VERYX belt fed sorter by Key Technology
Key Technology Introduces VERYX Belt-Fed Digital Sorters
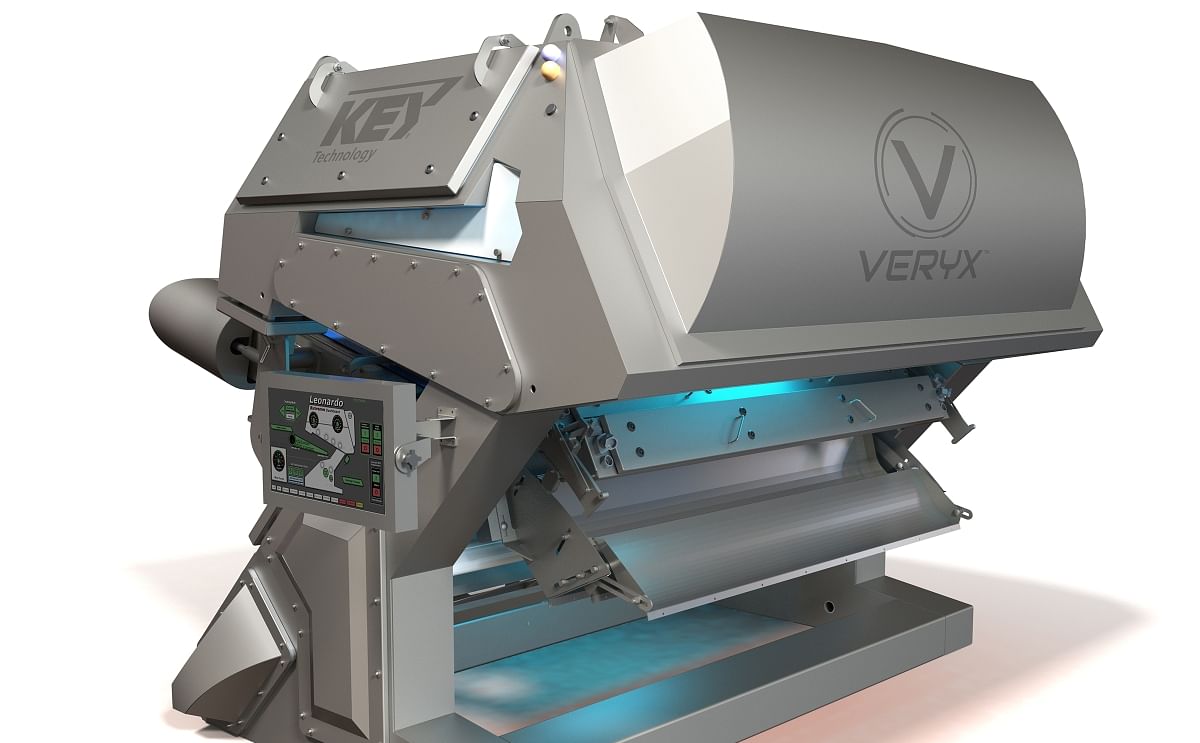
Key Technology introduces its VERYX® belt-fed digital sorters. Like the chute-fed VERYX sorters introduced in 2015, the new belt-fed VERYX sorters set new standards of performance.
With a highly innovative mechanical architecture, sustainable all-sided surface inspection, multi-sensor Pixel Fusion™, the highest resolution cameras and laser sensors available on a digital sorter and extreme ease-of-use, VERYX maximizes foreign material (FM) and defect detection and removal while virtually eliminating false rejects. As the world’s most intelligent sorter, VERYX improves product quality, increases yields and reduces the need for labor.
Marco Azzaretti, Advanced Inspection Systems Product Manager at Key Technology:
The VERYX B175 features a 1750-mm wide inspection area suited for mid- to high-capacity operations. Ideal for potato processors sorting wet or frozen strips and specialty potato products as well as food processors sorting vegetables, fruits or other products, the B175 can be configured to achieve two- or three-way sorting, as needed.
For food processors requiring all-sided surface inspection, Key can arrange the sensors to achieve full view of each object in the product stream with no blind spots. On belt-fed systems, the VERYX bottom cameras are positioned away from product splatter to ensure lower sensor windows are not obstructed by buildup over time. Eliminating this previously common performance degradation keeps bottom cameras operating at peak performance and makes VERYX the first sorter to deliver 100 percent surface inspection that is sustained throughout the production cycle.
Another industry first is Key’s patented multi-sensor Pixel Fusion. This advanced feature merges data streams from multiple cameras and lasers in relation to each image pixel. Fusing sensor data at pixel level maximizes the contrast between ‘good’ and ‘bad’ (as defined by the user), which enables the sorter to recognize and remove more subtle product defects and previously difficult-to-detect FM.
Next-generation cameras and laser sensors offer twice the resolution capability of previous generation sorters to detect and remove sub-millimeter size defects and FM. With up to 4 channels of information from cameras and up to 8 channels of information from the laser scanner, combined with advanced LED lighting that operates at the optimal frequencies in relation to each sensor, Key customizes every VERYX sorter to perfectly match each customer’s sort requirements, from basic to complex.
The new VERYX product separation/ejection system is also tailored to each application, with the distance between nozzles and the power of the valves varying for optimal management of the sort streams. This precision ejection system, together with software-driven intelligent algorithms and specialized product handling systems, nearly eliminates false rejects to increase process yields.
Leveraging richer product information and Key’s powerful new data processing architecture and intelligent software, VERYX can make new and more robust sorting decisions while easing use. Its data processing capacity enables VERYX to easily handle spikes in incoming defect loads while maintaining final product quality and low false reject rates.
Smart features such as auto-learning, self-adjustment algorithms, predictive system diagnostics, smart alarms, FMAlert™ and Sort-to-Grade™ enable VERYX to operate virtually unattended during normal production. Operator qualification requirements are reduced, making it much faster and easier for a new operator to become a proficient user of the equipment.
To further ease use and simplify training, Key collaborated with ergonomic experts to develop a new intuitive user interface (UI), shared by all VERYX sorters, which can provide different views to users of various levels, depending on their needs. Recipe-driven operation and repeatable calibration ensure customers can count on consistent performance from their VERYX sorter day in, day out, including running the same product across multiple sorters in different locations. The streamlined UI enables the sorter to run a new product or grade at the touch of a button.
VERYX features Key’s Information Analytics, a set of data acquisition and connectivity capabilities that allow users to gather a broad range of product and operational data from the sorter. The data can be made available flexibly for off-line analysis or connected to a customer’s SCADA or Manufacturing Execution System.
VERYX sorters leverage Key’s specialized product handling solutions to optimally convey and control each object through the sort process. Improved stabilization of the product creates a more consistent trajectory through the inspection and ejection zones, which ensures ultimate accuracy in sorting out every piece of FM and defective product and avoiding the inadvertent removal of good product in the process.
Designed to minimize sanitation requirements and simplify maintenance, VERYX reduces downtime and the customer’s total cost of ownership.
For more information on Key’s VERYX, visit www.theKeyStandard.com.
With a highly innovative mechanical architecture, sustainable all-sided surface inspection, multi-sensor Pixel Fusion™, the highest resolution cameras and laser sensors available on a digital sorter and extreme ease-of-use, VERYX maximizes foreign material (FM) and defect detection and removal while virtually eliminating false rejects. As the world’s most intelligent sorter, VERYX improves product quality, increases yields and reduces the need for labor.
Marco Azzaretti, Advanced Inspection Systems Product Manager at Key Technology:
“We launched our VERYX family of digital sorters last year with the C140 chute-fed system, which is achieving great results in production environments.”To address a wide variety of food products and production capacities, the VERYX family will grow to include chute-fed sorter configurations in two widths and belt-fed sorters in four widths. With a highly customizable modular design, Key tailors each system specifically around the product characteristics and production objectives of each processor with the ideal sensors, sensor positions, lighting, separation/ejection system, product handling, software and more. The system can easily be upgraded in the field with more or different cameras, lasers, BioPrint® hyperspectral sensors and other technologies, as customer requirements evolve over time.
“Now, after extensive in-field testing, we’re introducing the first belt-fed VERYX – the B175 model – to begin shipping in November 2016.”
“Our next-generation VERYX sorters achieve more accurate discrimination – they detect additional kinds of defects and smaller defects at the same time they sacrifice almost no good product to the reject stream.”
“More intelligent automated decision-making minimizes the need for operator interaction and helps maintain optimal sorting performance.”
The VERYX B175 features a 1750-mm wide inspection area suited for mid- to high-capacity operations. Ideal for potato processors sorting wet or frozen strips and specialty potato products as well as food processors sorting vegetables, fruits or other products, the B175 can be configured to achieve two- or three-way sorting, as needed.
For food processors requiring all-sided surface inspection, Key can arrange the sensors to achieve full view of each object in the product stream with no blind spots. On belt-fed systems, the VERYX bottom cameras are positioned away from product splatter to ensure lower sensor windows are not obstructed by buildup over time. Eliminating this previously common performance degradation keeps bottom cameras operating at peak performance and makes VERYX the first sorter to deliver 100 percent surface inspection that is sustained throughout the production cycle.
Another industry first is Key’s patented multi-sensor Pixel Fusion. This advanced feature merges data streams from multiple cameras and lasers in relation to each image pixel. Fusing sensor data at pixel level maximizes the contrast between ‘good’ and ‘bad’ (as defined by the user), which enables the sorter to recognize and remove more subtle product defects and previously difficult-to-detect FM.
Next-generation cameras and laser sensors offer twice the resolution capability of previous generation sorters to detect and remove sub-millimeter size defects and FM. With up to 4 channels of information from cameras and up to 8 channels of information from the laser scanner, combined with advanced LED lighting that operates at the optimal frequencies in relation to each sensor, Key customizes every VERYX sorter to perfectly match each customer’s sort requirements, from basic to complex.
The new VERYX product separation/ejection system is also tailored to each application, with the distance between nozzles and the power of the valves varying for optimal management of the sort streams. This precision ejection system, together with software-driven intelligent algorithms and specialized product handling systems, nearly eliminates false rejects to increase process yields.
Leveraging richer product information and Key’s powerful new data processing architecture and intelligent software, VERYX can make new and more robust sorting decisions while easing use. Its data processing capacity enables VERYX to easily handle spikes in incoming defect loads while maintaining final product quality and low false reject rates.
Smart features such as auto-learning, self-adjustment algorithms, predictive system diagnostics, smart alarms, FMAlert™ and Sort-to-Grade™ enable VERYX to operate virtually unattended during normal production. Operator qualification requirements are reduced, making it much faster and easier for a new operator to become a proficient user of the equipment.
To further ease use and simplify training, Key collaborated with ergonomic experts to develop a new intuitive user interface (UI), shared by all VERYX sorters, which can provide different views to users of various levels, depending on their needs. Recipe-driven operation and repeatable calibration ensure customers can count on consistent performance from their VERYX sorter day in, day out, including running the same product across multiple sorters in different locations. The streamlined UI enables the sorter to run a new product or grade at the touch of a button.
VERYX features Key’s Information Analytics, a set of data acquisition and connectivity capabilities that allow users to gather a broad range of product and operational data from the sorter. The data can be made available flexibly for off-line analysis or connected to a customer’s SCADA or Manufacturing Execution System.
VERYX sorters leverage Key’s specialized product handling solutions to optimally convey and control each object through the sort process. Improved stabilization of the product creates a more consistent trajectory through the inspection and ejection zones, which ensures ultimate accuracy in sorting out every piece of FM and defective product and avoiding the inadvertent removal of good product in the process.
Designed to minimize sanitation requirements and simplify maintenance, VERYX reduces downtime and the customer’s total cost of ownership.
For more information on Key’s VERYX, visit www.theKeyStandard.com.
Like to receive news like this by email? Join and Subscribe!
Join Our Telegram Channel for regular updates!
Highlighted Company
Sponsored Content
Sponsored Content
Sponsored Content
Related Events
Sponsored Content
Sponsored Content