Bühler AeroDry dryer (Courtesy: Bühler)
Bühler strives for 20% higher energy efficiency by 2020
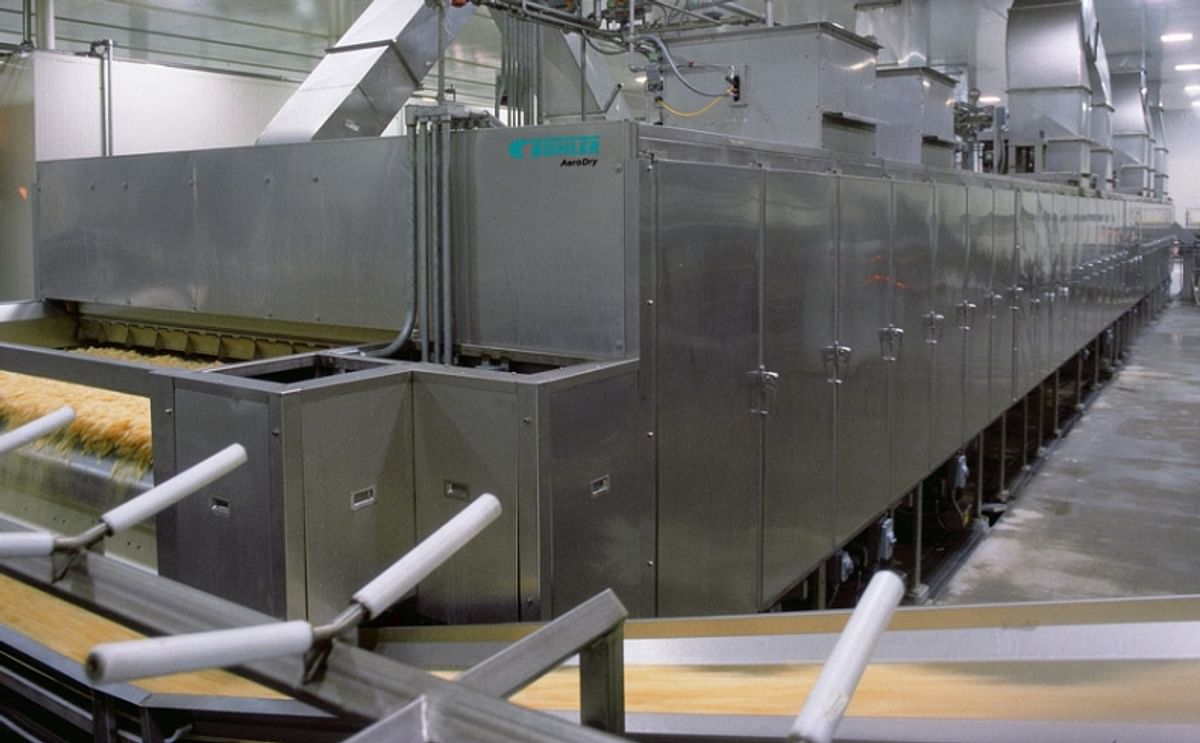
Energy efficiency is a top priority for equipment manufacturer Bühler, combining environmental and economic advantages. Driven by recent successes in this field, Bühler has set its target to reduce the energy requirement in our core processes by another 20% by 2020.
During the Bühler Networking Days that will be held in Uzwil at the end of August, Bühler will present its current solutions and discuss them together with distinguished experts such as ETH Zurich President Lino Guzzella.
Industrial processing of foods and engineering materials is often associated with high energy requirements. Whether it be energy efficient processing solutions or machines for customers, or technologies for manufacturing batteries, lightweight vehicle parts or coated architectural glass: Bühler actively engages in increasing energy efficiency and reducing carbon emissions.
Products such as feed pellets, breakfast cereals, or pasta are processed with a certain moisture content, but must in the end be completely dried again to be fit for storage. And the energy costs in large aluminum die casting foundries may easily add up to several million francs a year.
Improving energy efficiency while protecting the environment
Bühler has already made great strides in the field of energy efficiency with its process solutions, plant and equipment.
Ian Roberts, Chief Technology Officer at Bühler:
“This allows us at one and the same time to increase the energy efficiency of our products while also contributing to the protection of the environment.”During the last few years, Bühler has developed processes and technologies that significantly cut energy consumption. With these, Bühler’s customers need for example 40% less heat for the drying of pasta and 50% less electrical power for a feed mill.
Roberts:
“Despite these successes, we are far from having reached our final goal yet. Our target is to reduce the energy requirement in our core processes by another 20% by 2020, thereby reducing the amount of energy our customers are consuming.”But there is no panacea for this. It is the result of a multitude of different measures and fine-tuning steps at different levels. One core aspect is productivity, for example the reduction of cycle times in industrial production processes. If an engine block can be die cast within 90 seconds instead of 120, this will cut the energy requirement per unit significantly.
The greatest energy savings can be achieved by a correct design of production processes, in which the process is matched as closely as possible to the raw material and the end product.
Roberts:
“Bühler has seasoned specialists who are past masters at designing processes, for example in grinding, extrusion, die casting, or coating.”. It is therefore not surprising that it is precisely this application and process expertise that is one of the core competitive differentiation features of the Uzwil-based technology group.
Retrofit services: helping customers increase their energy efficiency
Thus, Bühler is stepping up its efforts to offer its customers optimal production plant designs in terms of energy efficiency beside other performance parameters.
Roberts explains:
“We take detailed measurements, give integral consideration to – say – die casting and grinding processes, and show our customers the various potential optimizations that exist.”Efficient hydraulic and drive concepts and new control technology enable up to 20% energy to be saved. In the past year, these services – which are offered under the brand name “Retrofit” – allowed Bühler to grow vigorously in the grain milling industry.
Close collaboration for new approaches to higher energy efficiency
In order to find new solutions in the medium and long terms, Bühler is collaborating closely with partners in industry and academia, for example the Swiss Institute of Technology ETH in Zurich.
Moreover, at the end of last year, Bühler launched a broadly based competition called “Energy Challenge“ in order to develop new approaches to higher energy efficiency together with researchers from top universities.
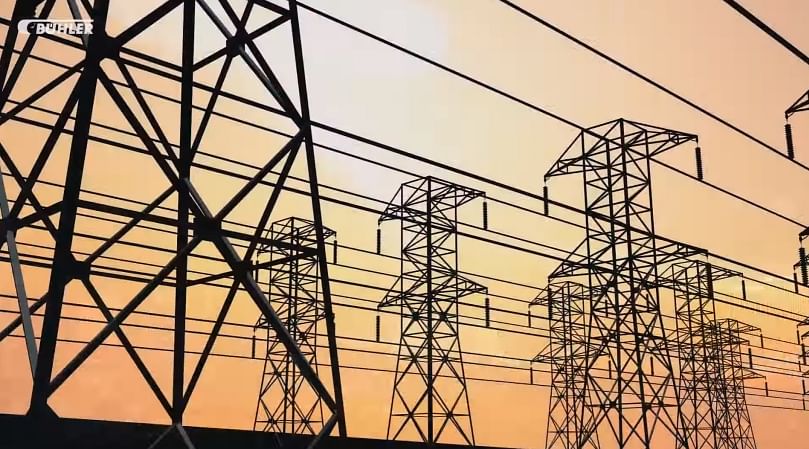
Presentation of the "Energy Challenge" competition held by Bühler in 2015
“Industry should use the energy topic as a catalyst to further improve production processes and product designs.”