Mark Willcox, Technical Director at Branston inspecting the new washer, the 1000th vegetable washer sold by the Haith Group
Branston Ltd buys Haith’s 1000th vegetable washer to clean potatoes
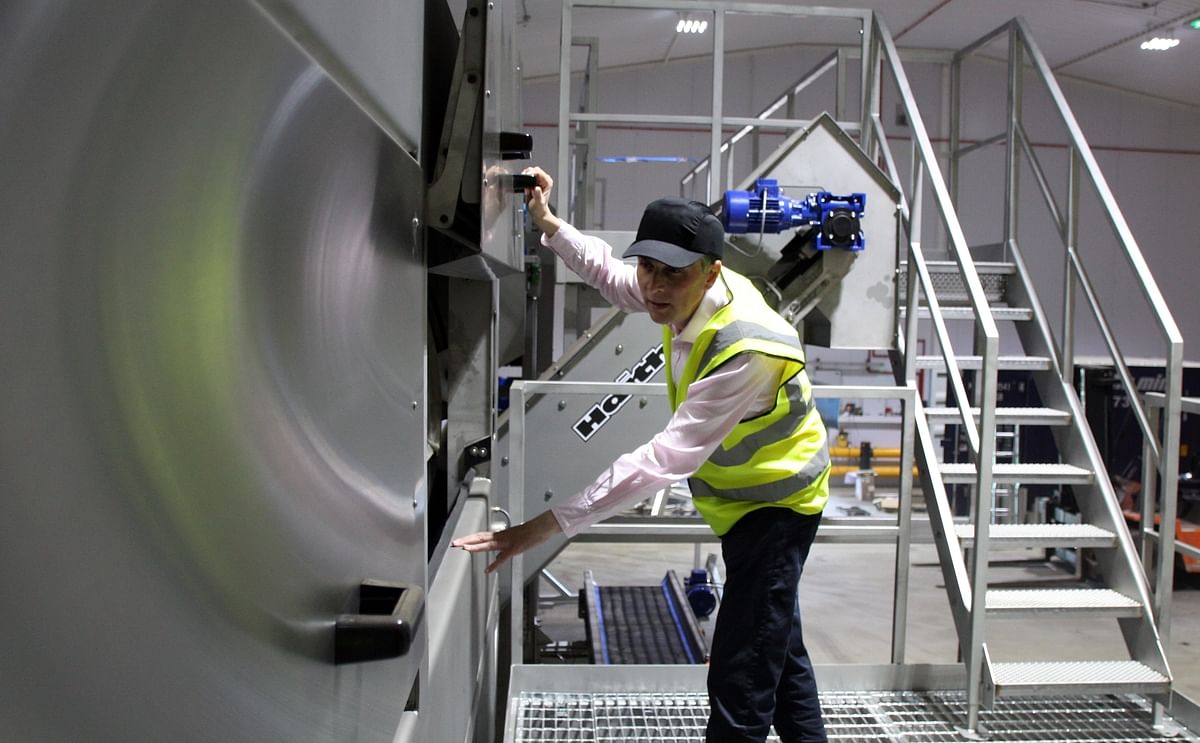
Haith group is celebrating selling its 1000th vegetable washer! The milestone machine, one of a pair, rolled off the production line at the end of last month destined for Branston Ltd.
As well as being the thousandth vegetable washer to be sold since Haith invented the modern barrel washer in 1961, Branston’s machine is the eighth Haith Supa-Wash to be sold since it was introduced in March 2018.
Haith’s barrel washers have come a long way since Mr Haith Snr introduced the first spokeless steel washing barrel in the early ‘60s.
In the 1970s Haith’s innovation produced the brush roller bed, which was superseded in the ‘80s by the Hydro Flow washer, with its unique pump which moved the produce from the barrel.
At the beginning of this century, Haith launched the Self Clean washer, a machine that is still operating in food packers and processor factories across the world, thanks to its robust and innovative design features, such as an electrically operated radial door, direct barrel drive, thick steel slotted barrel and full pintle lining.
When launched, the Haith Self Clean washer was significantly ahead of its competition, with most other manufacturers relying on less advanced features, such as hydraulic doors, chain driven barrels and thin punched barrels.
The latest Supa-Wash is a significant step forward in another way too says Nigel Haith, managing director of Haith Group.
Nigel Haith:
Mark Willcox, Technical Director at Branston:
A CIP cleaning system can be supplied as an option which allows automatic internal sanitation of the washer, this is controlled from the HMI and can easily be done at the end of each shift, another important factor in reducing bacteria and improving vegetable shelf life.
For further information about Haith and its range of vegetable handling equipment, please visit www.haith.co.uk
As well as being the thousandth vegetable washer to be sold since Haith invented the modern barrel washer in 1961, Branston’s machine is the eighth Haith Supa-Wash to be sold since it was introduced in March 2018.
Haith’s barrel washers have come a long way since Mr Haith Snr introduced the first spokeless steel washing barrel in the early ‘60s.
In the 1970s Haith’s innovation produced the brush roller bed, which was superseded in the ‘80s by the Hydro Flow washer, with its unique pump which moved the produce from the barrel.
At the beginning of this century, Haith launched the Self Clean washer, a machine that is still operating in food packers and processor factories across the world, thanks to its robust and innovative design features, such as an electrically operated radial door, direct barrel drive, thick steel slotted barrel and full pintle lining.
When launched, the Haith Self Clean washer was significantly ahead of its competition, with most other manufacturers relying on less advanced features, such as hydraulic doors, chain driven barrels and thin punched barrels.
The latest Supa-Wash is a significant step forward in another way too says Nigel Haith, managing director of Haith Group.
Nigel Haith:
“Our new washer is the result of months of development work.”Branston Ltd will use the record-setting machine at its Lincoln factory. The company, which handles 350,000 tonnes of potatoes each year, is no stranger to Haith’s high-quality machines, using them in its fresh and prepared factories in Lincolnshire, Somerset and Scotland.
“It is packed with technologically advanced features, such as cooper split bearings on the top shaft for easy maintenance, and on the main drive shaft, a SEW energy efficient shaft mounted barrel drive and externally mounted stainless steel bearings for longer life.”
“The machine is further enhanced by the presence of a gentle air operated vertical rising crop discharge control gate, a laser cut stainless barrel with slots or holes depending on the produce which will be washed, a full pintle rubber lining inside the barrel and HMI touch screen control with intelligent feedback. All of these features are standard.”
“We’ve also improved the way crop is discharged from the washer. With the Supa-Wash, the crop is gently encouraged out of the barrel using an elevated cone which after a final rinse deposits the crop into a separated discharge tank which houses the discharge elevator. This means the washed product leaves the washer after being fully submerged in clean water that is separate to the dirtier water found in the main tank.”
“The waste which is collected in the base tank is automatically removed by an auger and scraper elevator system alternatively you can have a series of air valves which can be controlled to dump in sequence monitoring the volume of water usage.”
Mark Willcox, Technical Director at Branston:
“The team at Haith recognised the challenges we face in terms of constantly improving our packing process.”All Haith barrel washers can be supplied as a complete system if required, with de-stoning on the in-feed and a floating waste removal unit on the out-feed of the barrel, which is ideal when the washer is incorporated into a potato processing line.
“As a result the new door-less design has further reduced the potential for damage and we’ve been delighted with the impact it’s had on the quality of product to our retail customers.”
A CIP cleaning system can be supplied as an option which allows automatic internal sanitation of the washer, this is controlled from the HMI and can easily be done at the end of each shift, another important factor in reducing bacteria and improving vegetable shelf life.
For further information about Haith and its range of vegetable handling equipment, please visit www.haith.co.uk
Like to receive news like this by email? Join and Subscribe!
NEW! Join Our BlueSky Channel for regular updates!
Highlighted Company
Sponsored Content
Sponsored Content
Sponsored Content
Sponsored Content
Sponsored Content