The 3D layout of the installation, showing the buffer area where cases are accumulated before palletization.
End-of-line automation: Burts Snacks Take the 'Multi-line' Decision
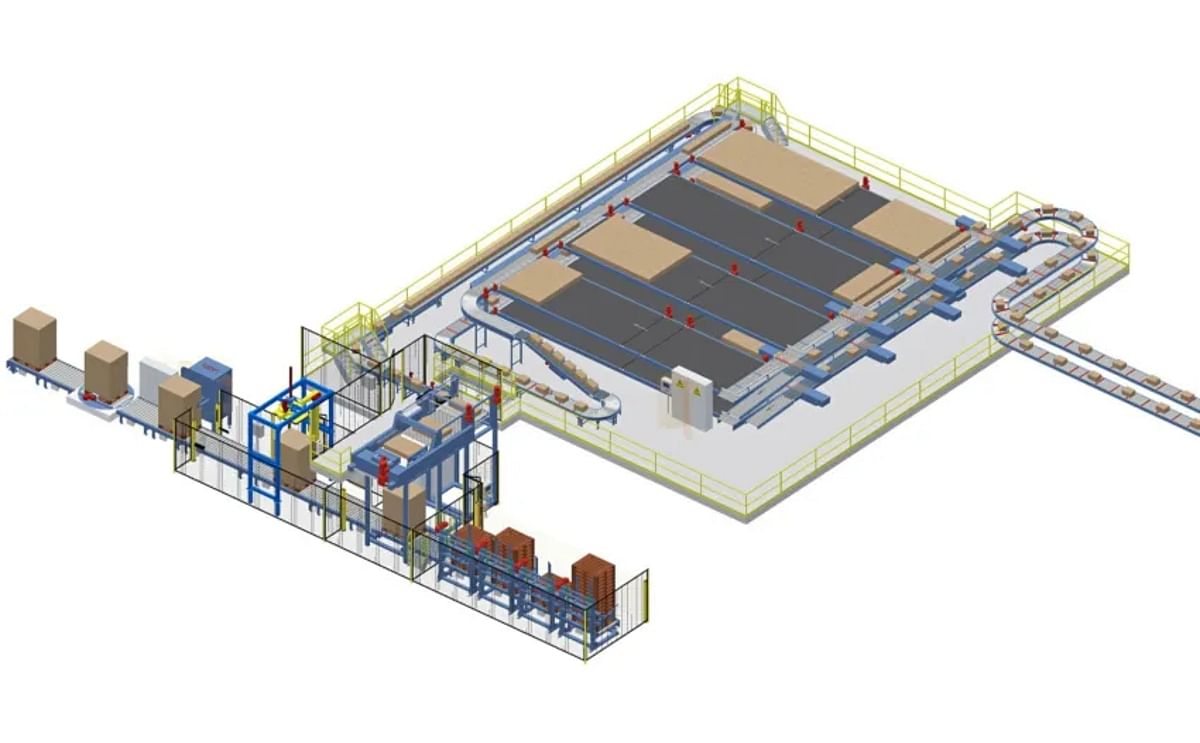
Premium Snacks manufacturer in the United Kingdom, Burts Snacks Ltd, completed one of their single largest investments, with the installation of a complete end of line pack handling and palletising solution from Scott.
Producing a wide range of bag sizes and multipacks, in a diverse range of regular cases, display packs and SRP cases, Burts needed to increase individual line efficiencies, reduce manual handling, reduce extensive internal pallet movements and increase pallet stack quality through the supply chain.
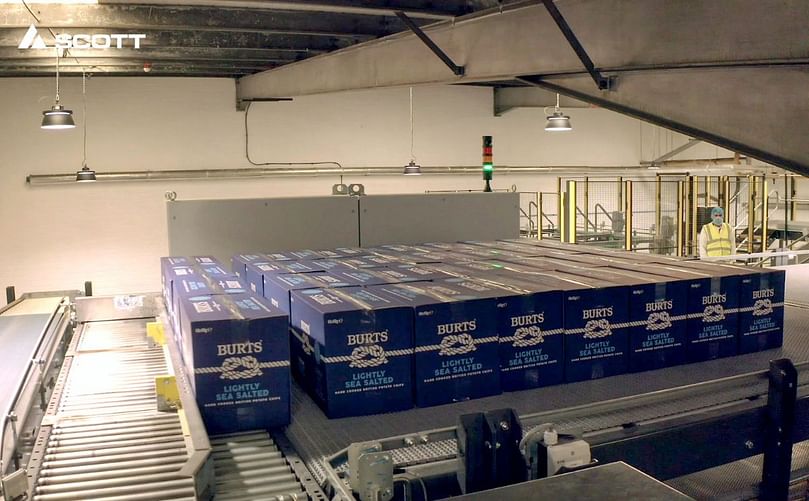
Scott Automation Palletising Solutions
Stuart Watkins, Operations Manager of Burts Snacks:
"After many months of careful consideration, looking at robots and layer solutions, we felt the Scott offering gave us what we needed..."
"Once the final design was completed, the Burts Snacks’ on-site team worked closely and collaboratively with the Scott project and installation team."
"The successful end result was achieved with the complete buy in from the Burts Snacks’ operational team with a significant up lift in output and reduced supermarket returns."
"And with the huge operational changes required this year, the decision to install Scott’s Multi-line was hugely beneficial!"
The Project objective was to provide a palletising solution for the rapidly filling Roborough site, with a phased installation, without disrupting production.
The solution needed to enable access to each line for operators and packaging materials whilst minimising transport distance of unwrapped pallet loads.
Nine production lines producing up to 2,400 cases per hour are linked to the system with future expansion for 2 more lines foreseen and as a multi-customer producer, the solution handles multiple case sizes, empty pallet types, and various stacking patterns delivering an output of up to 40 pallets per hour.
Cases are collected from each production line, merged onto high-level transport conveyors and delivered to a central sortation, buffering and palletisation area based on the Scott Multi-line principle.
The correct empty pallet is dispensed for the high-level Scott palletiser to build each SKU at 4 layers per minute.
Completed pallet stacks are then carefully wrapped, labelled and delivered to the on-site warehouse.
The system was installed in a small area at the back of our empty pallet and packaging store, with all the sortation and buffering at a high level on a mezzanine floor.
Maxine Stringer, Group Technical Manager of Burts Snacks:
"From my perspective the food safe approach to installation facilitated a seamless install and the ease of maintenance from a hygiene perspective post-install is excellent."