”