Newtec’s Optical Sorting Solution ideal for packers of table potatoes
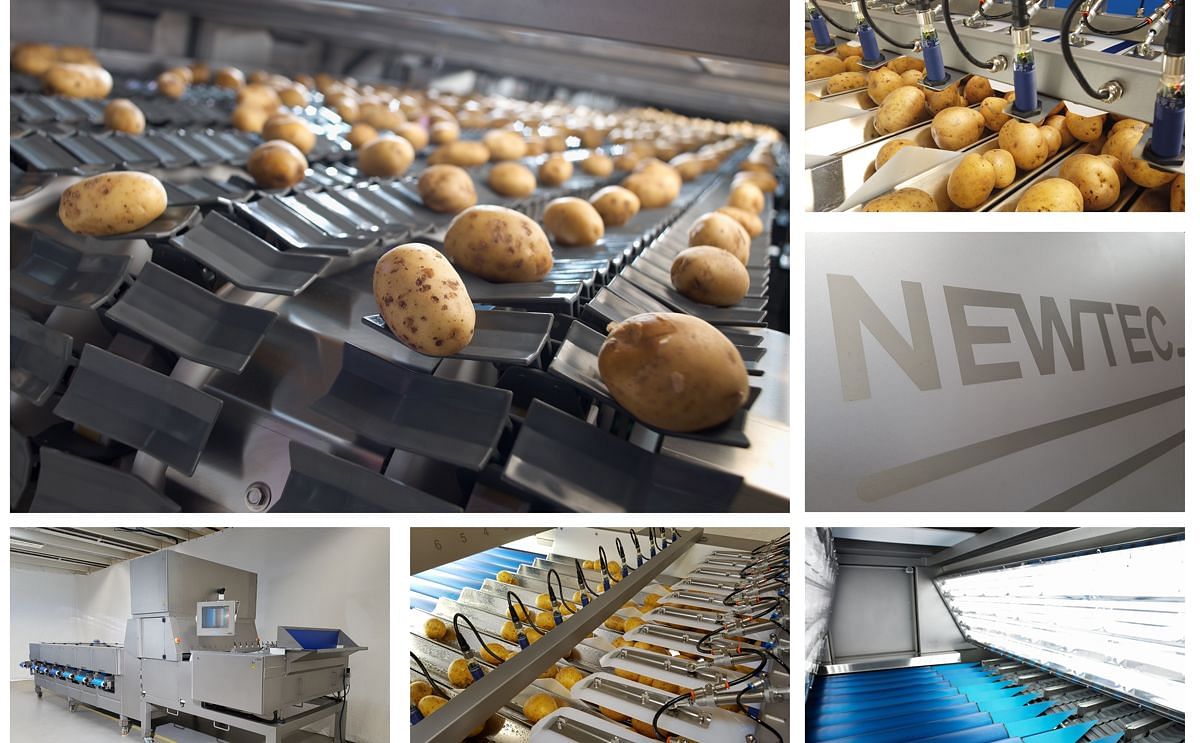
Newtec Optical sorters, here applied for potatoes to be packed for retail
Newtec’s weighing, sorting and packing solutions offer reliability and efficiency of production for customers in the food industry.
With its focus on establishing long-lasting trust with customers globally, Newtec helps companies optimise production through easy-to-use and durable weighing, sorting, and packing equipment, minimizing giveaway and turning produce into highly competitive end-products.
Making better use of the raw material
The large amount of natural variety in potatoes means there is no easily expressible reference standard for comparison. The product can vary largely in size, shape and possible defects, so an optical sorting machine designed for potatoes would need a very advanced set of abstractions and concepts that efficiently capture the essence of what normal potatoes really look like.
Furthermore, potato colours can include white, yellow, red, purple, brown and multi-coloured while dirt and loose skin can be left as residue inside the machine. With such a varied and cluttered environment, it is important that the computer vision system of a sorting machine for potatoes is robust.
Due to the number of staff required, sorting potatoes by hand is also rarely economically feasible. Manual sorting requires large amounts of space, which often needs to be tightly climate-controlled. Furthermore, rising labour costs and workforce shortages mean that filling vacancies such as potato sorting have become increasingly difficult.
Daniel Bengtson, Software Developer of Newtec Engineering:
The Newtec Optical Sorting Machine, Celox-P-UHD for potatoes uses the patented Newtec roller vibration system to achieve a complete 360⁰ scan.
Daniel Bengtson:
This means that product batches that would not be economical to manually sort can still be profitable when sorted by an optical grader.
Daniel Bengtson:
Daniel Bengtson:
How can Artificial intelligence AI help with optical sorting?
The ‘sorting algorithms’ used for optical sorting machines are generally defined by physical criteria and surface defects. For example, the criteria used by the Celox-P-UHD for potatoes include length, diameter, volume, roundness, and bad shape. Additionally, new ‘filters’ can be downloaded and installed for different defects and product types.
Daniel Bengtson:
Daniel Bengtson:
With a more nuanced quality classification of ‘bad products’, food waste can be reduced, effectively reducing the carbon footprint of a given amount of crops. Furthermore, the ability to sort product batches with a high percentage of bad products means that otherwise uneconomical product batches can still be used.
Newtec’s optical sorting machine, The Celox-P-UHD, can also collect data about products for later analysis. This data can be used to optimise future harvests, increasing overall crop yield while reducing fertiliser and chemical treatment use.
Daniel Bengtson:
Optimised conditions increase the prospect of a yield that meets the taste, size, appearance, shape and variety demands of manufacturers and supermarket chains.
Optical graders can also work efficiently in smaller and less tightly controlled environments, reducing the amount of energy expended on heating and lighting as compared to manual sorting.
Newtec is ready to deal with emerging sustainability-related developments, delivering highly modular machines that meet customer needs and always allow the operator to make the final call.
With its focus on establishing long-lasting trust with customers globally, Newtec helps companies optimise production through easy-to-use and durable weighing, sorting, and packing equipment, minimizing giveaway and turning produce into highly competitive end-products.
Making better use of the raw material
The large amount of natural variety in potatoes means there is no easily expressible reference standard for comparison. The product can vary largely in size, shape and possible defects, so an optical sorting machine designed for potatoes would need a very advanced set of abstractions and concepts that efficiently capture the essence of what normal potatoes really look like.
Furthermore, potato colours can include white, yellow, red, purple, brown and multi-coloured while dirt and loose skin can be left as residue inside the machine. With such a varied and cluttered environment, it is important that the computer vision system of a sorting machine for potatoes is robust.
Due to the number of staff required, sorting potatoes by hand is also rarely economically feasible. Manual sorting requires large amounts of space, which often needs to be tightly climate-controlled. Furthermore, rising labour costs and workforce shortages mean that filling vacancies such as potato sorting have become increasingly difficult.
Daniel Bengtson, Software Developer of Newtec Engineering:
"A high-quality optical sorting machine … will be able to run almost 24/7 with little supervision, and at the same time consistently outperform the typical accuracy of human manual sorting."Benefits of optical sorting
The Newtec Optical Sorting Machine, Celox-P-UHD for potatoes uses the patented Newtec roller vibration system to achieve a complete 360⁰ scan.
Daniel Bengtson:
"Products move through the machine while they rotate, presenting the complete surface of the product to the camera as it passes through the inspection section."With simultaneous sorting by quality, size and shape, the optical sorting machine can maintain a consistent rate of production flow. While a higher number of defects in products can slow human sorting, or allow more defective products to slip through, a competent optical sorting machine will be unaffected.
This means that product batches that would not be economical to manually sort can still be profitable when sorted by an optical grader.
Daniel Bengtson:
"Enabling packhouses to squeeze out the final few percent of good quality products from an otherwise bad batch increases the efficiency of food production."The classic Red Green Blue (RGB) sensor cameras cannot detect internal defects, so Newtec’s optical sorting machines take the safer course of action when in ‘doubt’ about an unusual-looking feature or product.
Daniel Bengtson:
"It is usually more economically feasible to let a bad product slip through than to mistakenly discard a good one."However, as sorting requirements can vary amid locations, product batches, and seasons, Newtec machines can easily be adjusted by operators to change the threshold for ‘benefit of the doubt’, as well as other settings for current business requirements.
How can Artificial intelligence AI help with optical sorting?
The ‘sorting algorithms’ used for optical sorting machines are generally defined by physical criteria and surface defects. For example, the criteria used by the Celox-P-UHD for potatoes include length, diameter, volume, roundness, and bad shape. Additionally, new ‘filters’ can be downloaded and installed for different defects and product types.
Daniel Bengtson:
"Such filters already exist for detecting greening, rot, black spots, grey mechanical damage, different kinds of scars, growth cracks, skin discoloration and wrong colour."Artificial intelligence (AI), machine learning and high-performance computing play a large part in optical sorting, as the image stream coming from the cameras must be processed in real-time.
Daniel Bengtson:
"Although this touches on trade secrets, we continually make further developments to utilise the latest developments within AI, computer vision and machine learning."Increasing sustainability by reducing food waste
With a more nuanced quality classification of ‘bad products’, food waste can be reduced, effectively reducing the carbon footprint of a given amount of crops. Furthermore, the ability to sort product batches with a high percentage of bad products means that otherwise uneconomical product batches can still be used.
Newtec’s optical sorting machine, The Celox-P-UHD, can also collect data about products for later analysis. This data can be used to optimise future harvests, increasing overall crop yield while reducing fertiliser and chemical treatment use.
Daniel Bengtson:
"To our knowledge, no other solution exists that is capable of keeping track of every single potato or carrot processed by the Newtec Celox-P-UHD or Celox-C-UHD, respectively."Analysis of a sample from the raw materials can allow growers to adjust the conditions that affect quality, such as planting density and water.
Optimised conditions increase the prospect of a yield that meets the taste, size, appearance, shape and variety demands of manufacturers and supermarket chains.
Optical graders can also work efficiently in smaller and less tightly controlled environments, reducing the amount of energy expended on heating and lighting as compared to manual sorting.
Newtec is ready to deal with emerging sustainability-related developments, delivering highly modular machines that meet customer needs and always allow the operator to make the final call.
Like to receive news like this by email? Join and Subscribe!
Join Our Telegram Channel for regular updates!
Highlighted Company
Sponsored Content
Sponsored Content
Sponsored Content
Sponsored Content
Sponsored Content