Key Technology introduces VERYX® digital sorters for potato strips and specialty potato products. Featuring an innovative mechanical architecture, sustainable all-sided surface inspection, unique multi-sensor Pixel Fusion™, the highest resolution cameras and laser sensors on a digital sorter, intelligent ejection system and extreme ease-of-use, VERYX significantly improves detection performance and sorting accuracy. Ideal for wet and frozen french fries and specialty potato products,
VERYX sorters maximize foreign material (FM) and defect removal to enhance product quality while virtually eliminating false rejects to ensure maximum yield.
- All Products
- Processing Equipment
- VERYX Digital Sorting...
- All Products
- Processing Equipment
- VERYX Digital Sorting...
VERYX Digital Sorting Platform
Description
Featuring a customizable modular platform, Key tailors each VERYX system with the ideal sensors, sensor positions, lighting, separation/ejection system, product handling and software for each customer application. If future needs change, the sorter can easily be upgraded in the field with more sensors or different sensor types.
Ideal for wet potato products, VERYX offers in-air inspection and the ability to view all sides of the product to maximize defect detection and removal. Compared to on-belt sorters in which belt sanitation issues can interfere with sensor detection, VERYX in-air inspection ensures perfect inspection consistency. All-sided surface inspection with no blind spots is sustained throughout the production cycle, because the all-new VERYX design architecture positions sensor surfaces, light sources and backgrounds strategically away from product splatter and contamination zones.
For sorting frozen potato products prior to packaging, Key’s advanced Pixel Fusion detection module provides the highest level of contrast and clear separation between good product, defects and FM. Pixel Fusion synchronizes and combines channel input from multiple camera and laser sensors at the pixel level. Digital information from this unique inspection technique allows VERYX to reliably sort even difficult-to-detect defects and FM such as glass, metal, rubber, paperboard, foam and plastics of different colors.
Configurable in four different widths, VERYX sorters satisfy a wide range of capacity requirements, including extremely high throughputs on the 2.1-meter wide belt model, the highest capacity digital sorter on the market.
Marco Azzaretti, Advanced Inspection Systems Product Manager at Key:
“Our VERYX family of sorters introduces many state-of-the-art features and advanced functionality. After two years of extensive field testing, covering both wet and frozen sorting at potato processing plants in North America and Europe, we’ve proven that VERYX delivers new standards of performance.”
“With more than 40 years of experience in the potato processing industry, we offer our expertise as well as equipment. In addition to our next-gen VERYX sorters, specialized conveyors and a range of other potato processing systems, we provide engineering integration services that tie it all together into a complete solution.”
With Key’s powerful Sort-to-Grade™ software for potato strips, VERYX can automatically perform length grading and optimize defect removal to deliver the desired product grade while minimizing good product loss to increase yields. Accurately profiling the dimension of each strip and managing to a target length profile electronically means traditional mechanical length graders are no longer needed on the line. By eliminating mechanical length graders, VERYX reduces operating costs and sanitation requirements, frees up floor space and minimizes the risk of FM introduction. Production flexibility is maximized because length profiling criteria are easily managed and adjusted on the sorter’s intuitive user interface (UI).
VERYX is the world’s most intelligent sorter, including smart features such as auto-learning, self-adjustment algorithms, predictive system diagnostics, smart alarms, FMAlert™ and Sort-to-Grade, which enable it to adapt to normal changes in the product and environment without operator intervention. As result, VERYX can operate virtually unattended during normal production.
To further ease use and simplify operator training, Key developed an intuitive new UI, which provides different views to users of various levels, depending on their needs. Recipe-driven operation and repeatable calibration ensure customers can count on consistent performance from their VERYX sorter day in, day out, including running the same product across multiple sorters in different locations. For customers running multiple product types on the same system, the ergonomic VERYX UI enables the sorter to run a new product or grade at the touch of a button. Operator qualification requirements are reduced, making it much faster and easier for a minimally-skilled operator to become a proficient user of the equipment.
VERYX features Key’s Information Analytics, a set of data acquisition and connectivity capabilities that allow users to gather a broad range of product and operational data from the sorter. Data can be shared for off-line analysis or exchanged directly with a customer’s SCADA, Manufacturing Execution System or PLC network.
VERYX sorters leverage Key’s specialized product handling solutions to optimally convey and control each object through the sort process. Improved stabilization of the product creates a more consistent trajectory through the inspection and ejection zones, which ensures ultimate accuracy in sorting out every piece of FM and defective product while avoiding the inadvertent removal of good product in the process.
Designed to minimize sanitation requirements and simplify maintenance, VERYX reduces downtime and the customer’s total cost of ownership.
Key manufactures VERYX in the U.S. and Europe to support customers worldwide.
For more information on Key’s VERYX, visit www.key.net/products/veryx
Manufacturer
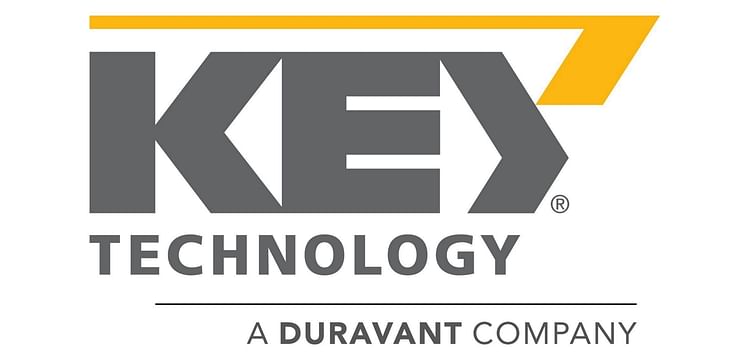
Key Technology
Key's potato processing equipment includes optical inspection systems, laser sorters, sizing, grading, and packaging conveyors, and revolutionary Automatic Defect Removal (ADR®) systems. Our extensive line of technology helps operations worldwide meet quality, safety, and capacity demands every day.
Product Group
More Products
News related to this product
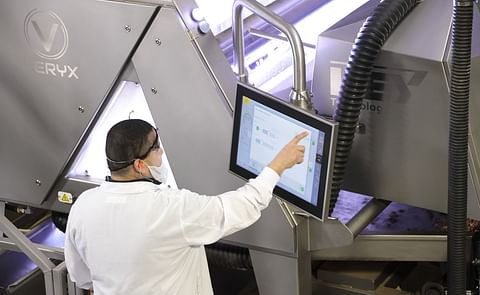
Key Technology Introduces RemoteMD® 2.0 for Optical Sorters
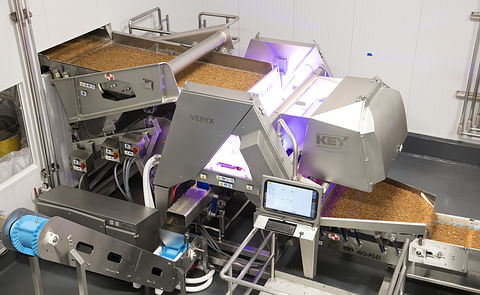
Key Technology Presents World-Class Food Processing and Packaging Systems at Interpack
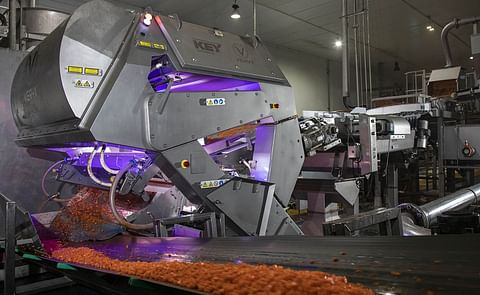
Antarctic Foods Relies on VERYX Digital Sorters to Maximize Production Efficiency and Vegetable Product Quality
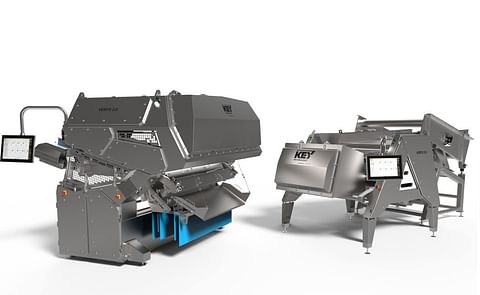